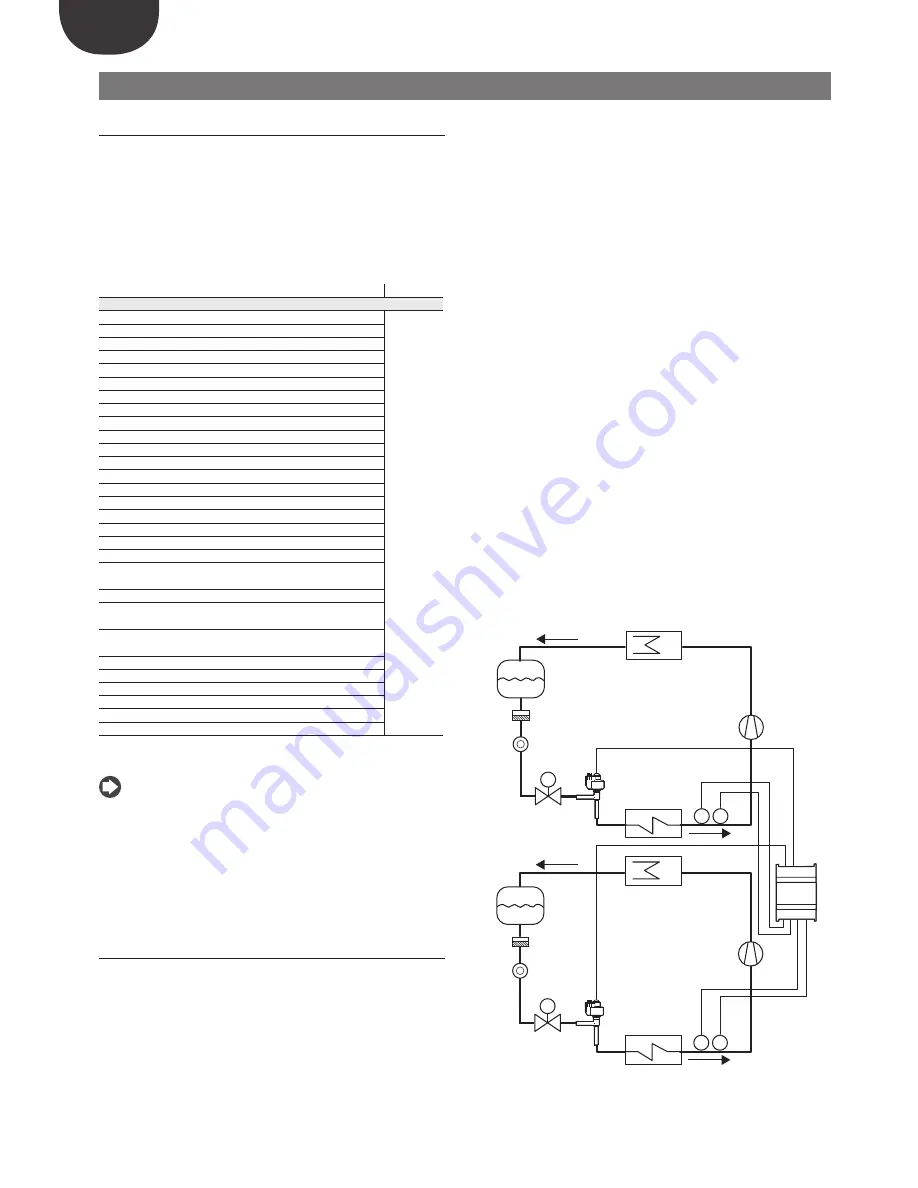
ENG
“EVD Evolution TWIN” +0300006EN - rel. 2.6 - 31.01.2019
20
5. CONTROL
S
uperheat control
The parameter that the control of the electronic valve is based on is the
superheat temperature, which effectively tells whether or not there is liquid
at the end of the evaporator. EVD Evolution twin can independently manage
superheat control on two refrigerant circuits. The superheat temperature
is calculated as the difference between: superheated gas temperature
(measured by a temperature probe located at the end of the evaporator) and
the saturated evaporation temperature (calculated based on the reading of a
pressure transducer located at the end of the evaporator and using the Tsat(P)
conversion curve for each refrigerant).
Superheat = Superheated gas temperature(*) – Satur. evaporation temperature
(*) suction
If the superheat temperature is high it means that the evaporation process is
completed well before the end of the evaporator, and therefore flow-rate of
refrigerant through the valve is insufficient. This causes a reduction in cooling
efficiency due to the failure to exploit part of the evaporator. The valve must
therefore be opened further. Vice-versa, if the superheat temperature is low
it means that the evaporation process has not concluded at the end of the
evaporator and a certain quantity of liquid will still be present at the inlet to
the compressor. The valve must therefore be closed further. The operating
range of the superheat temperature is limited at the lower end: if the flow-
rate through the valve is excessive the superheat measured will be near 0 K.
This indicates the presence of liquid, even if the percentage of this relative to
the gas cannot be quantified. There is therefore un undetermined risk to the
compressor that must be avoided. Moreover, a high superheat temperature
as mentioned corresponds to an insufficient flow-rate of refrigerant. The
superheat temperature must therefore always be greater than 0 K and have
a minimum stable value allowed by the valve-unit system. A low superheat
temperature in fact corresponds to a situation of probable instability due to
the turbulent evaporation process approaching the measurement point of
the probes. The expansion valve must therefore be controlled with extreme
precision and a reaction capacity around the superheat set point, which will
almost always vary from 3 to 14 K. Set point values outside of this range are
quite infrequent and relate to special applications.
Example of superheat control on two independent circuits A and B
.
S2
S1
EVD evolution
twin
PA
E1
V1
S1
F1
L1
M
TA
CP1
C1
EEVA
PB
E2
V2
S2
F2
L2
M
TB
CP2
C2
EEVB
S3
S4
A
B
Fig. 5.a
5.1 Main
control
EVD evolution twin features two types of control, which can be set
independently for driver A and B. Main control defines the operating mode
of the driver. The first 10 settings refer to superheat control, the others are so-
called “special” settings and are pressure or temperature settings or depend
on a control signal from an external controller. The last special functions (18,
19, 20) also relate to superheat control, but they can be selectable if EVD
Evolution TWIN is working as single driver (see Appendix 2). Programmable
control exploits CAREL’s technology and know-how in terms of control
logic. Finally, it is possible to control liquid level in applications with flooded
evaporator/condenser.
Parameter/Description
Def.
CONFIGURATION
Main control
multiplexed
showcase/
cold room
Superheat control
1= multiplexed showcase/cold room
2= showcase/cold room with compressor on board
3= “perturbed” showcase/cold room
4= showcase/cold room with sub-critical CO
2
5= R404A condenser for sub-critical CO
2
6= air-conditioner/chiller with plate heat exchanger
7= air-conditioner/chiller with tube bundle heat exchanger
8= air-conditioner/chiller with finned coil heat exchanger
9= air-conditioner/chiller with variable cooling capacity
10= “perturbed” air-conditioner/chiller
Special control
11= EPR back pressure
12= hot gas bypass by pressure
13= hot gas bypass by temperature
14= transcritical CO
2
gas cooler
15= analogue positioner (4 to 20 mA)
16= analogue positioner (0 to 10 V)
17= air-conditioner/chiller or showcase/cold room with
adaptive control
18= air-conditioner/chiller with Digital Scroll compressor (*)
19=AC/chiller with BLDC scroll compressor (CANNOT BE
SELECTED)
20=superheat regulation with 2 temperature probes (CANNOT
BE SELECTED)
21=I/O expander for pCO (**)
22= Programmable SH regulation
23= Programmable special regulation
24= Programmable positioner
25= Evaporator liquid level regulation with CAREL sensor
26= Condenser liquid level regulation with CAREL sensor
(*) only for CAREL valve drivers; (**) control only settable on driver A, howe-
ver corresponds to the entire controller.
Tab. 5.a
Note:
•
R404A condensers with subcritical CO
2
refer to superheat control for valves
installed in cascading systems where the flow of R404A (or other refrigerant)
in an exchanger acting as the CO
2
condenser needs to be controlled;
•
“perturbed” cabinet/cold room or air-conditioner/chiller refer to units
that momentarily or permanently operate with swinging condensing or
evaporation pressure;
•
for the Auxiliary control setting see Appendix 2
The following paragraphs explain all the types of control that can be set on
EVD evolution twin.
5.2 Superheat
control
The primary purpose of the electronic valve is ensure that the flow-rate of
refrigerant that flows through the nozzle corresponds to the flow-rate required
by the compressor. In this way, the evaporation process will take place along
the entire length of the evaporator and there will be no liquid at the outlet and
consequently in the branch that runs to the compressor.
As liquid is not compressible, it may cause damage to the compressor and even
breakage if the quantity is considerable and the situation lasts some time.
Содержание EVD Evolution Twin
Страница 2: ......
Страница 4: ......
Страница 6: ......
Страница 66: ...ENG EVD Evolution TWIN 0300006EN rel 2 6 31 01 2019 66 Note...
Страница 67: ......