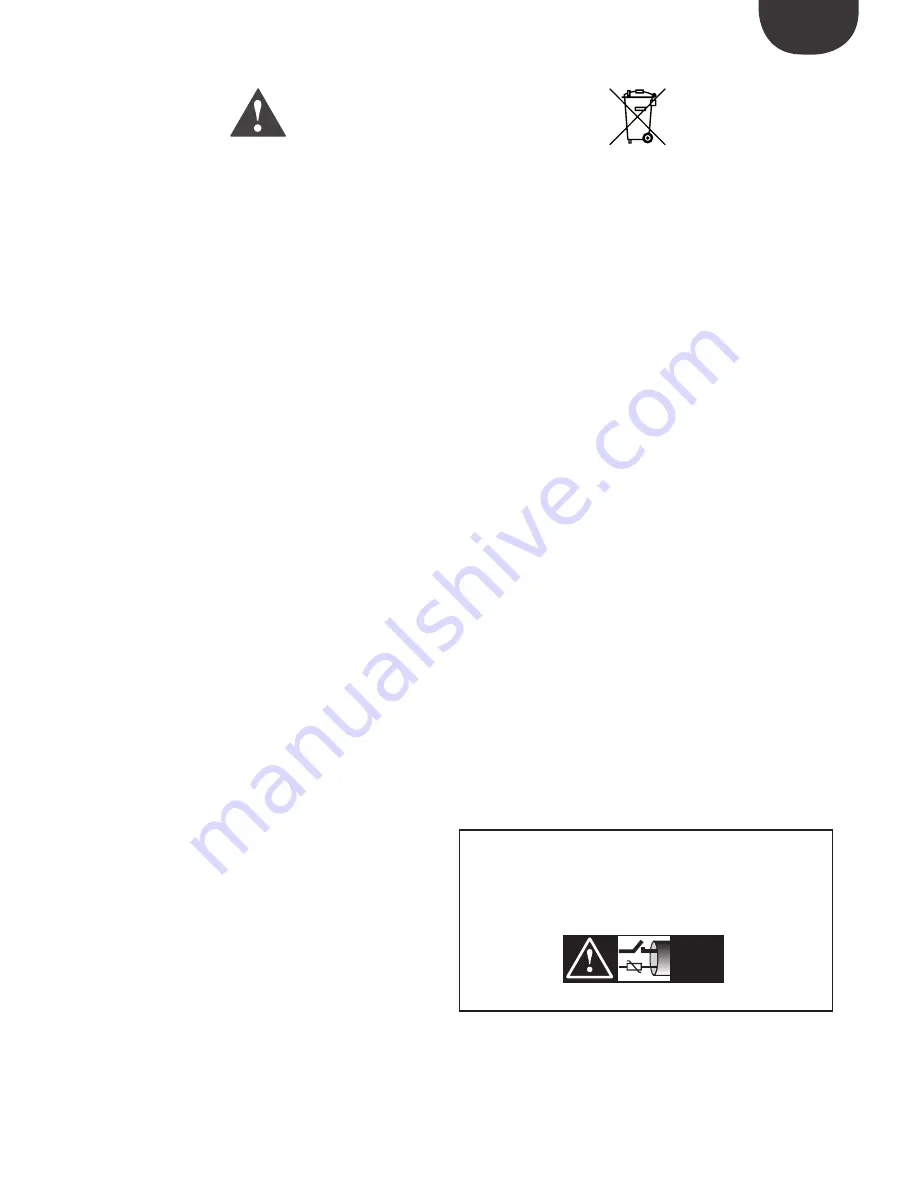
NO POWER
& SIGNAL
CABLES
TOGETHER
READ CAREFULLY IN THE TEXT!
ENG
“EVD Evolution TWIN” +0300006EN - rel. 2.6 - 31.01.2019
3
WARNINGS
CAREL INDUSTRIES bases the development of its products on decades
of experience in HVAC, on the continuous investments in technological
innovations to products, procedures and strict quality processes with in-circuit
and functional testing on 100% of its products, and on the most innovative
production technology available on the market. CAREL INDUSTRIES and its
subsidiaries/affiliates nonetheless cannot guarantee that all the aspects
of the product and the software included with the product respond to the
requirements of the final application, despite the product being developed
according to start-of-the-art techniques. The customer (manufacturer,
developer or installer of the final equipment) accepts all liability and risk
relating to the configuration of the product in order to reach the expected
results in relation to the specific final installation and/or equipment.
CAREL INDUSTRIES may, based on specific agreements, acts as a consultant
for the successful commissioning of the final unit/application, however in no
case does it accept liability for the correct operation of the final equipment/
system.
The CAREL INDUSTRIES product is a state-of-the-art product, whose operation
is specified in the technical documentation supplied with the product or can
be downloaded, even prior to purchase, from the website www.carel.com.
Each CAREL INDUSTRIES product, in relation to its advanced level of
technology, requires setup/configuration/programming/commissioning
to be able to operate in the best possible way for the specific application.
The failure to complete such operations, which are required/indicated in the
user manual, may cause the final product to malfunction; CAREL INDUSTRIES
accepts no liability in such cases. Only qualified personnel may install or carry
out technical service on the product. The customer must only use the product
in the manner described in the documentation relating to the product.
In addition to observing any further warnings described in this manual, the
following warnings must be heeded for all CAREL INDUSTRIES products:
•
prevent the electronic circuits from getting wet. Rain, humidity and all
types of liquids or condensate contain corrosive minerals that may damage
the electronic circuits. In any case, the product should be used or stored
in environments that comply with the temperature and humidity limits
specified in the manual;
•
do not install the device in particularly hot environments. Too high
temperatures may reduce the life of electronic devices, damage them and
deform or melt the plastic parts. In any case, the product should be used
or stored in environments that comply with the temperature and humidity
limits specified in the manual;
•
do not attempt to open the device in any way other than described in the
manual;
•
do not drop, hit or shake the device, as the internal circuits and mechanisms
may be irreparably damaged;
•
do not use corrosive chemicals, solvents or aggressive detergents to clean
the device;
•
do not use the product for applications other than those specified in the
technical manual.
All of the above suggestions likewise apply to the controllers, serial boards,
programming keys or any other accessory in the CAREL INDUSTRIES product
portfolio.
CAREL INDUSTRIES adopts a policy of continual development. Consequently,
CAREL INDUSTRIES reserves the right to make changes and improvements to
any product described in this document without prior warning.
The technical specifications shown in the manual may be changed without
prior warning.
The liability of CAREL INDUSTRIES in relation to its products is specified in
the CAREL INDUSTRIES general contract conditions, available on the website
www.carel.com and/or by specific agreements with customers; specifically,
to the extent where allowed by applicable legislation, in no case will CAREL
INDUSTRIES, its employees or subsidiaries/affiliates be liable for any lost
earnings or sales, losses of data and information, costs of replacement goods
or services, damage to things or people, downtime or any direct, indirect,
incidental, actual, punitive, exemplary, special or consequential damage of any
kind whatsoever, whether contractual, extra-contractual or due to negligence,
or any other liabilities deriving from the installation, use or impossibility to use
the product, even if CAREL INDUSTRIES or its subsidiaries are warned of the
possibility of such damage.
DISPOSAL
INFORMATION FOR USERS ON THE CORRECT HANDLING OF WASTE
ELECTRICAL AND ELECTRONIC EQUIPMENT (WEEE)
In reference to European Union directive 2002/96/EC issued on 27 January
2003 and the related national legislation, please note that:
1. WEEE cannot be disposed of as municipal waste and such waste must be
collected and disposed of separately;
2. the public or private waste collection systems defined by local legislation
must be used. In addition, the equipment can be returned to the
distributor at the end of its working life when buying new equipment;
3. the equipment may contain hazardous substances: the improper use or
incorrect disposal of such may have negative effects on human health and
on the environment;
4. the symbol (crossed-out wheeled bin) shown on the product or on the
packaging and on the instruction sheet indicates that the equipment has
been introduced onto the market after 13 August 2005 and that it must
be disposed of separately;
5. in the event of illegal disposal of electrical and electronic waste, the
penalties are specified by local waste disposal legislation.
W
arranty on the materials:
2 years (from the date of production, excluding
consumables).
A
pproval:
the quality and safety of CAREL INDUSTRIES products are
guaranteed by the ISO 9001 certified design and production system.
IMPORTANT: Separate as much as possible the probe and digital input cables
from the cables to inductive loads and power cables to avoid possible
electromagnetic disturbance.
Never run power cables (including the electrical panel cables) and signal
cables in the same conduits
Содержание EVD Evolution Twin
Страница 2: ......
Страница 4: ......
Страница 6: ......
Страница 66: ...ENG EVD Evolution TWIN 0300006EN rel 2 6 31 01 2019 66 Note...
Страница 67: ......