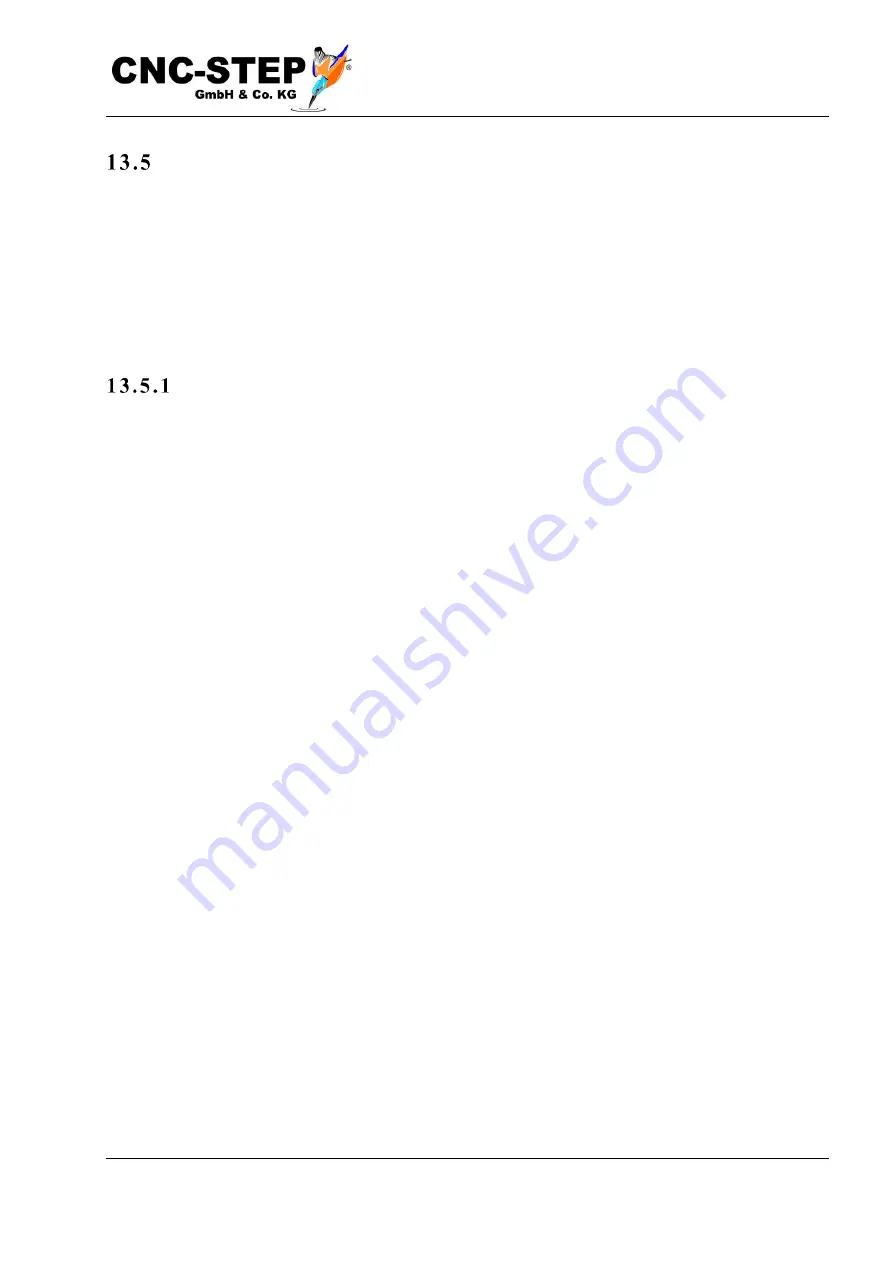
KinetiC-NC
User Manual
CNC-STEP GmbH & Co. KG ▪ Siemensstrasse 13-15 ▪ 47608 Geldern ▪ Germany
Page 98
Support: +49 (0)2831/91021-50
10.11.2018
T o o l ma n a g e me n t
Why?
As soon as you need more than just one tool per workpiece, you have to think about how to make it
happen that, despite different lengths, diameters and shapes, the machining is done in the right place
and the right plunge depth. That means, the controller must "know" which tool is currently in the
machine and how long and thick it is, etc. There are different tool change methods that require
different approaches.
Without tool change
This is the simplest case. Only one tool is used per CNC program. This sounds like a drastic
limitation, but it's not that bad when it comes to CNC machining, at least if you only work on thin
plate material. You can, for example, to produce holes with different diameters, select a tool to
match the smallest hole, and mill for the larger one circle. In this way, one often gets amazingly far
with a single tool.
1 3 . 5 . 1 . 1
Distri bution of the progra m
If you need several tools in succession, the processing is divided into several programs. Each
processing step is carried out separately. In between, the tool is changed manually and then the zero
point is re-measured. In this case you only need a single tool (T1) in the tool list. You can enter the
tool data in the list (menu "Configuration -> Tools"), but this is only relevant for the display on the
screen. Since the workpiece offset is re-measured after each change, the entered tool length is
irrelevant, and you do not have to worry about the tool number. The setting in „
" is best set to "Ignore tool change" to avoid unnecessary requests to change
tools. You have to have the tool anyway before the start suitable for the program have changed.