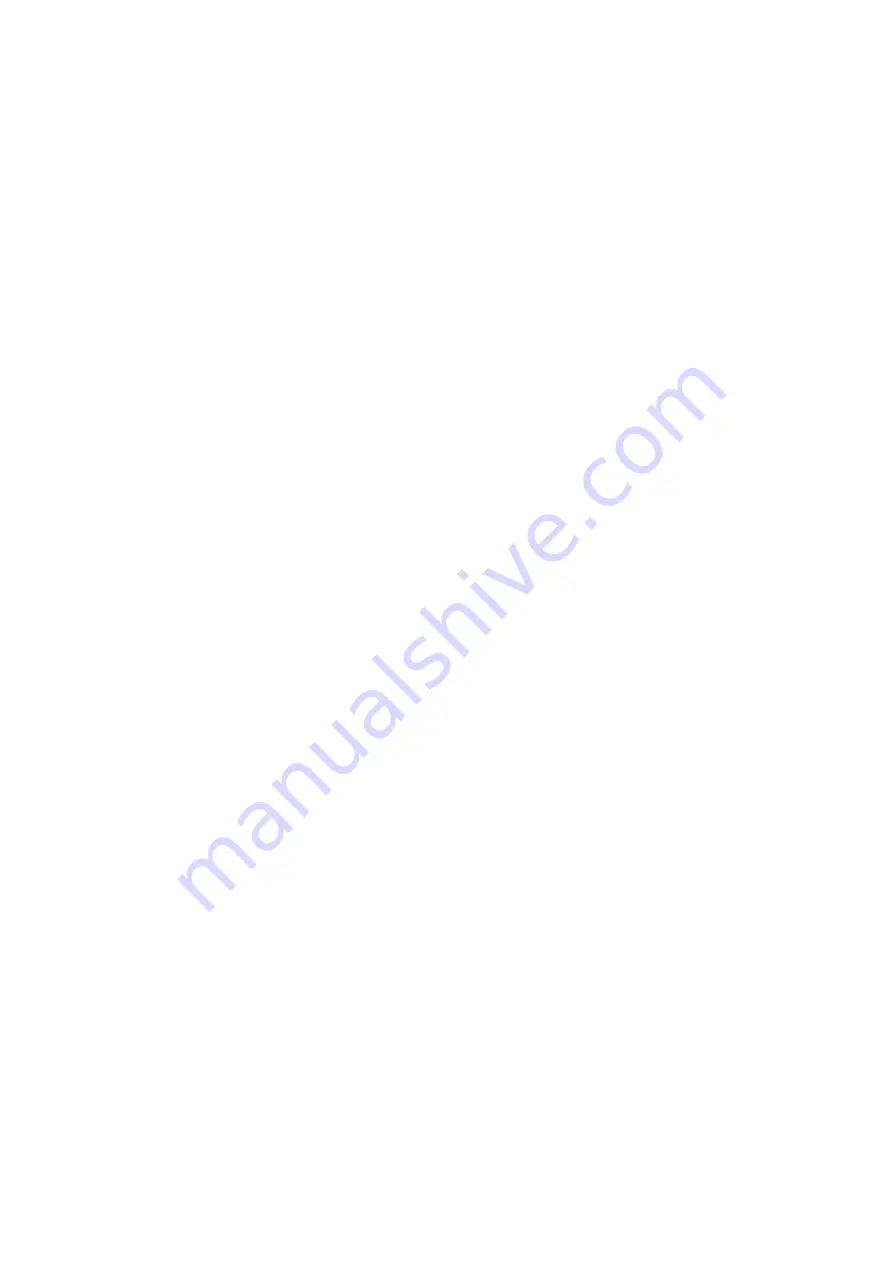
105
4- Reconnect the pressure switch.
Switch off the power supply by acting on the QF1 circuit breaker.
Wait at least 5 seconds
Put the power supply back on the circuit breaker QF1.
Reset the safety relay by pressing the reset button.
Na
5- Check that the PWR, IN and OUT LED of the safety relay K4 is on.
Check that the contactor tap K101 is depressed.
Test n°2 :
Steps :
OK
NOK
1- Machine under tension with K101 closed.
2- Disconnect the NC contact signal from the K101 from the S-33 terminal of the TBS
terminal block
Na
3- Disconnect an active pressure switch by opening its disconnect terminal on TBS main
terminal (SP1FA = S-11 ; SP1FB= S-12 ; SP2FA = S-21 ; SP2FB = S-22).
Na
4- Check that the OUT LED of the safety relay K4 is off.
5- Check that the contactor tap K101 is not depressed.
6- Close the disconnect terminal of the pressure switch wiring
Switch off the power supply by acting on the QF1 circuit breaker.
Wait at least 5 seconds
Put the power supply back on the circuit breaker QF1.
Reset the safety relay by pressing the reset button.
Na
7- Check that the OUT LED of the safety relay K4 is still off.
8- Check that the K101 contactor tap is still not depressed.
9- Reconnect the NC contact
Na
10- Reset the safety relay by pressing the reset button.
Na
11- Check that the PWR, IN and OUT LED of the safety relay K4 is on.
Check that the contactor tap K101 is depressed
Table 21
– Safety chain check
9.3.11
– Compressor bearing maintenance
The key to good bearing maintenance is proper lubrication. Inspect the lubrication system regularly and
thoroughly. Annual vibration measurements are recommended to monitor overall compressor status. Annual
refrigerant analysis is recommended to monitor refrigerant acid and moisture levels over time.
Excessive bearing wear can sometimes be detected through increased vibration or increased bearing
temperature. To inspect the bearings, a complete compressor teardown is required.
Only a trained service technician should perform a compressor disassembly. Bearings cannot be field inspected;
excessive vibration is the primary sign of wear or damage. If either symptom appears, contact an experienced and
responsible service organization for assistance.
Annual compressor vibration analysis and trending is recommended for compressor preventative monitoring and
maintenance.
CAUTION: If compressor requires disassembly, cleanliness is of critical importance to avoid contamination. Small
amounts of contamination can result in damage to ceramic bearings.
Содержание PIC 5+
Страница 26: ...26 VFD not shown Fig 13 Sensors actuators location ...
Страница 52: ...52 Fig 24 19DV control box ...
Страница 53: ...53 1 Power supply 24V AC 2 LEN 3 CCN 4 Ethernet 5 USB Fig 25 19DV HMI box rear view ...
Страница 54: ...54 Fig 26 19DV IOB1 wiring Fig 27 19DV IOB2 wiring ...
Страница 57: ...57 ...
Страница 113: ...113 APPENDIX A SmartView SCREEN AND MENU STRUCTURE ...
Страница 114: ...114 Detailed menu description ...
Страница 116: ...116 APPENDIX B MAINTENANCE SUMMARY AND LOGSHEETS Cont 19DV monthly Maintenance Log ...