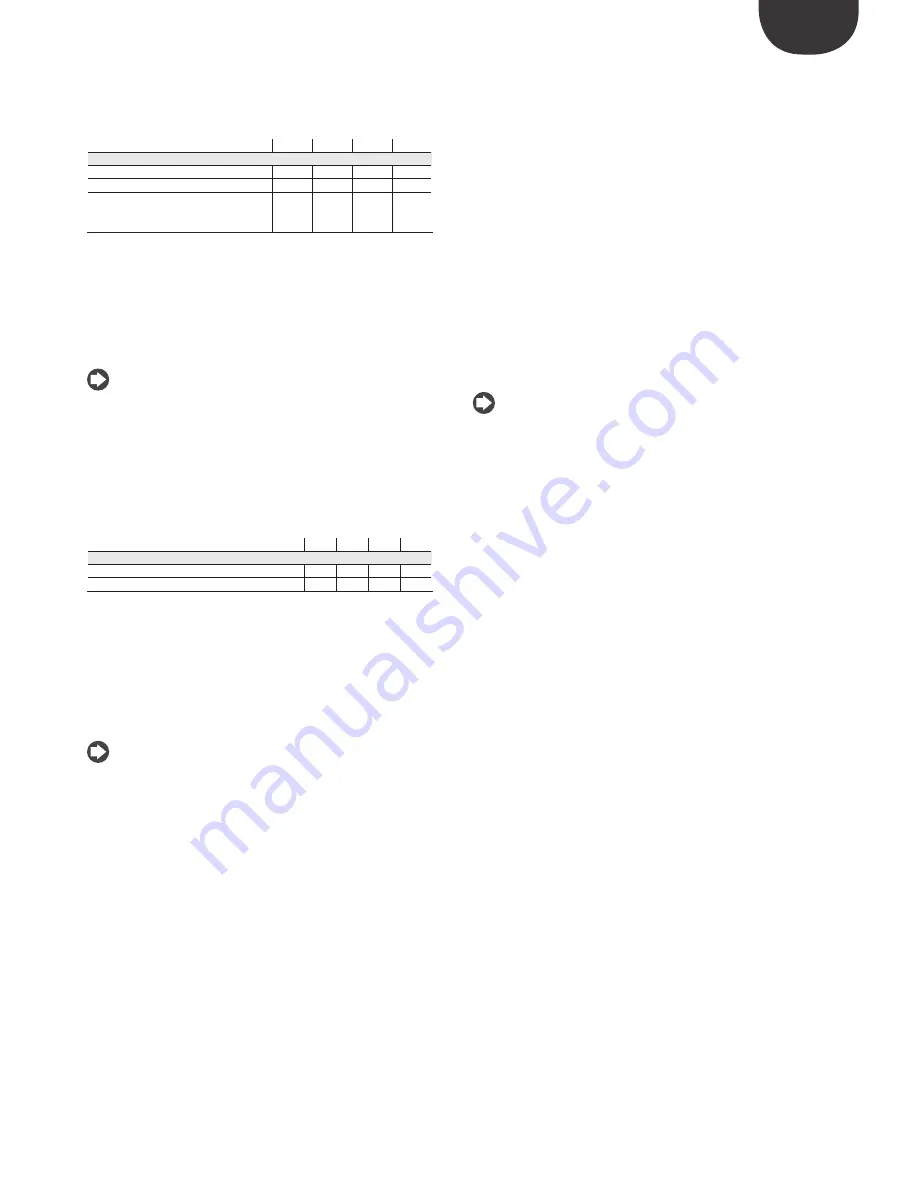
ENG
“EVD Evolution TWIN” +0300006EN - rel. 2.6 - 31.01.2019
33
Manual positioning
Manual positioning can be activated at any time during the standby or control
phase. Manual positioning, once enabled, is used to freely set the position of
the valve using the corresponding parameter.
Parameter/Description
Def.
Min.
Max.
UOM
CONTROL
Enable manual valve positioning
0
0
1
-
Manual valve position
0
0
9999
step
Stop manual positioning on network
error
0 = Normal operation; 1 = Stop
0
0
1
-
Tab. 6.l
Control is placed on hold, all the system and control alarms are enabled,
however neither control nor the protectors can be activated. Manual
positioning thus has priority over any status/protection of the driver.
When the driver is connected to the network (for example to a pCO controller),
in presence of an communication-error (LAN error), manual positioning can
be inhibited temporarily by the parameter and the driver recognizes the start/
stop regulation, depending on the configuration of the digital inputs.
Note:
•
the manual positioning status is NOT saved when restarting after a power
failure;
•
in for any reason the valve needs to be kept stationary after a power failure,
proceed as follows:
-
remove the valve stator;
-
in Manufacturer programming mode, under the configuration
parameters, set the PID proportional gain =0. The valve will remain
stopped at the initial opening position, set by corresponding parameter.
R
ecover physical valve position
Parameter/Description
Def.
Min.
Max. UOM
VALVE
Synchronise valve position in opening
1
0
1
-
Synchronise valve position in closing
1
0
1
-
Tab. 6.m
This procedure is necessary as the stepper motor intrinsically tends to lose
steps during movement. Given that the control phase may last continuously
for several hours, it is probable that from a certain time on the estimated
position sent by the valve controller does not correspond exactly to the
physical position of the movable element. This means that when the driver
reaches the estimated fully closed or fully open position, the valve may
physically not be in that position. The “Synchronisation” procedure allows the
driver to perform a certain number of steps in the suitable direction to realign
the valve when fully opened or closed.
Note:
•
realignment is in intrinsic part of the forced closing procedure and is
activated whenever the driver is stopped/started and in the standby phase;
•
the possibility to enable or disable the synchronisation procedure depends
on the mechanics of the valve. When the setting the “valve” parameter, the
two synchronisation parameters are automatically defined. The default
values should not be changed.
Unblock valve
This procedure is only valid when the driver is performing superheat control.
Unblock valve is an automatic safety procedure that attempts to unblock a
valve that is supposedly blocked based on the control variables (superheat,
valve position). The unblock procedure may or may not succeed depending
on the extent of the mechanical problem with the valve. If for 10 minutes the
conditions are such as to assume the valve is blocked, the procedure is run a
maximum of 5 times. The symptoms of a blocked valve doe not necessarily
mean a mechanical blockage. They may also represent other situations:
•
mechanical blockage of the solenoid valve upstream of the electronic valve
(if installed);
•
electrical damage to the solenoid valve upstream of the electronic valve;
•
blockage of the filter upstream of the electronic valve (if installed);
•
electrical problems with the electronic valve motor;
•
electrical problems in the driver-valve connection cables;
•
incorrect driver-valve electrical connection;
•
electronic problems with the valve control driver;
•
secondary fluid evaporator fan/pump malfunction;
•
insufficient refrigerant in the refrigerant circuit;
•
refrigerant leaks;
•
lack of subcooling in the condenser;
•
electrical/mechanical problems with the compressor;
•
processing residues or moisture in the refrigerant circuit.
Note:
the valve unblock procedure is nonetheless performed in each
of these cases, given that it does not cause mechanical or control problems.
Therefore, also check these possible causes before replacing the valve.
Содержание EVD Evolution Twin
Страница 2: ......
Страница 4: ......
Страница 6: ......
Страница 66: ...ENG EVD Evolution TWIN 0300006EN rel 2 6 31 01 2019 66 Note...
Страница 67: ......