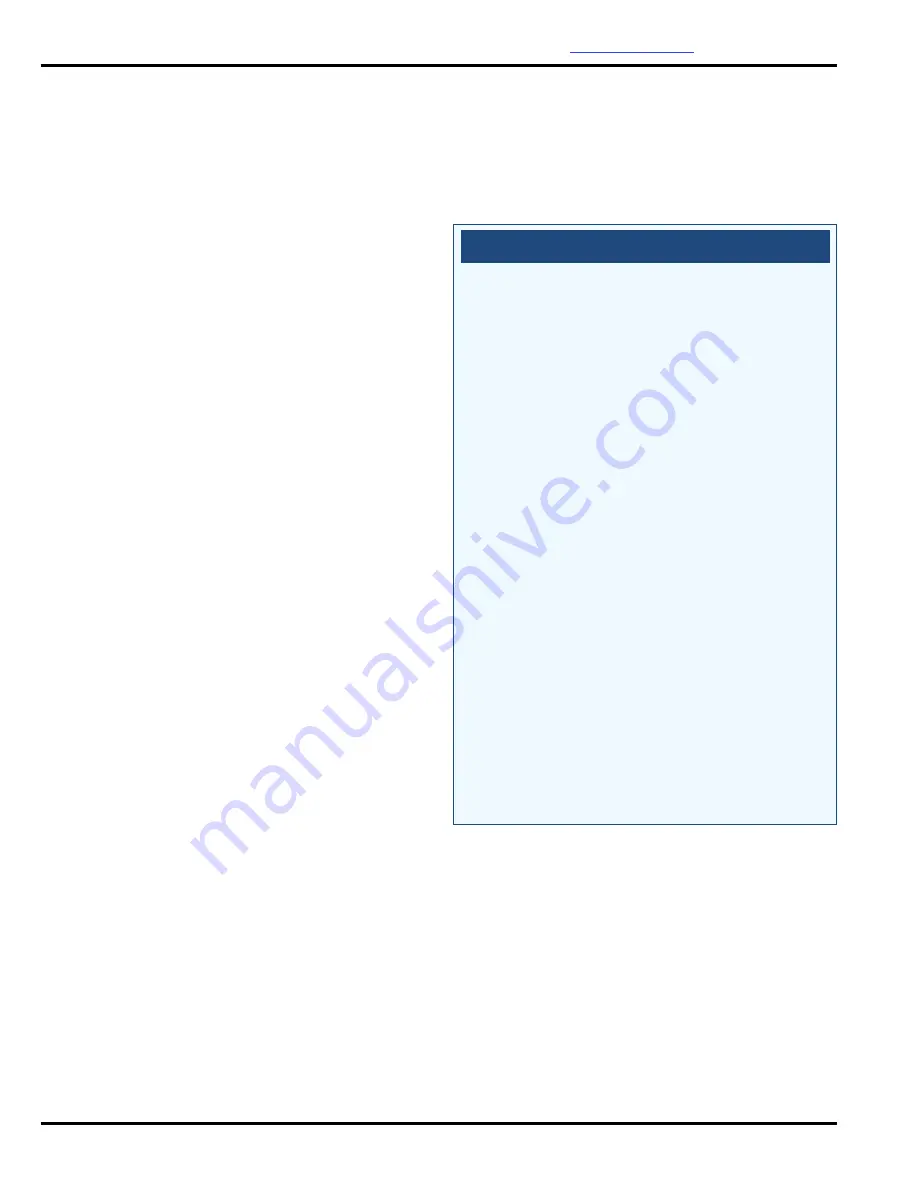
EQUIPMENT AND MATERIALS REQUIRED
EN
SI-21-06-R1 (11/2021)
8 / 32
www.carlisleft.com
EQUIPMENT AND MATERIALS REQUIRED
1. 2/0 or finer abrasive paper or cloth 1-inch-wide x 8-8
1/2-inch-long strips (25mm wide x 200mm long) (in-
cluded with kit A14896-00 and A12951-02) Circu-
lar Donut 2/0 or finer abrasive disks .950 I.D. x 1.54
O.D. (24.1mm I.D. x 39.1mm O.D.) (included with kit
A14896-00 and A12951-02)
2. Lint Free Tissue (included with kit A14896-00 and
A12951-02)
3. Aerosol electrical contact cleaner with Nozzle Attach-
ment
4. .004-inch (0.102mm) Diameter Piano Wire (included
with kit A14896-00 and A12951-02)
5. T-10 Star bit Wrench
6. Set of 90 degree “V” Blocks (Preferred Size 70mm x
90mm x 125mm) or A13268-00 Alignment Ring
7. Magnifier with Light – visual inspection
8. Master Bell Cup (12900-XX cup only) or equal
10. Safety Glasses
11. Latex Gloves
12. Isopropyl Alcohol
13. 3mm Hex Wrench
14. Light Duty Thread Retaining Compound (7969-05)
15. Torque wrench driver (30 lbs.-in. (3.4 Nm) capacity
16. Isopropyl Alcohol 99% Pure
NOTE
Flooded turbine motors - prove to be difficult to
repair if not addressed immediately after being flood-
ed. It’s difficult to impossible to flush the contaminat-
ed “hardened” fluid from the bearing air ports. If the
unit cannot be cleaned up quickly, then the bearings
and or housing must be replaced. Do not soak bear-
ings in Ethylene-Glycol as it will destroy the bearing
substrate and pressed in jets. The radial bearing may
be soaked in a solvent compatible with the paint in-
trusion. A use of an Ultrasonic cleaner may aid in
the loosening of material. Do not let turbine compo-
nents sit in ultrasonics longer than 20 minutes. Some
solutions will etch the turbine motor components.
During repair of multiple turbine motors
DO NOT MIX COMPONENT PARTS all rotor
shafts are matched with their spacer ring to pro-
vide correct spacing for operation of the spindle.
The spacers and the shafts are a matched
set. The number on the shaft must correspond to
the number on the spacer plate. See Figure 1-25.
During tear down remove all O-rings and save
in a safe place until new O-ring kit is installed.
Final rinsing of component parts should be made
by Isopropyl Alcohol.