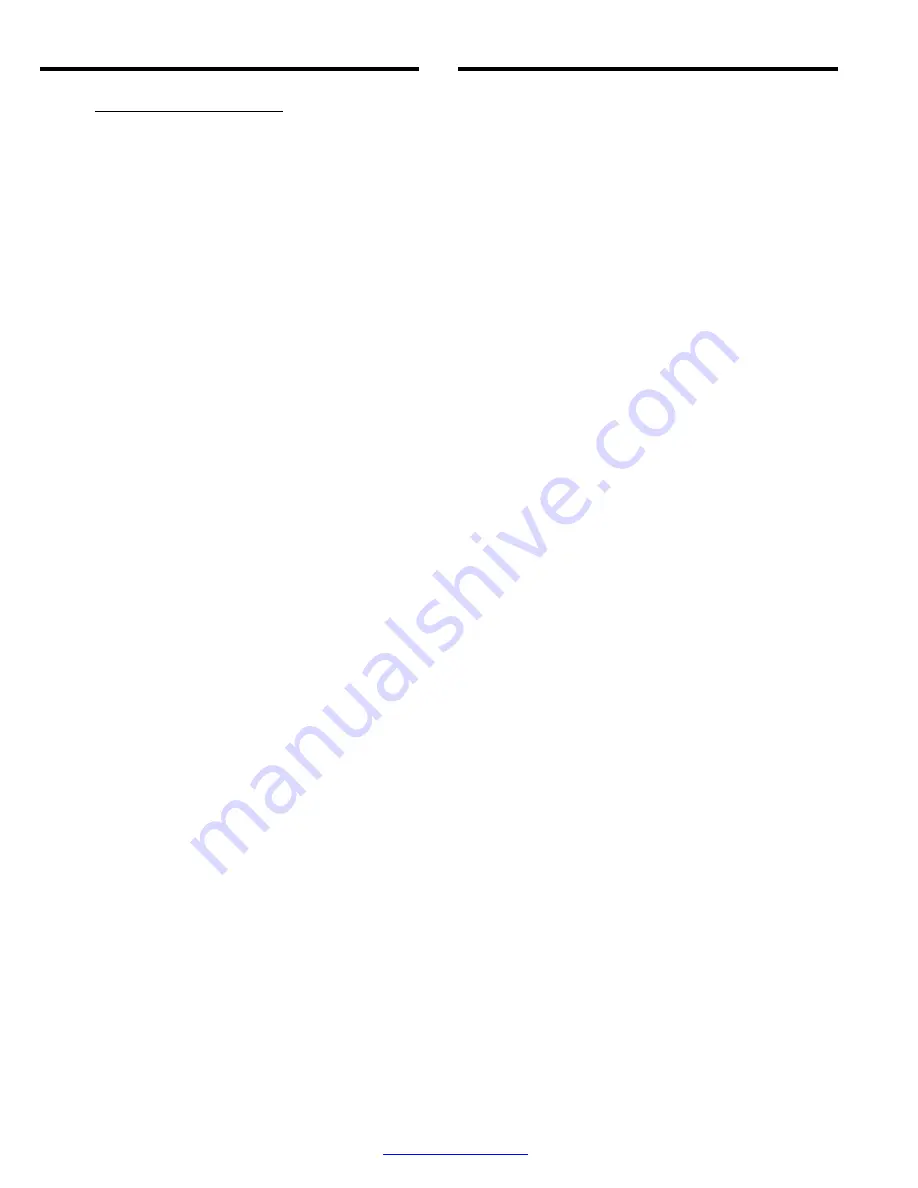
BNP
®
55 SUCTION BLAST CABINET
Page 26
© 2019 CLEMCO INDUSTRIES CORP.
www.clemcoindustries.com
Manual No. 23350, Rev G, 02/19
8.1.6
Cabinet air-inlet damper closed too far,
restricting air movement through the cabinet. Adjust
damper, per Section 2.6 and 5.6.
8.1.7
Reclaimer door open. Check door.
8.1.8
Hole worn in flex hose between cabinet hopper
and reclaimer inlet or between the reclaimer and dust
collector. Replace hose and route it with as few bends
as possible to prevent wear.
8.1.9
Obstruction in flex hose between the cabinet
hopper and reclaimer inlet. Inspect flex hose for
blockage
8.2
Abnormally high media consumption
8.2.1
Door on reclaimer open or worn door gasket.
Air entering the reclaimer around the door will cause
media carry over to the dust collector. Inspect door
gasket. DO NOT operate unless all doors are closed.
8.2.2
Dust-collector damper open too far. Adjust
static pressure, per Section 5.4.
8.2.3
Media may be too fine or worn-out. Check
condition of media.
8.2.4
Using friable media that rapidly breaks down.
Check condition of media.
8.2.5
Blast pressure too high for the media, causing
media to breakdown. Check blast pressure and adjust
as needed or switch media.
8.2.6
Hole worn in reclaimer or leak in reclaimer
seams. Check entire reclaimer for negative-pressure
leaks.
8.2.7
When using media finer than 180-mesh, as
noted in Paragraph 1.9.6, the inlet baffle of the
reclaimer may need to be removed. Refer to Section
7.10.
8.2.8
Optional, externally adjustable vortex cylinder
out of adjustment. Refer to Section 5.5.
8.3
Reduction in blast cleaning rate
8.3.1
Low media level reducing media flow. Check
media level and replenish or replace as needed.
8.3.2
Media-air mixture out of adjustment. Adjust
metering valve, per Section 5.3.
8.3.3
Reduced air pressure. This may be caused by
the pressure regulator set too low, a malfunctioning
regulator, a dirty filter element in the air filter, partially
closed air valve, leaking air line, or other air tools in
use. Inspect all items.
8.3.4
Blockage in media hose or gun. Blockage may
occur because of:
A damaged or missing reclaimer screen; inspect
screen.
Heavy media flow. Adjust media flow, per Section
5.3.
8.3.5
Worn gun parts such as nozzle or air jet.
Inspect and replace all worn parts.
8.3.6
Worn media hose. Check hose for leaks and
soft spots. Replace worn or damaged hose.
8.3.7
Air jet out of adjustment. Check adjustment,
per Section 5.2.
8.3.8
Moist media. Frequent bridging or blockage in
the area of the metering valve can be caused by
moisture. Refer to Section 8.5.
8.4
Plugged nozzle
8.4.1
A damaged or missing reclaimer screen will
allow large particles to pass and block the nozzle.
Replace or reinstall as necessary.
8.4.2
Media mixture too rich. Adjust media-air
mixture, per Section 5.3.
8.5
Media bridging
8.5.1
Frequent bridging or blockage in the media
metering valve can be caused by damp media. Media
becomes damp from blasting parts that are slightly oily,
from moisture in the compressed-air line, or from
absorption from ambient air.
8.5.2
To avoid contaminating media from the
workpiece, all parts put into the cabinet should be
clean and dry. If parts are oily or greasy, degrease and
dry them prior to blasting.