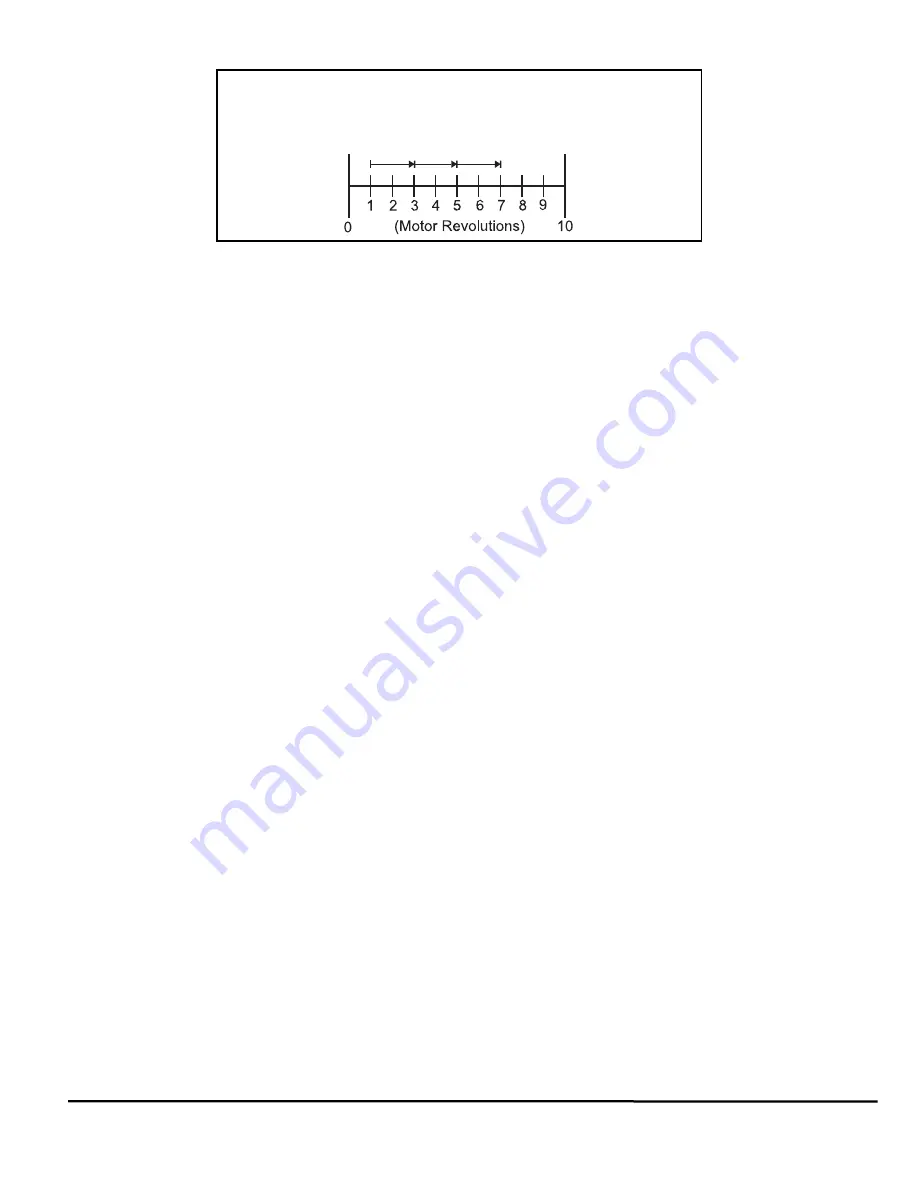
Epsilon EP-P Drive Reference Manual
13
Revision A4
www.controltechniques.com
Figure 26:
Incremental Index Example 2
Correction Indexes
A Correction index is intended to continuously run on the second profile correcting any position drift. It will adjust the motor
position based on changes to it's index.#.dist parameter. The Correction indexes use incremental distance values. Updates to
the index distance while the correction index is executing will take effect immediately by recalculating the index on the fly.
Another words, if this index is in progress and the distance value is changed, the move profile instantaneously recalculates
based on the index's current position, speed and acceleration. Once the Correction index is initiated it will remain active until
stopped by the user with the Profile.#.MotionStop function.
Example: Correction index distance sources are user program calculations, fieldbus inputs or analog input values. The index
distance value can be updated via Fieldbus, by simply writing to the index distance parameter. If the analog input's Destination
Variable is set to the Index.#.Dist parameter, the index's distance value will be updated by the Analog Input. This can be set to
a automatic refresh using the Analog Input view
Posn Tracker Cont and Posn Tracker Once Indexes
Posn Tracker Cont and Posn Tracker Once are indexes which expect their position values to be dynamically changed while
executing. Position Tracker indexes use absolute position values. Posn Tracker Cont index once initiated, will remain active
until stopped by the user with the Profile.#.MotionStop function. The Posn Tracker Once index will accept position changes
until the target position is reached, at which point the index is complete.
The index 's position value can be updated via fieldbus, by simply writing to the index position parameter. Posn Tracker
Indexes are used to follow dynamic changes to the end point of the index prior to and during the index motion. If the analog
input's Destination is set to an Index.#.distance, the index's position value will be updated by the Analog to Position scaling
found in the Analog Input view.
Posn Tracker also accepts on the fly changes to index velocity, acceleration and deceleration. The index is recalculated on the
next trajectory update.
Registration Indexes
A Registration Index is used in applications where the motor must move until an object is detected and then move a specific
distance from the point of detection, such as finding a registration mark and moving a distance beyond.
The Registration Index consists of two parts. The first part accelerates the motor to the target velocity and continues at this
velocity until it receives a registration trigger (sensor or analog). Upon receipt of a registration trigger, the registration offset will
be executed at the target velocity. The Sensor Limit Distance Hit source can be used to turn on an output, if a sensor input or
analog limit is not received within the Limit Distance. A registration window can also be used to determine the validity of a
registration trigger. If a registration trigger is received outside of the registration window, it will be ignored.
Rotary Plus and Rotary Minus Indexes
Rotary Plus and Rotary Minus Indexes provide forced directional control of moves to absolute positions. The position entered
for a Rotary Plus or Minus type index must be within the rotary range (i.e. 0
Position < Rotary Rollover Point). All other
parameters function the same as they do with absolute indexes. An Absolute Index is a direct move to a specific position,
regardless of the starting point. A Rotary Plus Index moves to the specified position, but is forced in a positive direction.
Similarly, a Rotary Minus index moves to the specific position, but is forced in a negative direction.
Rotary Plus and Minus Indexes are usually used in rotary applications, therefore the rotary rollover feature on the Setup -
Position view in the PowerTools Pro software must be enabled to use them.
1.
In the following examples the term “D” = (absolute position specified) - (current position). If “D” is negative,
motion in the negative direction is implied.
2.
In the following examples the Rotary Rollover parameter on the Setup - Position view is set to 360.00°. This
means that with each revolution of the motor (or rotary table), feedback will count up to 359.99°, then roll over
to ذ.
Indexes with Rotary Rollover Enabled
Incremental move distances can be outside of the rotary rollover range. See the "Setting Up Parameters" chapter for an
explanation of Rotary Rollover.
Example 1:
If the starting position is at ذ and 720° is the specified distance, an Incremental index would move 2 revolutions
in the positive direction. At the completion of this index the motor position would be ذ.
Absolute indexes will take the shortest path to the specified position. Absolute index positions must be within the rotary
Incremental Index
Start Position = 1 Rev
Index Distance = 2 Revs
Содержание Epsilon EP-P
Страница 2: ......
Страница 14: ...xii Epsilon EP P Drive Reference Manual www controltechniques com Revision A4 Glossary 225 Index 231...
Страница 124: ...110 Epsilon EP P Drive Reference Manual www controltechniques com Revision A4...
Страница 200: ...186 Epsilon EP P Drive Reference Manual www controltechniques com Revision A4...
Страница 218: ...204 Epsilon EP P Drive Reference Manual www controltechniques com Revision A4...
Страница 238: ...224 Epsilon EP P Drive Reference Manual www controltechniques com Revision A4...
Страница 244: ...230 Epsilon EP P Drive Reference Manual www controltechniques com Revision A4...
Страница 247: ......