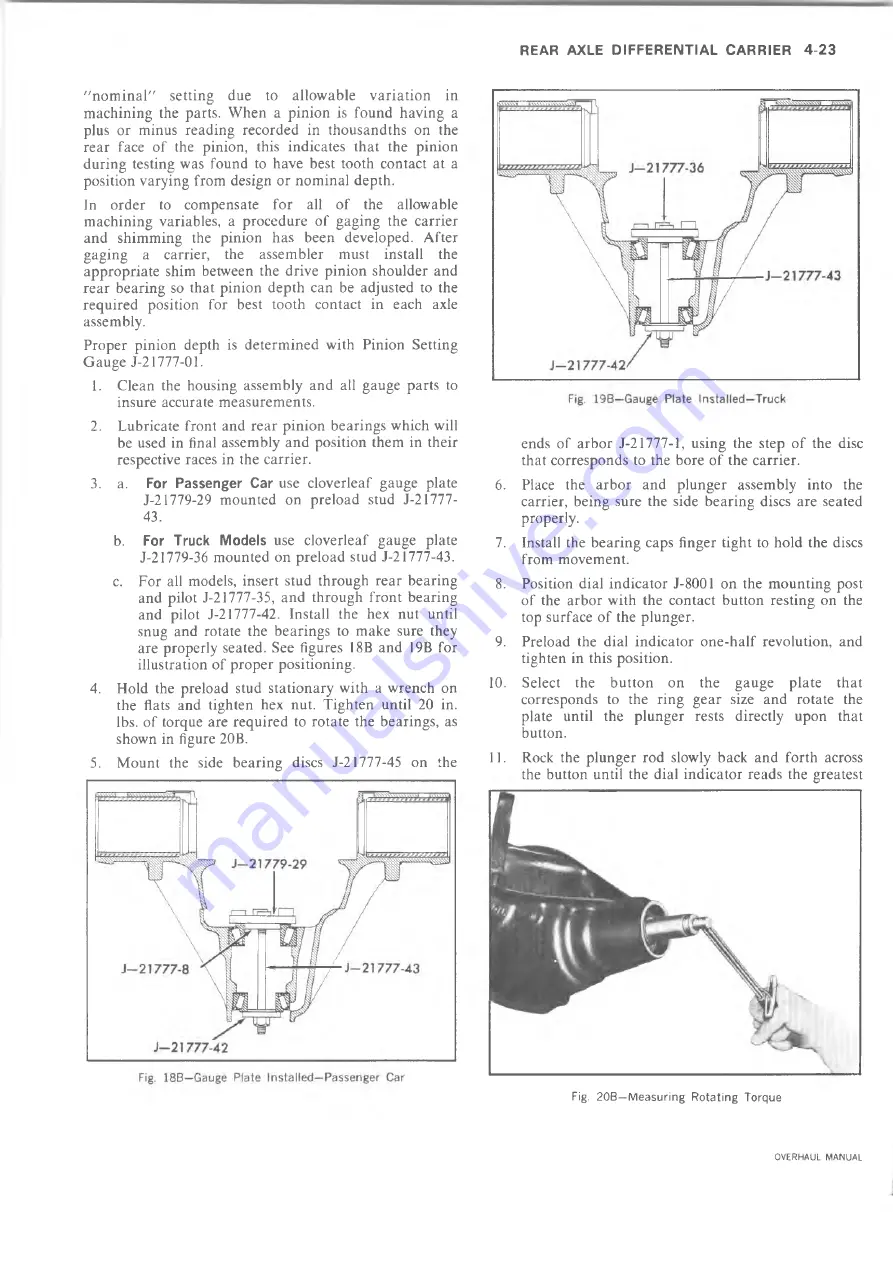
REAR AXLE DIF FER EN TIA L CARRIER 4 -2 3
"nominal" setting due to allowable variation in
machining the parts. When a pinion is found having a
plus or minus reading recorded in thousandths on the
rear face of the pinion, this indicates that the pinion
during testing was found to have best tooth contact at a
position varying from design or nominal depth.
In order to compensate for all of the allowable
machining variables, a procedure of gaging the carrier
and shimming the pinion has been developed. After
gaging a carrier, the assembler must install the
appropriate shim between the drive pinion shoulder and
rear bearing so that pinion depth can be adjusted to the
required position for best tooth contact in each axle
assembly.
Proper pinion depth is determined with Pinion Setting
Gauge J-21777-01.
1. Clean the housing assembly and all gauge parts to
insure accurate measurements.
2. Lubricate front and rear pinion bearings which will
be used in final assembly and position them in their
respective races in the carrier.
3. a.
For Passenger Car
use cloverleaf gauge plate
J-21779-29 mounted on preload stud J-21777-
43.
b.
For Truck Models
use cloverleaf gauge plate
J-21779-36 mounted on preload stud J-21777-43.
c. For all models, insert stud through rear bearing
and pilot J-21777-35, and through front bearing
and pilot J-21777-42. Install the hex nut until
snug and rotate the bearings to make sure they
are properly seated. See figures 18B and 19B for
illustration of proper positioning.
4. Hold the preload stud stationary with a wrench on
the flats and tighten hex nut. Tighten until 20 in.
lbs. of torque are required to rotate the bearings, as
shown in figure 20B.
5. Mount the side bearing discs J-21777-45 on the
ends of arbor J-21777-1, using the step of the disc
that corresponds to the bore of the carrier.
6. Place the arbor and plunger assembly into the
carrier, being sure the side bearing discs are seated
properly.
7. Install the bearing caps finger tight to hold the discs
from movement.
8. Position dial indicator J-8001 on the mounting post
of the arbor with the contact button resting on the
top surface of the plunger.
9. Preload the dial indicator one-half revolution, and
tighten in this position.
10. Select the button on the gauge plate that
corresponds to the ring gear size and rotate the
plate until the plunger rests directly upon that
button.
11. Rock the plunger rod slowly back and forth across
the button until the dial indicator reads the greatest
Fig. 20B —M easuring R o ta tin g Torque
OVERHAUL MANUAL
Содержание 10 series 1973
Страница 1: ......
Страница 3: ...r...
Страница 5: ......
Страница 21: ......
Страница 31: ......
Страница 34: ...REAR AXLE DIFFERENTIAL CARRIER 4 3 OVERHAUL MANUAL...
Страница 85: ...4 54 REAR AXLE DIFFERENTIAL CARRIER OVERHAUL MANUAL...
Страница 93: ...4 62 REAR AXLE DIFFERENTIAL CARRIER OVERHAUL MANUAL...
Страница 103: ...V...
Страница 141: ...I...
Страница 144: ...ENGINE 6 3 OIL PRESSURE SENDING UNIT Fig 1 In Line Engine Lubrication OVERHAUL MANUAL...
Страница 145: ...6 4 ENGINE FUEL PUMP PUSH ROD OILING OIL FILTER AND BY PASS VALVE Fig 2 Sm all V8 Engine Lubrication OVERHAUL MANUAL...
Страница 179: ......
Страница 185: ...6M 6 CARBURETORS Fig M6 Monojet See Fig M7 for legend...
Страница 219: ...L...
Страница 247: ...7 M 28 CLUTCHES AND MANUAL TRANSMISSIONS Fig 19X Loading Countergear Bearings Fig 20X Loading Mainshaft Pilot Bearings...
Страница 289: ...7M 70 CLUTCHES AND MANUAL TRANSMISSIONS Fig 13F Transfer Case Exploded View OVERHAUL MANUAL...
Страница 352: ...AUTOMATIC TRANSMISSION 7A 49 Fig 85M Planetary Gear Train Exploded View OVERHAUL MANUAL...
Страница 363: ...7A 60 AUTOMATIC TRANSMISSION Fig IT S ide Cross Section Typical OVERHAUL MANUAL...
Страница 457: ......
Страница 459: ......
Страница 522: ......