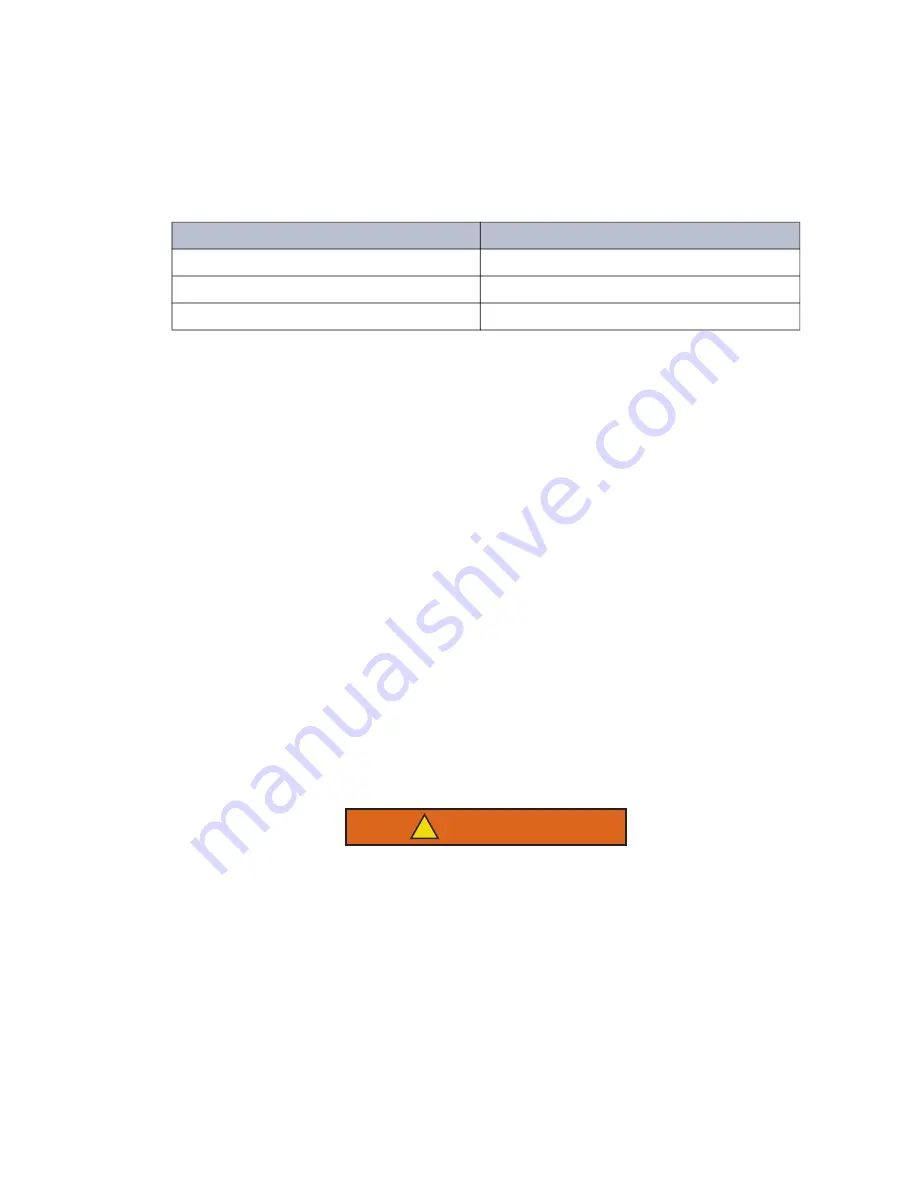
7–9
T-340
13. Cut and discard the wire ties used to hold the base plate to the compressor.
14. Place the new SST washers on each side of the resilient mounts, and the new Mylar washer on the bottom
of it (see
). Install the four base mounting bolts loosely.
15. Place the new Teflon seals at the compressor suction and discharge ports as well as the O-rings at the
unloader and economizer line connection ports. Hand tighten all four connections.
16. Torque the four base-mounting screws to 6.2 mkg (45 ft- lbs).
17. Torque the compressor ports / connections to:
18. Connect (butt-splice and heat shrink) the new compressor dome temperature sensor with the old sensor
wires removed in step h. Wire-tie any loose wiring as appropriate.
19. Evacuate the compressor to 1000microns if the unit was pumped down before the replaced compressor
was removed. Otherwise, evacuate the complete unit and charge it with R-134a refrigerant (see
).
20. Open the compressor terminal cover and connect the compressor power cable following the steps below:
a. Liberally coat the orange gasket surfaces with the Krytox lubricant.
b. Install the orange gasket part onto the compressor fusite with the grooved or threaded side out. Ensure
that the gasket is seated onto the fusite base.
c. Coat the inside of the power plug (female) connector pins with the Krytox lubricant, and insert the plug
onto the compressor terminal connections. Make sure the orange gasket has bottomed out onto the
fusite and it fits securely onto the terminal pins while fully inserted into the orange plug.
d. Connect the green ground wire to the grounding tab located inside the terminal box of the compressor
using the self-tapping grounding screw. Close the compressor terminal box using the terminal cover
removed in step t.
21. Backseat all service valves, connect the power to the unit and run it for at least 20 minutes.
22. Perform a leak check of the system.
7.9 High Pressure Switch
7.9.1
Checking High Pressure Switch
WARNING
!
Do not use a nitrogen cylinder without a pressure regulator.
NOTE
The high pressure switch is non-adjustable.
1. Remove the switch (see
).
2. Connect ohmmeter or continuity light across switch terminals. Ohmmeter will indicate no resistance or con
-
tinuity light will be illuminated if the switch closed after relieving compressor pressure.
3. Connect hose to a cylinder of dry nitrogen (see
).
Service Valve / Connection
Torque Value
Suction and Discharge Rotalocks
108.5 to 135.5 Nm (80 to 100 ft-lbs.)
Unloader connection
24.5 to 27 Nm (18 to 20 ft-lbs.)
Economized connection
32.5 to 35 Nm (24 to 26 ft-lbs.)
Содержание Transicold 69NT40-561-001
Страница 2: ......
Страница 4: ......
Страница 14: ......
Страница 22: ......
Страница 36: ......
Страница 92: ......
Страница 159: ...7 47 T 340...
Страница 163: ...8 3 T 340 Figure 8 2 Schematic Diagram for Standard Unit Configuration Based on Drawing 62 11271 Rev A...
Страница 169: ...8 9 T 340 Figure 8 8 Schematic and Diagram for Lower Vent Position Sensor VPS Option...
Страница 170: ...T 340 8 10 Figure 8 9 Unit Wiring Diagram for Standard Unit Configuration With 3 Phase Condenser Fan Motors...
Страница 172: ...T 340 8 12 Figure 8 10 Unit Wiring Diagram for Single Phase Condenser Fan Motor and Optional Heater...
Страница 173: ...8 13 T 340 Unit Wiring Diagram for Single Phase Condenser Fan Motor and Optional Heater Based on Drawing 62 66721...
Страница 174: ...T 340 8 14 Figure 8 11 Unit Wiring Diagram for Configuration With eAutoFresh and Emergency Bypass Options...
Страница 176: ......
Страница 180: ......
Страница 181: ......