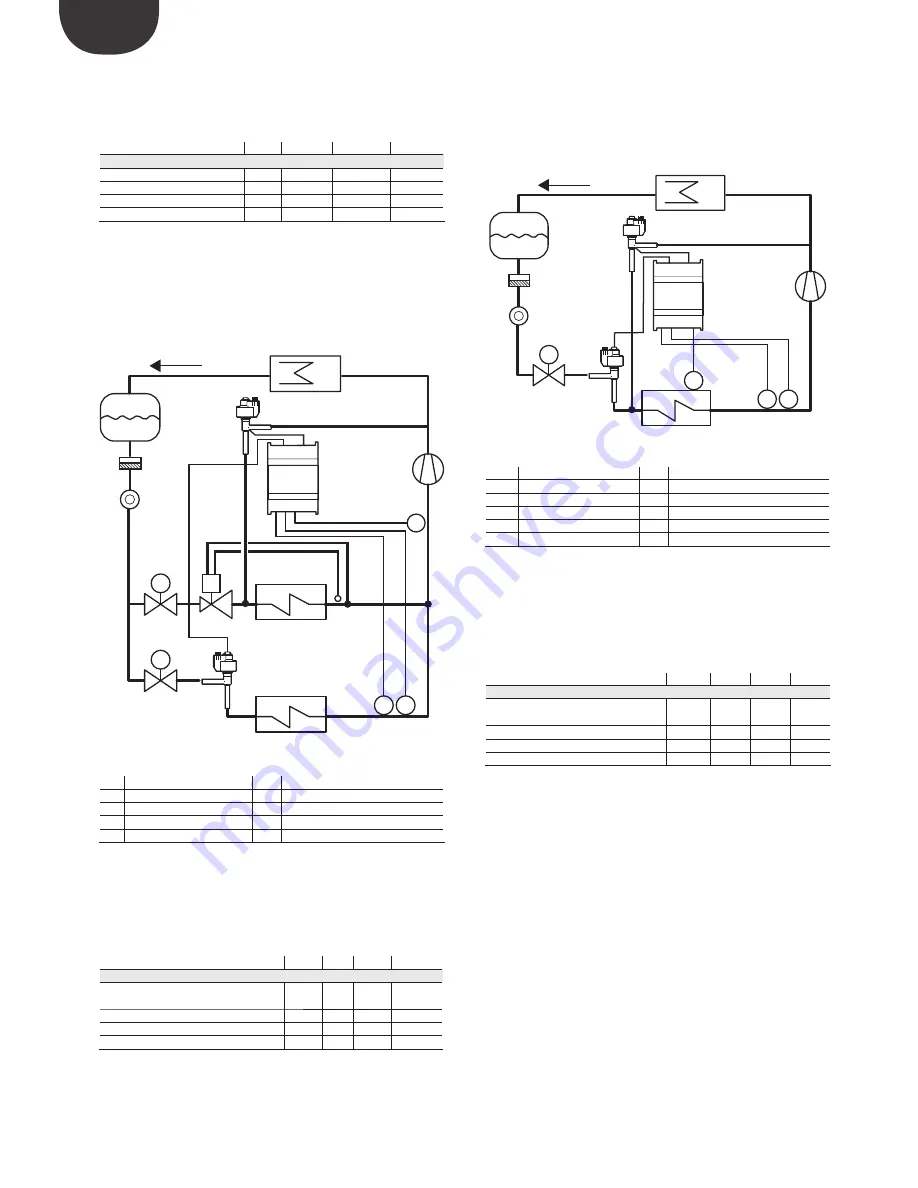
ENG
“EVD Evolution TWIN” +0300006EN - rel. 2.6 - 31.01.2019
24
This involves PID control without any protectors (LowSH, LOP, MOP, see the
chapter on Protectors), without any valve unblock procedure. Control is
performed on the pressure probe value read by input S1 for driver A and S3 for
driver B, compared to the set point: “EPR pressure set point”. Control is direct,
as the pressure increases, the valve opens and vice-versa.
Parameter/Description
Def.
Min.
Max.
UOM
CONTROL
EPR pressure set point
3.5
-20 (-290) 200 (2900)
barg (psig)
PID: proportional gain
15
0
800
-
PID: integral time
150
0
1000
s
PID: derivative time
5
0
800
s
Tab. 5.h
Hot gas bypass by pressure
This control function can be used to control cooling capacity, which in the
following example is performed by driver B. If there is no request from circuit Y,
the compressor suction pressure decreases and the bypass valve opens to let
a greater quantity of hot gas flow and decrease the capacity of circuit X. Driver
A is used for superheat control on circuit Y.
E
V1
M
E
V1
V2
M
T
S
F
L
CP
EVB
C
S1
EVD evolution
twin
S3
PA TA
EEVA
X
Y
S2
PB
Fig. 5.h
Key:
CP
Compressor
V1
Solenoid valve
C
Condenser
V2
Thermostatic expansion valve
L
Liquid receiver
EEVA Electronic expansion valve A
F
Dewatering filter
EVB
Electronic valve B
S
Liquid indicator
E
Evaporator
For the wiring, see paragraph “General connection diagram”.
This involves PID control without any protectors (LowSH, LOP, MOP, see the
chapter on Protectors), without any valve unblock procedure. Control is
performed on the hot gas bypass pressure probe value read by input S3,
compared to the set point: “Hot gas bypass pressure set point”. Control is
reverse, as the pressure increases, the valve closes and vice-versa.
Parameter/Description
Def.
Min. Max.
UOM
CONTROL
Hot gas bypass pressure set point
3
-20
(290)
200
(2900)
barg
(psig)
PID: proportional gain
15
0
800
-
PID: integral time
150
0
1000
s
PID: derivative time
5
0
800
s
Tab. 5.i
Hot gas bypass by temperature
This control function can be used to control cooling capacity, which in the
following example is performed by driver B. On a refrigerated cabinet, if the
ambient temperature probe S4 measures an increase in the temperature, the
cooling capacity must also increase, and so the EVB valve must close. In the
example driver A is used for superheat control.
E
V
M
S
F
L
CP
EVB
C
TB
S1
EVD evolution
twin
S4
PA TA
EEVA
S2
Fig. 5.i
Key:
CP
Compressor
V
Solenoid valve
C
Condenser
EEVA Electronic expansion valve A
L
Liquid receiver
EVB
Electronic valve B
F
Dewatering filter
E
Evaporator
S
Liquid indicator
PA
Pressure probe driver A
TA, TB Temperature probe
For the wiring, see paragraph “General connection diagram”.
This involves PID control without any protectors (LowSH, LOP, MOP, see the
chapter on Protectors), without any valve unblock procedure. Control is
performed on the hot gas bypass temperature probe value read by input S4,
compared to the set point: “Hot gas bypass temperature set point”. Control is
reverse, as the temperature increases, the valve closes.
Parameter/Description
Def.
Min.
Max.
UOM
CONTROL
Hot gas bypass temperature set point
10
-60
(-76)
200
(392)
°C (°F)
PID: proportional gain
15
0
800
-
PID: integral time
150
0
1000
s
PID: derivative time
5
0
800
s
Tab. 5.j
Another application that exploits this control function uses the connection
of two EXV valves together to simulate the effect of a three-way valve, called
“reheating”. To control humidity, valve EVB_2 is opened to let the refrigerant
flow into exchanger S. At the same time, the air that flows through evaporator
E is cooled and the excess humidity removed, yet the temperature is below
the set room temperature. It then flows through exchanger S, which heats it
back to the set point (reheating). In addition, if dehumidification needs to be
increased, with less cooling, valve EVA_2 must open to bypass at least some
of the refrigerant to condenser C. The refrigerant that reaches the evaporator
thus has less cooling capacity. Valves EVA_1 and EVA_2 are also connected
together in complementary mode, controlled by the 4 to 20 mA signal on
input S1, from an external regulator.
Содержание EVD Evolution Twin
Страница 2: ......
Страница 4: ......
Страница 6: ......
Страница 66: ...ENG EVD Evolution TWIN 0300006EN rel 2 6 31 01 2019 66 Note...
Страница 67: ......