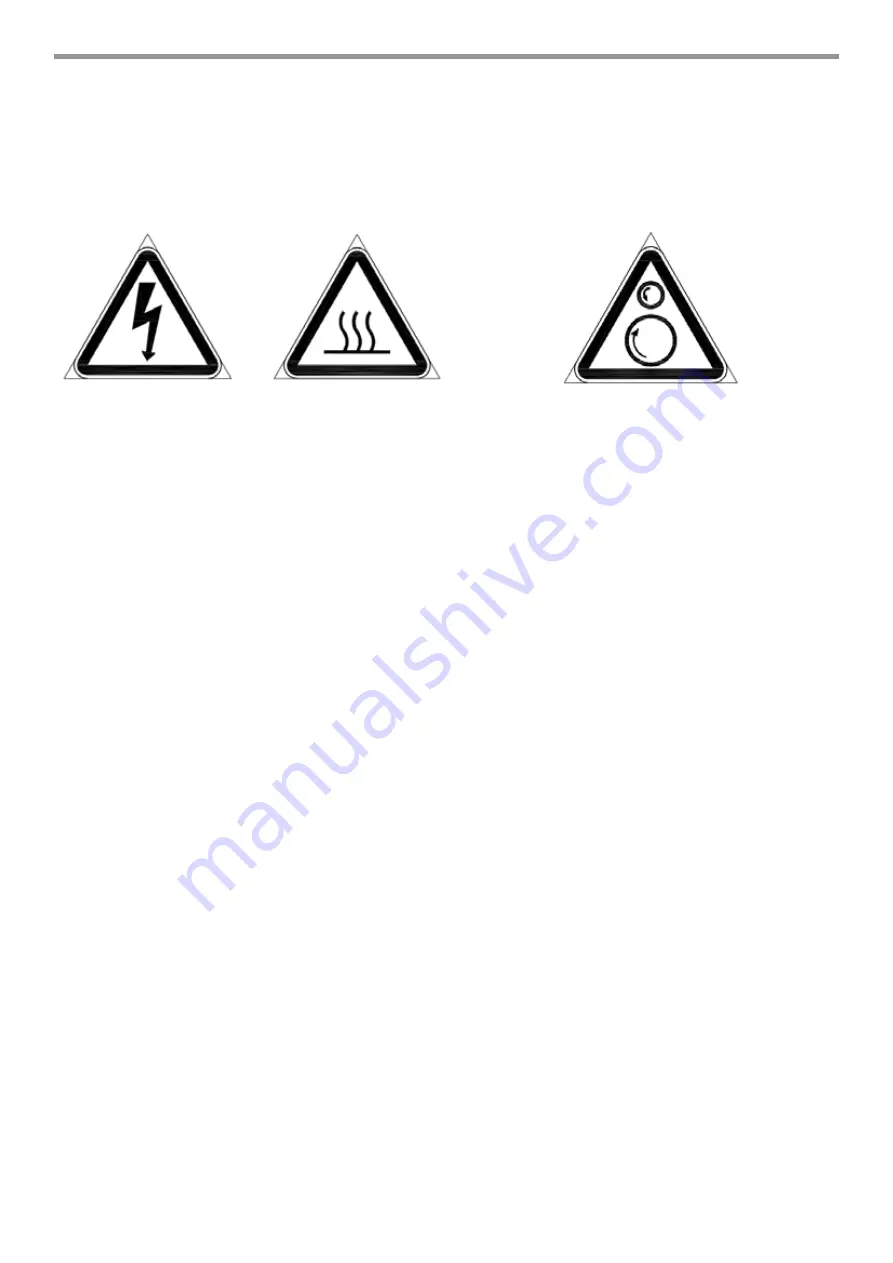
33
12.9.2. Electric Heaters
Check for contamination once a year and if neces-
sary clean with air jet. Check the connections in the
control box. Check operation of thermostat. The fol-
lowing warning pictograms are attached to the panel:
electric voltage and hot surface.
12.10. Coolers
Check for contamination once a year and if neces-
sary, clean with air jet against the direction of the air
flow or clean with a vacuum cleaner.
The eliminator assembly mounted after the cooler
can be removed. Perform leakage check. Check fins
of eliminator. Clean siphon and check its operation.
Check the condensation pan for contamination and
clean if necessary.
12.11. Heat Recovery Wheel
Check rotor for contamination once a year and clean
with air jet, if required. Check rotor speed and com-
pare it with design data.
Check the operation of the rotation monitor. Depend-
ing on roto-run material, rotary can absorb moisture.
When stationary rotary will absorb moist on one side
and thus become heavier.
For rotary speed adjustment, see manufacturer oper-
ating manual.
Rotor bearings are lubricated for complete life cycle
and maintenance free. Drive motor is accessible via
an inspection cover.
V-belt is automatically tensioned by a spring-loaded
rocking base on which motor is installed. New belts
expand excessively the beginning. Therefore, when
new belts are installed, check whether belt still has
enough tension after two days.
After this inspection, belt tension should be checked
weekly during the first month and then once a month.
If heat recovery wheel is controlled by a control panel,
see supplier documents for further information about
operation and maintenance details.
The following warning pictogram is attached to the
panel: rotating parts.
12.12. Plate Heat Exchanger
Check plate heat exchanger for contamination once
a year and if necessary, clean with air jet against the
direction of air flow. If dampers are used, strictly fol-
low the instructions in “Dampers” section.
Check the condensation pan for contamination and
clean if necessary.
12.13. Steam Humidifier
Clean the filter in steam supply line once a year.
If a filter is installed, also clean condensation drain
valve and inside of condensation tray.
Check control valve, condensation drain and distribu-
tion box twice a year.
With steam distribution pipes in negative pressure
systems (installed at air side) there may be excess
water present, as the condensation may not drain
from the steam distribution pipe.
For some brands a special siphon with a check valve
is supplied. Check the operation of this valve once a
year.
During periodical checks of the steam humidifier,
casing sections after the humidifier should facilitate
inspection and controlling of humidification level.
When viewed in the direction of the air flow rate, there
should not be any steam accumulated at the end of
the steam humidification section.
Electric humidifier capacity is strongly affected by
contamination of steam boiler and electrodes. This
is indicated by the LED. If required, replace steam
boiler or the electrodes.
Содержание AiroVision 39 HQ
Страница 2: ...2 Code No B 8 1 3i Book Publication Date 081018 Revision No 081018 ...
Страница 5: ...5 39 HQ Air Handling Units AiroVision Assembly Installation Commissioning Maintenance Manual ...
Страница 6: ...6 ...
Страница 23: ...23 ...
Страница 31: ...31 ...
Страница 40: ...40 APPENDIX 1 CELL INFO AND CONNECTION ORDER ...
Страница 41: ...41 APPENDIX 2 FRONT WITHDRAWAL FILTER DETAIL ...
Страница 42: ...42 APPENDIX 2 FRONT WITHDRAWAL POUCH FILTER INSTALLATION ...
Страница 43: ...43 APPENDIX 2 SIDE WITHDRAWAL COMBINED FILTER INSTALLATION ...
Страница 44: ...44 APPENDIX 2 SIDE WITHDRAWAL FILTER INSTALLATION F8 F9 ...
Страница 45: ...45 APPENDIX 2 SIDE WITHDRAWAL FILTER INSTALLATION F7 ...
Страница 46: ...46 APPENDIX 3 1 Side Withdrawal Filter ...
Страница 47: ...47 APPENDIX 3 2 Front Withdrawal Filter ...
Страница 48: ...48 APPENDIX 3 3 Pleated Filter ...
Страница 51: ...51 ...
Страница 52: ......