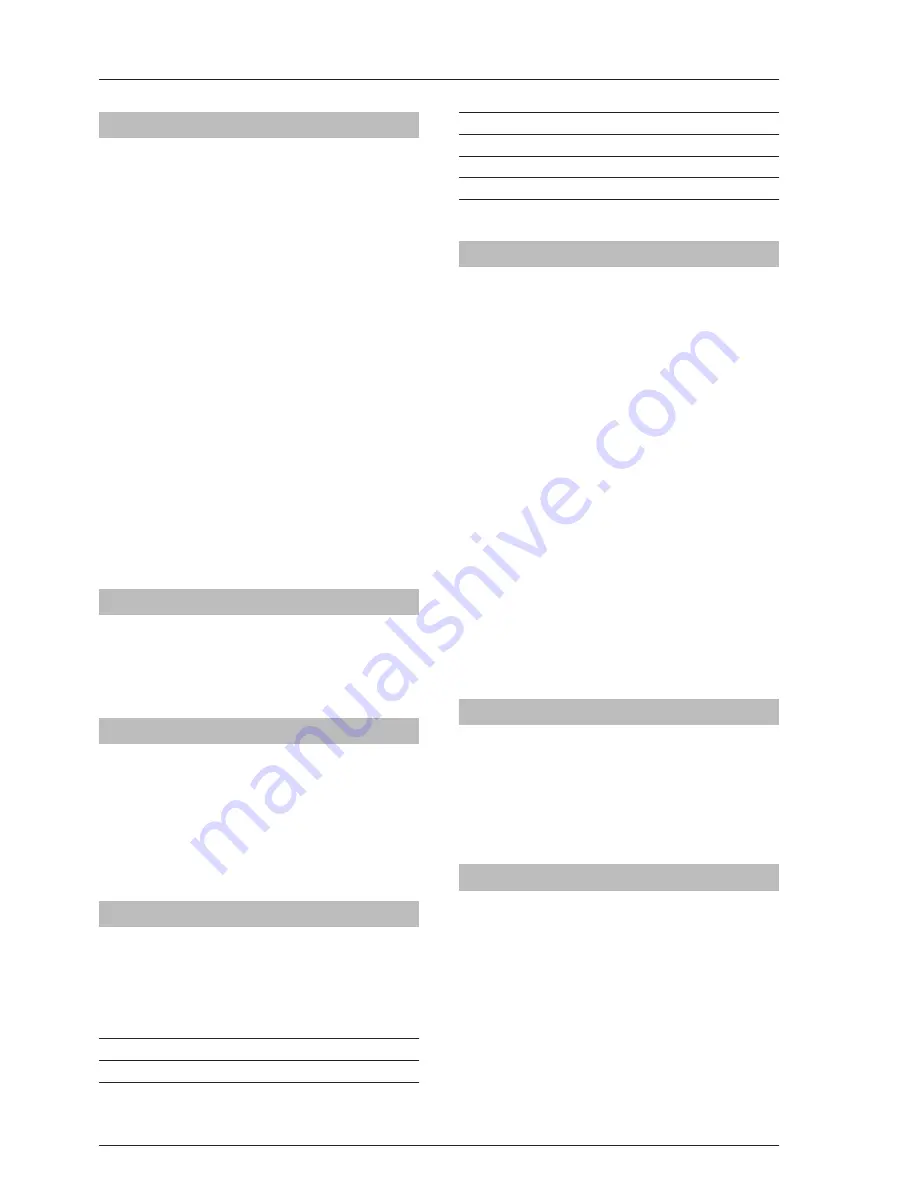
6
3�5 Venting
For quick venting during filling and commissioning the
intermediate modules have 1/2"-fittings with caps and the
end modules have manual air vents. The manual air vents
are accessible when the store is insulated. In operation,
the venting of the store takes place preferably through it’s
top connections: For permanent trouble-free operation of
the system—in particular in connection with a fresh water
station—it is highly recommended to fit an air separator at
the top outlet of the store.
NOTE:
Install pipe of a large size and height to ensure
good flow calming for ventilation. It is effective to have an
additional air seperator in the flow line between boiler and
store because in this area gases—dissolved by the temper-
atures—increasingly emerge as bubbles. Alternatively or
in addition a temporary vacuum degassing with a mobile
device can be performed during commissioning to degas
the entire system. The recommended procedure is described
in the guideline VDI 4708 sheet 2 ‘pressure maintenance,
ventilation, degassing; ventilation and degassing’. After the
ventilation phase (approx. 2 weeks), the system pressure
should be re-examined and water refilled if necessary.
3�6 Temperature sensor
Sensor terminal positions are on the end modules. Here
the heated volume can be set by the varying height of the
sensor, and temperatures measured.
3�7 Electric auxiliary heating
An external heating group preferably with a speed-con-
trolled pump and electric heating element is used for the
electric auxiliary heating of the buffer water, such as in
the context of power to heat. => See Hydraulic schematic.
Heating elements must be equipped with a safety limiter
according to EN 60335 part 1 and 2.
3�8 Materials
The buffer range is free of PVC, CFC, HFC and fiber insulat-
ing materials. Materials used and their weightings in a store
with three modules (4 000 l):
Steel
709,6 kg
91,1%
EPS
22,5 kg
2.9%
EPS-EPE copolymer
2,9 kg
0,4%
PET fleece
18,1 kg
2.3%
PS
12 kg
1,5%
PA
4,7 kg
0,6%
Stainless steel
4,7 kg
0,6%
EPDM
4 kg
0.5%
3�9 Installation location
Prior to installation of the store, the static load bearing
capacity of the ground must be checked. The weight of
the filled store including the attached accessories must not
exceed the maximum permissible floor or ceiling load!
The required, permitted minimum loading of the floor is
0.35 N/mm².
The area where the store will be sited must be level and
ensure a permanently vertical installation. Some unevenness
can be compensated for by means of the supplied floor rails
and levelling compound (see assembly instructions). The
store should be placed in a room with water drainage or
with some other consideration.
The unit must be installed in a frost-proof room. Pipes
should be as short as possible and frost-proofed. Also the
outlet of the pressure blow-off pipe must be in a frost-
proofed area.
The spacing must be chosen to walls, ceilings, and immov-
able obstructions, so that ease of Assembly and disassem-
bly, inspection, and maintenance are possible. Applicable
standards and technical rules must be observed!
3�10 Standards
The buffer class contains vertical stores of S 235 and S
355 according to DIN 17100 with quality certification. The
containers comply with DIN 4753 for heating water storage
in heating systems with flow temperatures up to 90 °C,
according to DIN 4751 part 1.
3�11 Notice of withdrawal
The store can be returned to the manufacturer at the end of
life. It is also possible to recycle locally. A final decommis-
sioning or disposal is permitted only by authorized person-
nel. The materials must be disposed of according to current
national and the relevant locally applicable environmental
laws and regulations.
T D M A - VA R I C A L :
Planing aids