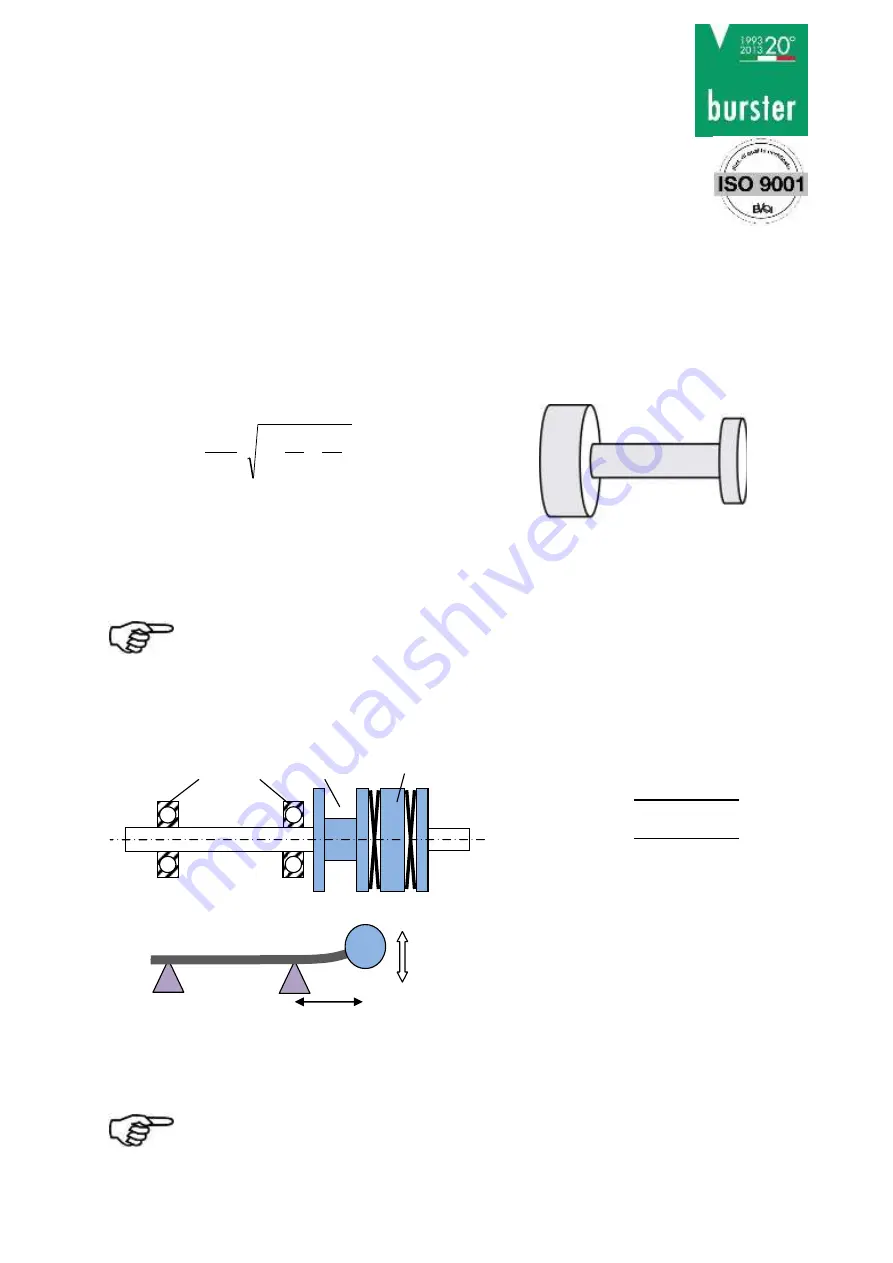
burster Italia s.r.l. · Sede legale ed operativa · Via Cesare Battisti, 16/18 · 24035 Curno (BG) · Tel. +39 035 618120 · Fax +39 035 618250
e-mail: [email protected] · http://www.burster.it
C.F. e P.IVA 11048400151 · Capitale sociale Euro 49.920,00 · R.E.A. di Bergamo 276749
Apparecchi di misura di precisione. Sensori e Sistemi
per grandezze elettriche, termiche e meccaniche
6.4
Dynamic Torques
6.4.1 General
The static calibration procedure of torque sensors is also valid for dynamic applications.
Note: The frequency of torques must be smaller than the natural frequency of the mechanical
measurement setup.
The band width of alternating torque must be limited to 70 % of the nominal torque.
6.4.2 Torsional Natural Resonances
Estimation of the mechanical natural frequencies:
2
1
0
1
1
2
1
J
J
c
f
f
0
J
1
, J
2
c
= Natural Frequency in Hz
= Moment of Inertia in kg*m²
= Torsional Rigidity in Nm/rad
Further methods for the calculation of natural resonances are corresponding purchasable programs or
books (e.g. Holzer-Procedure (Dubbel, Taschenbuch für den Maschinenbau, Springer Verlag) or
equivalent commercially available programs.
6.4.3 Bending Natural Resonances
Together with the shaft and the couplings, the sensor forms a bending vibration.
Bending vibrations are stimulated by unbalance.
balance well
Do not operate the system in bending natural resonance.
Apply bursting protection around the shaft string.
Operation of the device in natural resonance can lead to permanent damages.
Operation of the device in bending natural resonance can lead to permanent damages .
c
√
This applies for bending natural
resonance:
E =
Elasticity modulus of material
d =
Shaft diameter
m =
Mass
= Angular frequency
f
= Natural frequency in Hz
Preferably stable design
Diameter (
d
)
Length
l
preferably short
Mounting
Shaft
Sensor with coupling
m
l
m
J
1
J
2