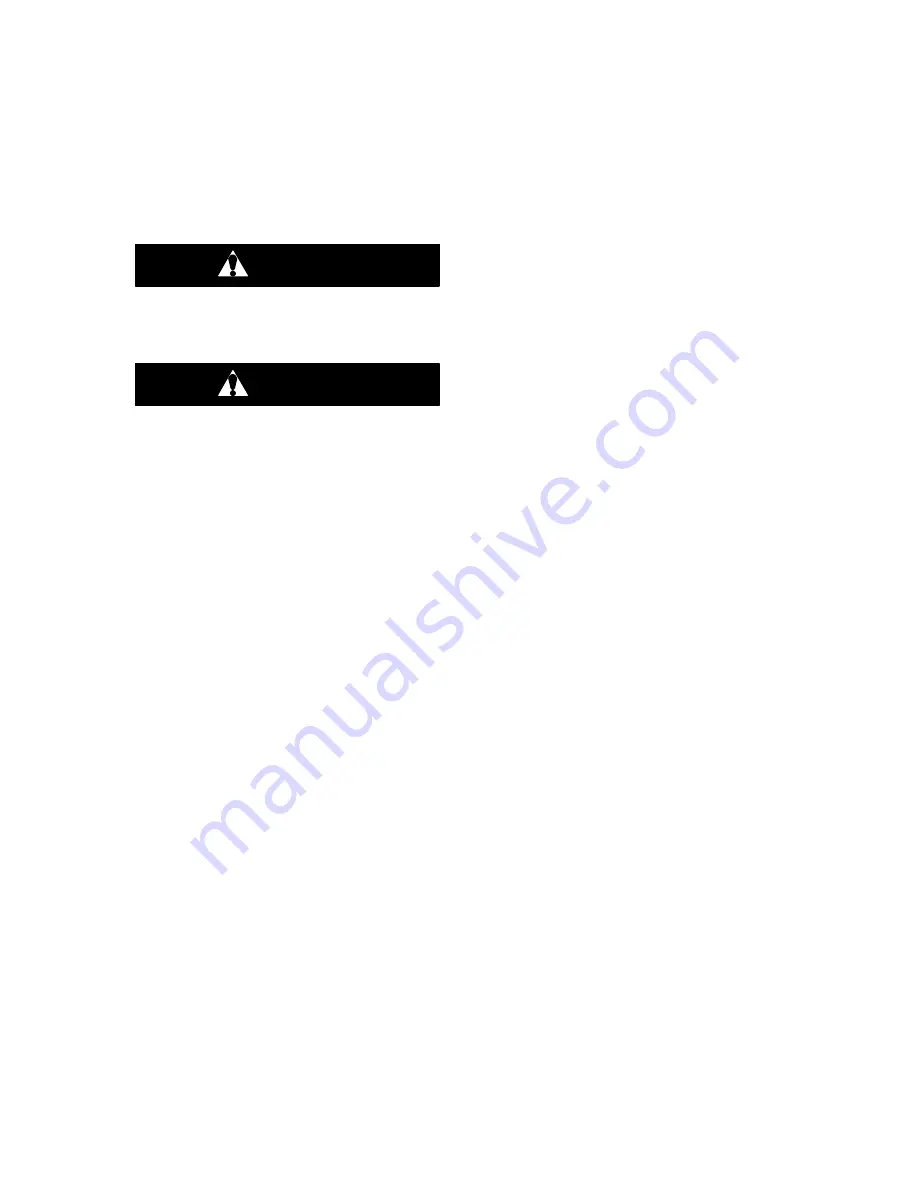
75
T-305
TP 9
This test point is the chassis (unit frame) ground
connection.
TP 10
This test point enables the user to check if the heat
termination thermostat (HTT) contact is open or closed.
6.21.3 Controller Programming Procedure
To load new software into the module, the programming
card is inserted into the programming/software port.
CAUTION
The unit must be OFF whenever a program-
ming card is inserted or removed from the
controller programming port.
CAUTION
All 69NT40-511-3XX units must use
software revision 5108 or higher to enable
stepper motor. Optional features may
require higher software revision levels to
enable functionality.
NOTE
The metal door (pins) on the programming card
must be facing to the left when inserting ML2/2i
cards. ML3 cards (PCMICA) may be used in
ML2/ML2i controllers using a PC Card Adapter
(Part Number 07--00461--00). The PC Adapter
is a printed circuit board that enables use of the
ML3 cards in ML2/ML2i controllers.
a. Procedure for loading Operational Software
1. Turn unit OFF, via start-stop switch (ST).
2. Insert the programming card for Operational Soft-
ware into the programming/software port. (See
Figure 46)
3. Turn unit ON, via start-stop switch (ST).
4. The Display module will alternate back and forth
between the messages “rEV XXXX” and “Press
EntR”. (If a defective card is being used the Display
will blink the message “bAd CArd”. Turn start-stop
switch OFF and remove the card.)
5. Press the ENTER key on the keypad.
6. The Display will show the message “Pro SoFt.” This
message will last for up to one minute.
7. The Display module will read “Pro donE” when the
software loading has loaded. (If a problem occurs
while loading the software: the Display will blink the
message “Pro FAIL” or “bad 12V”. Turn start-stop
switch OFF and remove the card.)
8. Turn unit OFF, via start-stop switch (ST).
9. Remove the programming card from the program-
ming/software port and return the unit to normal op-
eration by placing the start-stop switch in the ON
position.
b. Procedure for loading Configuration Software
1. Turn unit OFF using start-stop switch (ST).
2. Insert the programming card, for Configuration Soft-
ware, into the programming/software port. (See
Figure 46.)
3. Turn unit ON using start-stop switch (ST).
4. The Display module will show “489” on the left LCD
display and “###” on the right . The “###” will be the
dash number for a given unit model number, use the
UP or DOWN ARROW key to scroll through the list to
obtain the proper model dash number. For example,
to program a model number 69NT40-489-100, press
the UP or DOWN ARROW key until the display
shows “489” on the left display and “100” on the right.
(If a defective card is being used, the Display will
blink the message “bAd CArd”. Turn start-stop
switch OFF and remove the card.)
5. Press the ENTER key on the keypad.
6. When the software loading has successfully com-
pleted, the Display will show the message “EEPrM
donE.” (If a problem occurs while loading the soft-
ware, the Display will blink the message “Pro FAIL”
or “bad 12V.” Turn start-stop switch OFF and remove
the card.)
7. Turn unit OFF using start-stop switch (ST).
8. Remove the programming card from the program-
ming/software port and return the unit to normal op-
eration by placing the start-stop switch in the ON
position.
6.21.4 Removing and Installing the Controller
a. Removal:
1. Disconnect all front wire harness connectors (MA,
MB, MC, KA & KB) and move wiring out of way.
2 The lower controller mounting is slotted, loosen the
top mounting screw (see Figure 46) and lift up and
out.
3 Disconnect the two back connectors (EC) and re-
move module.
4 When removing the replacement controller from its
packaging , note how it is packaged. When returning
the old controller for service, place it in the packaging
in the same manner as the replacement. The pack-
aging has been designed to protect the controller
from both physical and electrostatic discharge dam-
age during storage and transit.
b.Installation:
Install the module by reversing the removal steps.
Torque values for mounting screws (item 2, see
Figure 46) are 0.23 mkg (20 inch-pounds). Torque value
for the connectors (MA, MB, MC, KA & KB) is 0.12 mkg
(10 inch-pounds).
6.21.5 Battery Replacement
If required, use tool 07-00418-00.
6.22 TEMPERATURE SENSOR SERVICE
Procedures for service of the Return Recorder, Return
Temperature, Supply Recorder, Supply Temperature,
Ambient, Defrost Temperature, Compressor Discharge
and Compressor Suction temperature sensors are
provided in the following sub paragraphs.
6.22.1 Sensor Checkout Procedure
To check a sensor reading, do the following:
a. Remove the sensor and place in a 0
_
C (32
_
F) ice-wa-
ter bath. The ice-water bath is prepared by filling an
Содержание 69NT40-489-100 Series
Страница 2: ......
Страница 4: ......
Страница 14: ...Safety 10 T 305...
Страница 28: ...4 T 305...
Страница 40: ...16 T 305...
Страница 50: ...26 T 305 Figure 12 Standard Configuration Report...
Страница 112: ...88 T 305...
Страница 163: ...139 T 305 CFS KA6 CFA1 QC1 FDH HST RRS SINGLE SENSOR ONLY Figure 88 Wiring Diagram Sheet 2 of 2...
Страница 164: ...140 T 305...
Страница 167: ...143 T 305 Based on drawings 62 10526 Rev and 62 10736 Rev Figure 90 Electrical Schematic CA...
Страница 168: ...144 T 305 ALTERNATE CONFIGURATION Figure 91 Electrical Wiring Diagram Controlled Atmosphere Sheet 1 of 2...
Страница 169: ...145 T 305 F Figure 88 E Figure 88 Figure 91 Electrical Wiring Diagram Controlled Atmosphere Sheet 2 of 2...
Страница 172: ...148 T 305 Figure 93 Electrical Wiring Diagram Sheet 1 of 2 Units not modified to include the N2 Purity Solenoid Valve...
Страница 174: ...150 T 305...