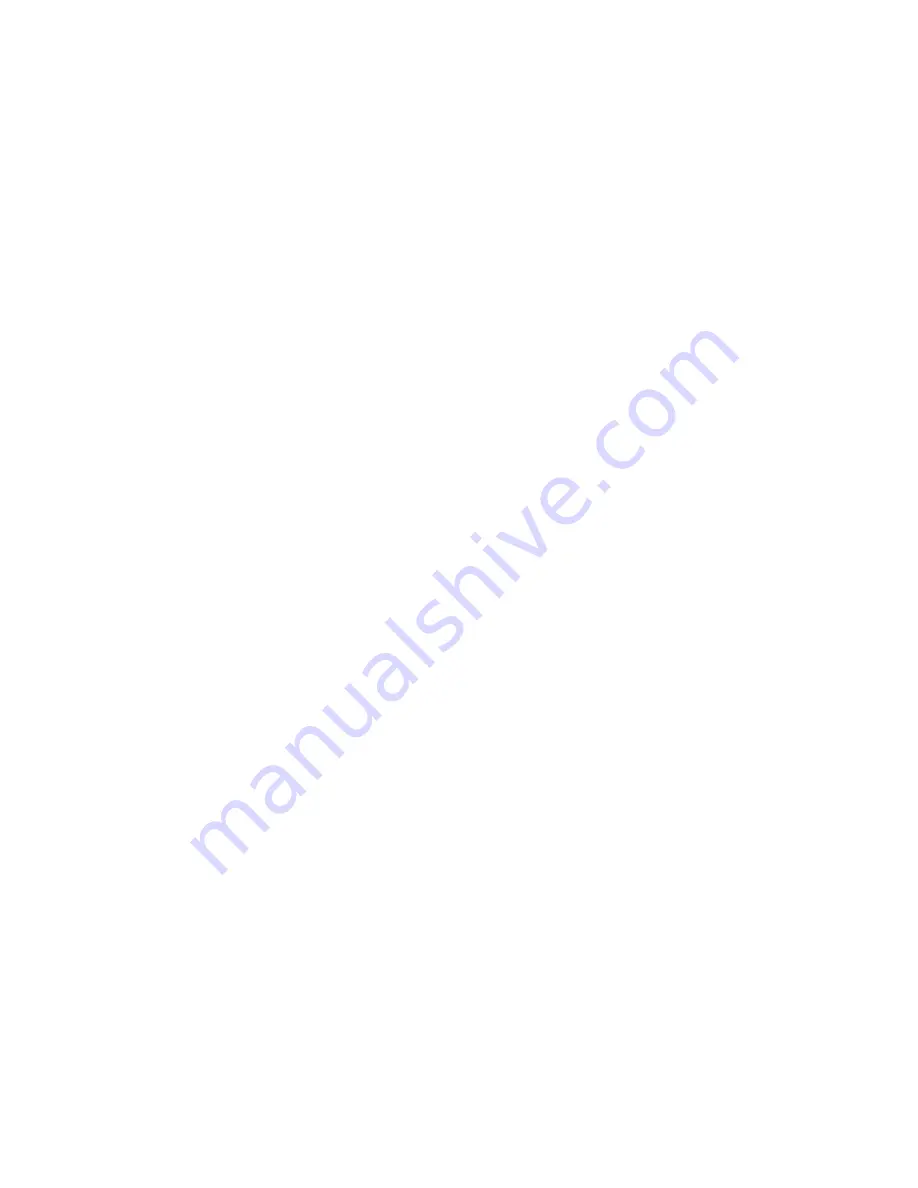
T-372
7–14
10. To make sure that the motor is aligned properly, slide the condenser fan onto the motor shaft reversed but
do not secure.
11. Rotate the fan to make sure the fan blades do not contact the shroud:
• If the fan motor is misaligned vertically, add or remove shims to align.
• If the fan motor is not properly centered, loosen the mounting bolts, and adjust the motor position on the
bracket, and then secure the motor.
12. Remove the condenser fan, and connect the fan motor wiring to the fan motor.
13. Place the condenser fan on the shaft facing the correct direction. Adjust the fan to the correct position,
37mm (1.5”) from the fan shroud, see
14. Use Loctite “H” on the fan set screws, and tighten.
15. Refit the left and right infill panels.
16. Refit the condenser fan grille, ensuring the grille is properly centered around condenser fan.
7.13 Water-Cooled Condenser Cleaning
The water-cooled condenser is of the shell and coil type with water circulating through the cupro-nickel coil. The
refrigerant vapor is admitted to the shell side and is condensed on the outer surface of the coil.
Rust, scale and slime on the water-cooling surfaces inside of the coil interfere with the transfer of heat, reduce sys
-
tem capacity, cause higher head pressures and increase the load on the system.
By checking the leaving water temperature and the actual condensing temperature, it can be determined if the con
-
denser coil is becoming dirty. A larger than normal difference between leaving condensing water temperature and
actual condensing temperature, coupled with a small difference in temperature of entering and leaving condensing
water, is an indication of a dirty condensing coil.
If the water-cooled condenser is dirty, it may be cleaned and de-scaled.
7.13.1
Cleaning Supplies Needed
• Oakite Aluminum Cleaner® 164, available as a powder in 20 kg (44 lb) pails and 205 kg (450 lb) drums.
• Oakite Composition No. 32, available as a liquid in cases, each containing 3.785 liters (4 U.S. gallon) bottles
and also in carboys of 52.6 kg (116 lbs) net.
• Fresh clean water.
• Acid proof pump and containers or bottles with rubber hose.
NOTE
When Oakite Compound No. 32 is used for the first time, the local Oakite technical service representative
should be called in for suggestions in planning the procedure. The representative will advise the reader on
how to do the work with a minimum dismantling of equipment: how to estimate the time and amount of
compound required; how to prepare the solution; how to control and conclude the de-scaling operation by
rinsing and neutralizing equipment before putting it back into service. The representative’s knowledge of
metals, types of scale, water conditions and de-scaling techniques will be highly useful.
7.13.2
Cleaning Procedure Summary
1. Turn the unit off and disconnect main power.
2. Disconnect the water pressure switch tubing by loosening the two flare nuts. Install a 1/4 inch flare cap on
the water-cooled condenser inlet tube (replaces tubing flare nut). De-scale tubing if necessary.
3. Drain water from the condenser tubing circuit.
4. Clean the water tubes with Oakite Aluminum Cleaner® 164 to remove mud and slime.
5. Flush.
6. De-scale the water tubes with Oakite No. 32 to remove scale.
7. Flush.
8. Neutralize.
Содержание PrimeLINE 69NT40-571-001
Страница 2: ......
Страница 4: ......
Страница 14: ......
Страница 36: ......
Страница 110: ......
Страница 116: ......
Страница 171: ...8 1 T 372 SECTION 8 ELECTRICAL WIRING SCHEMATIC AND DIAGRAMS Figure 8 1 Legend Standard Unit Configuration ...
Страница 172: ...T 372 8 2 ELECTRICAL WIRING SCHEMATIC AND DIAGRAMS Figure 8 2 Schematic Diagram Based on Drawing 62 11957 ...
Страница 176: ......
Страница 178: ......
Страница 180: ......
Страница 184: ......
Страница 185: ......