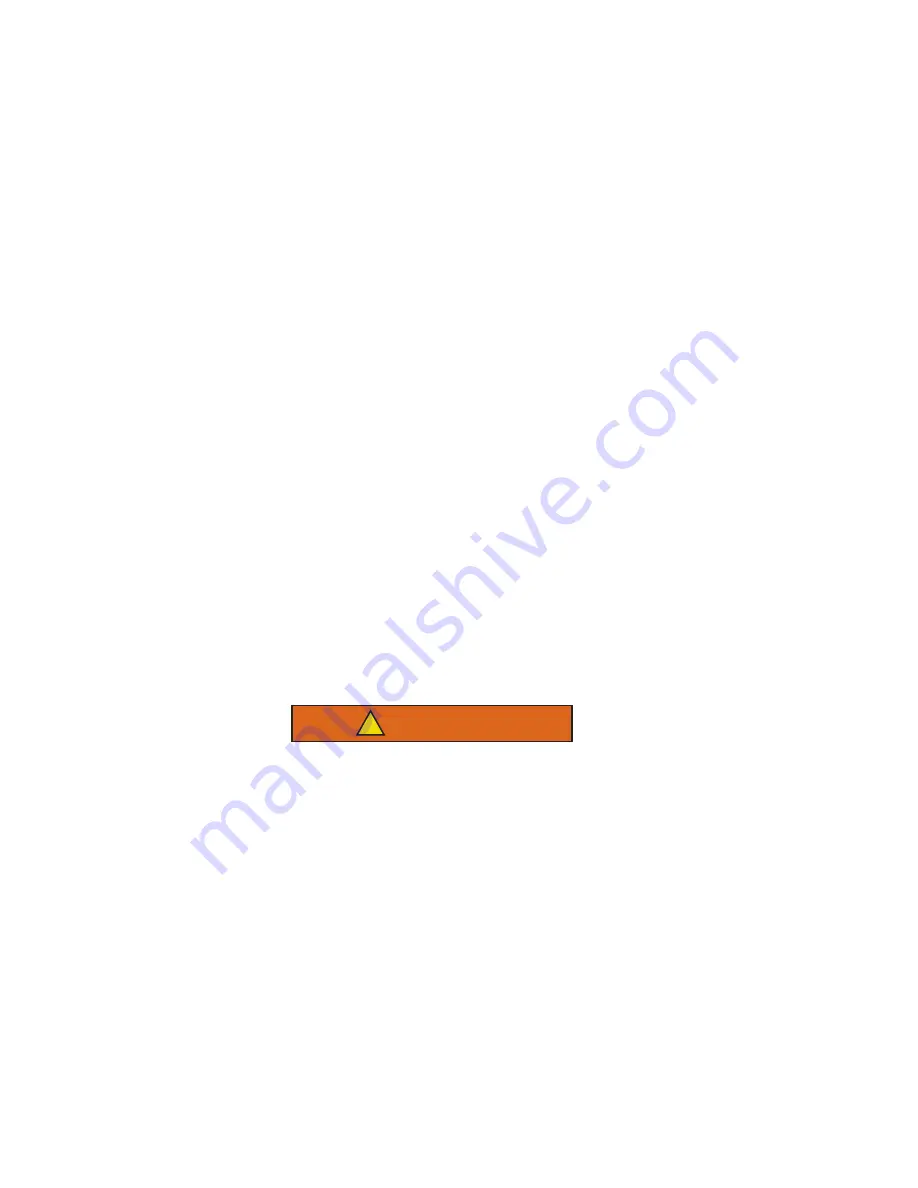
T-340
7–6
2. The recommended method to evacuate and dehydrate the system is to connect evacuation hoses at the
compressor suction and liquid line service valve (see
). Be sure the service hoses are suited for
evacuation purposes.
3. Test the evacuation setup for leaks by backseating the unit service valves and drawing a deep vacuum with
the vacuum pump and gauge valves open. Shut off the pump and check to see if the vacuum holds. Repair
leaks if necessary.
4. Midseat the refrigerant system service valves.
5. Open the vacuum pump and electronic vacuum gauge valves, if they are not already open. Start the vacuum
pump. Evacuate unit until the electronic vacuum gauge indicates 2000 microns. Close the electronic vac
-
uum gauge and vacuum pump valves. Shut off the vacuum pump. Wait a few minutes to be sure the vac
-
uum holds.
6. Break the vacuum with either clean dry refrigerant 134a or dry nitrogen. Raise system pressure to roughly
0.14 bar (2 psig), monitoring it with the compound gauge.
7. Remove refrigerant using a refrigerant recovery system.
8. Repeat steps e. and f. one time.
9. Remove the copper tubing and change the filter drier. Evacuate unit to 500 microns. Close the electronic
vacuum gauge and vacuum pump valves. Shut off the vacuum pump. Wait five minutes to see if vacuum
holds. This procedure checks for residual moisture and/or leaks.
10. With a vacuum still in the unit, the refrigerant charge may be drawn into the system from a refrigerant con
-
tainer on weight scales.
7.6.4
Evacuate and Dehydrate - Partial System
1. If refrigerant charge has been removed from the low side only, evacuate the low side by connecting the
evacuation set-up at the compressor suction valve and the liquid service valve but leave the service valves
frontseated until evacuation is completed.
2. Once evacuation has been completed and the pump has been isolated, fully backseat the service valves to
isolate the service connections and then continue with checking and, if required, adding refrigerant in accor
-
dance with normal procedures.
7.7 Refrigerant Charge
WARNING
!
EXPLOSION HAZARD Failure to follow this WARNING can result in death, serious personal
injury and / or property damage. Never use air or gases containing oxygen (O
2
) for leak testing
or operating the product. Charge only with R- 134a: Refrigerant must conform to AHRI Stan
-
dard 700 specification.
7.7.1
Checking the Refrigerant Charge
NOTE
Use a refrigerant recovery system whenever removing refrigerant.When working with refrigerants you must
comply with all local government environmental laws. In the U.S.A., refer to EPA Section 608.
1. Connect the gauge manifold to the compressor discharge and suction service valves. For units operating on
a water cooled condenser, change over to air cooled operation.
2. Bring the container temperature to approximately 0°C (32°F) or below. Then set the controller set point to -
25°C (-13°F).
3. Partially block the condenser coil inlet air. Increase the area blocked until the compressor discharge pres
-
sure is raised to approximately 12.8 bar (185 psig).
4. On units equipped with a receiver, the level should be between the glasses. On units equipped with a water-
cooled condenser, the level should be at the center of the glass. If the refrigerant level is not correct, con
-
tinue with the following paragraphs to add or remove refrigerant as required.
Содержание Transicold 69NT40-561-001
Страница 2: ......
Страница 4: ......
Страница 14: ......
Страница 22: ......
Страница 36: ......
Страница 92: ......
Страница 159: ...7 47 T 340...
Страница 163: ...8 3 T 340 Figure 8 2 Schematic Diagram for Standard Unit Configuration Based on Drawing 62 11271 Rev A...
Страница 169: ...8 9 T 340 Figure 8 8 Schematic and Diagram for Lower Vent Position Sensor VPS Option...
Страница 170: ...T 340 8 10 Figure 8 9 Unit Wiring Diagram for Standard Unit Configuration With 3 Phase Condenser Fan Motors...
Страница 172: ...T 340 8 12 Figure 8 10 Unit Wiring Diagram for Single Phase Condenser Fan Motor and Optional Heater...
Страница 173: ...8 13 T 340 Unit Wiring Diagram for Single Phase Condenser Fan Motor and Optional Heater Based on Drawing 62 66721...
Страница 174: ...T 340 8 14 Figure 8 11 Unit Wiring Diagram for Configuration With eAutoFresh and Emergency Bypass Options...
Страница 176: ......
Страница 180: ......
Страница 181: ......