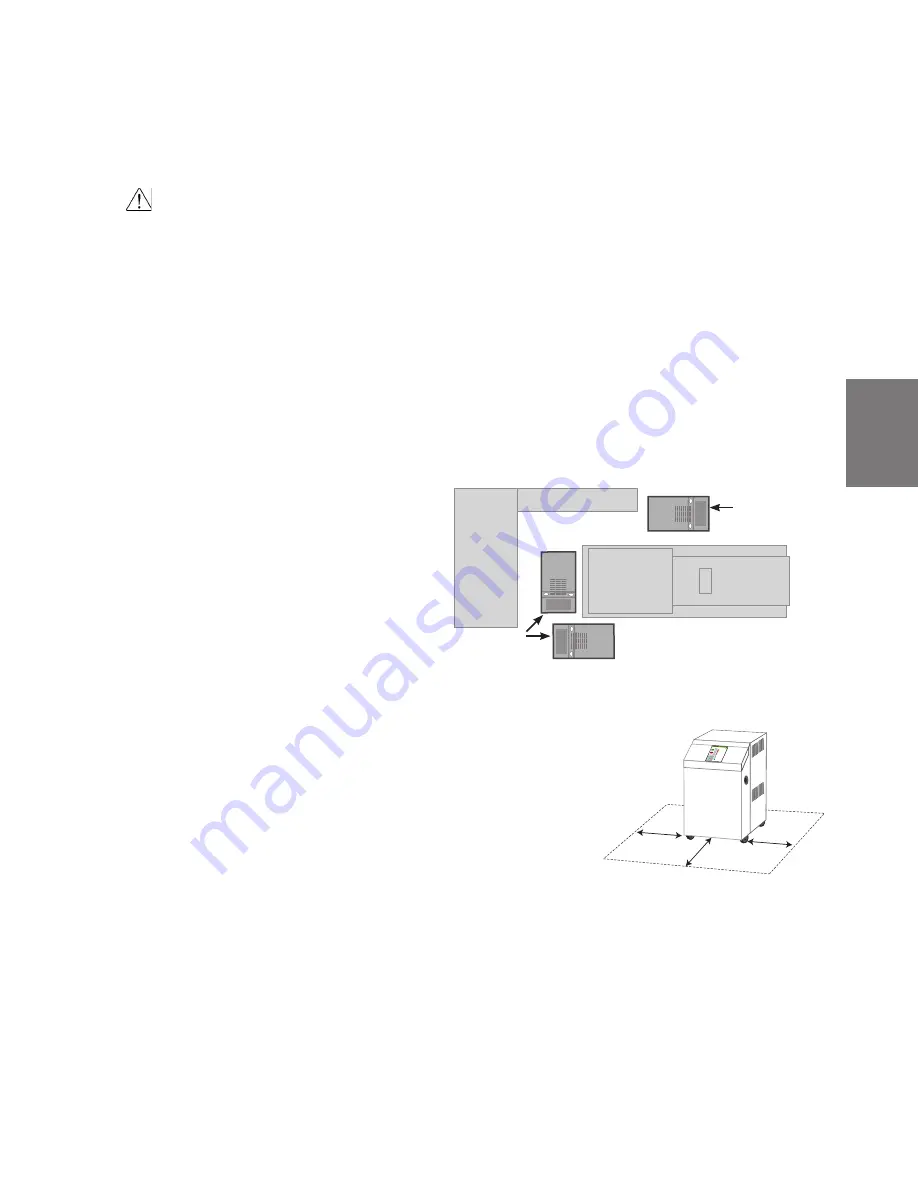
Installation
I
3-3
3
Installa
tion
Preparing for Installation
The Thermolator is easy to install, if you plan the location and prepare the area properly.
WARNING: Improper installation, operation, or servic-
ing may result in equipment damage or personal
injury.
This equipment should only be installed, adjusted, and serviced by qualified tech-
nical personnel who are familiar with the construction, operation, and potential
hazards of this type of machine.
All wiring, disconnects, and fuses should be installed by qualified electrical
technicians in accordance with electrical codes in your region. Always maintain
a safe ground. Do not operate the equipment at power levels other than what is
specified on the machine serial tag and data plate.
1
Position the Thermolator as close to the process machine as possible.
2
Make sure the installation area provides
:
r
A three-phase power source supplying the
correct current for your Thermolator model.
Check the serial tag on the unit for required
voltage, phase, frequency, and full load amps.
Check the last page of the electrical power
prints for the disconnect fuse size and mini-
mum wire connection size. All wiring should
be completed by qualified personnel and should
comply with your region’s electrical codes.
r
A clean, well-ventilated environment.
The room temperature should not
exceed 104° F {40° C} with 95% non-condensing humidity and should not fall
below 32° F {0° C}.
r
Minimum clearance for safe operation and maintenance.
The diagram at
the right shows minimum clearance for operation. You also need enough
clearance in rear for water hookups. For maintenance, you should move
the Thermolator to provide at least 36 inches {91 cm} on any side of the
Thermolator. Additionally, your required electrical codes may require a
larger service area in front of the electrical panel.
r
A source of water for cooling.
City, tower or chiller water may be
used, as long as the supply pressure is at least
25
psi and not more than 95 psi
for most units;
refer to the appendix for more information on 48 kW and 300° F
{149° C} units.
3
Install plumbing for process and cooling lines.
You will need two 1
1
/
2
-inch NPT male fittings for the process inlet and outlet and
two 1-inch NPT male fittings for the cooling inlet and outlet. Larger line sizes are
acceptable as long as they are reduced at the Thermolator connections. Smaller line
sizes are not recommended.
Mold
Purge
Rapid
Cool
Process
Cool Down
Control Power
Autostart Signal
Pump
Heat
Cool
Coolant Pressure
Temperature Limit
Electrical Phase Error
Heat Error
Process Cool Down
Rapid Cool
Communications
Remote Heat/Cool
Program Mode
Mold Purge
Flow GPM (flash)
12 inches
{305 mm}
12 inches
{305 mm}
20 inches
{508 mm}
Thermolator
Process
Machine
Alternate
locations
Содержание Thermolator TW-P
Страница 6: ...iv I Table of Contents ...
Страница 12: ...1 6 I Introduction ...
Страница 36: ...3 14 I ...
Страница 58: ...4 22 I Operation ...
Страница 72: ...5 14 I Maintenance ...
Страница 128: ...E 4 I Appendix ...
Страница 134: ...G 4 I Appendix ...
Страница 136: ...H 2 I Appendix ...