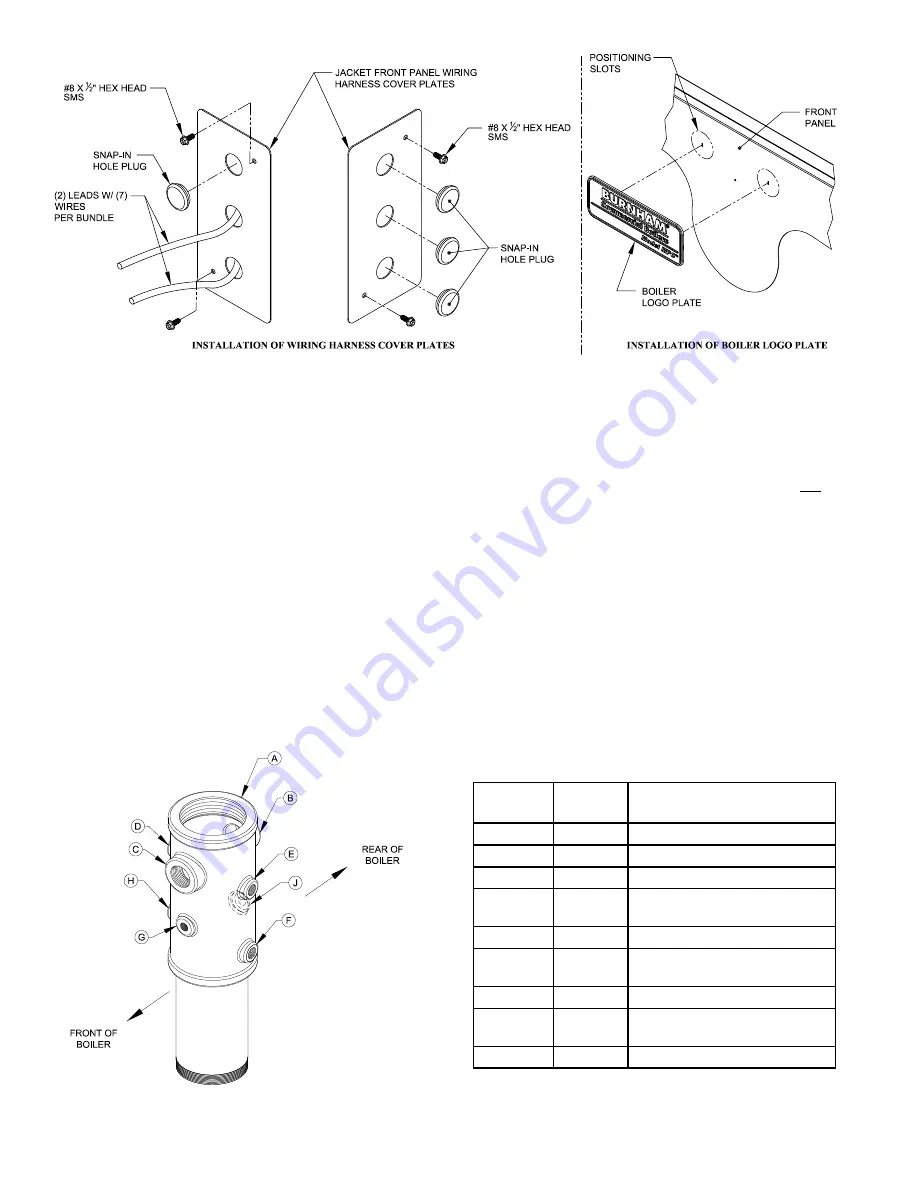
5
1. Harness is split into two (2) 7 wire bundles that exit
side of front panel as shown in Figure 25.
2. Each seven (7) wire harness bundle must be encased
in flexible conduit from cover plate to burner control
panel or junction box.
3. Locate front panel cover plates in JC-1 carton.
4. Determine routing, length and type of ‘BX’
connectors to be used on flexible conduit.
5. Mount ‘BX’ connector and flexible conduit to
one (1) front panel cover plate. Pull wire bundles
through conduit.
6. Secure cover plate to side of jacket front panel using
(2) #8 x 1/2” lg. hex head SMS.
7. Locate and install one (1) plastic hole plug
(provided) into unused 7/8” dia. hole in cover plate.
8. Install remaining cover on opposite side of front
panel. Secure with #8 x 1/2” lg. hex head SMS,
push (3) plastic hole plugs into 7/8” dia. holes.
Figure 7: Install Jacket Front Panel Harness Cover Plates and Logo Plate
9. Connect other end of flexible conduit to burner
control panel or junction box. Connect control/
safety circuit wires to appropriate terminals per
wiring diagram provided with burner.
Q.
Install Logo Plate on Jacket Front Panel if Optional
Jacket Split Burner Swing Door Cover Panels are
not
to
be used.
Locate Logo Plate shipped in Instruction Envelope.
Peel paper off adhesive strips and install by inserting
positioning tabs on rear of Logo Plate into slotted
openings located at top of front panel shown in Figure
37.
If optional BSD cover panels are used, Logo Plate will
be installed on the cover as instructed in later steps.
R.
Locate Water Trim and Control Carton marked ‘WT’
and remove contents. Check Equipment Check List for
proper working pressure/relief valve. Install standard
trim and controls as follows:
1. See Figure 38 for purpose of tappings on supply
manifold.
Figure 8: Purpose of Tappings in Supply Manifold
*
Location
Size of
Tapping
Purpose of Tapping
A
4” Flange
Supply
B
1½”
Relief Valve
C
1½”
Auxiliary Tapping (Plug)
D
¾”
Operating Temperature
Limit Control
E
¾”
Probe L.W.C.O.
F
¾”
High Temperature Limit Control /
Manual Reset
G
½”
Temperature / Pressure Gauge
H
¾”
Low / High / Low
or Modulating Control
J
½
Low Fire Hold Control
*
Supply Manifold must be installed with 1½” coupling ‘B’
or ‘C’ aligned with front of boiler when water tight.
Содержание MPC
Страница 19: ...19 Figure 5 Manual or Hydraulic Draw up Section Assembly ...
Страница 28: ...28 Table VII Modular Return Water Mixing Tube RWMT RC ...
Страница 29: ...29 Figure 13 Return Water Mixing Tube RC Assembly and Installation ...
Страница 78: ...78 Figure 56 MPC Common Bare Boiler Components ...
Страница 80: ...80 Figure 56 MPC Common Bare Boiler Components continued ...
Страница 82: ...82 Figure 57 MPC Front Center Section Frame Rail Assembly ...
Страница 84: ...84 Figure 58 MPC Rear Section Frame Rail Assembly ...
Страница 86: ...86 Figure 59 MPC Return Water Mixing Tube RC Assembly ...
Страница 88: ...88 Figure 60 MPC Heat Exchanger Insulation Wrapper ...
Страница 90: ...90 Figure 61 MPC Internal Wiring Harness Components ...
Страница 92: ...92 Figure 62 MPC Jacket Panel Assembly ...
Страница 94: ...94 Figure 62 MPC Jacket Panel Assembly continued ...
Страница 96: ...96 Figure 63 MPC 2 nd and 3 rd Pass Flueway Baffles ...
Страница 98: ...98 Figure 64 MPC Standard 50 PSI Trim Control with 30 PSI and 80 PSI Working Pressure Trim Options ...
Страница 100: ...100 Figure 64 MPC Standard 50 PSI Trim and Control with 30 PSI and 80 PSI Working Pressure Trim Options continued ...
Страница 102: ...102 Figure 65 MPC Optional Controls ...