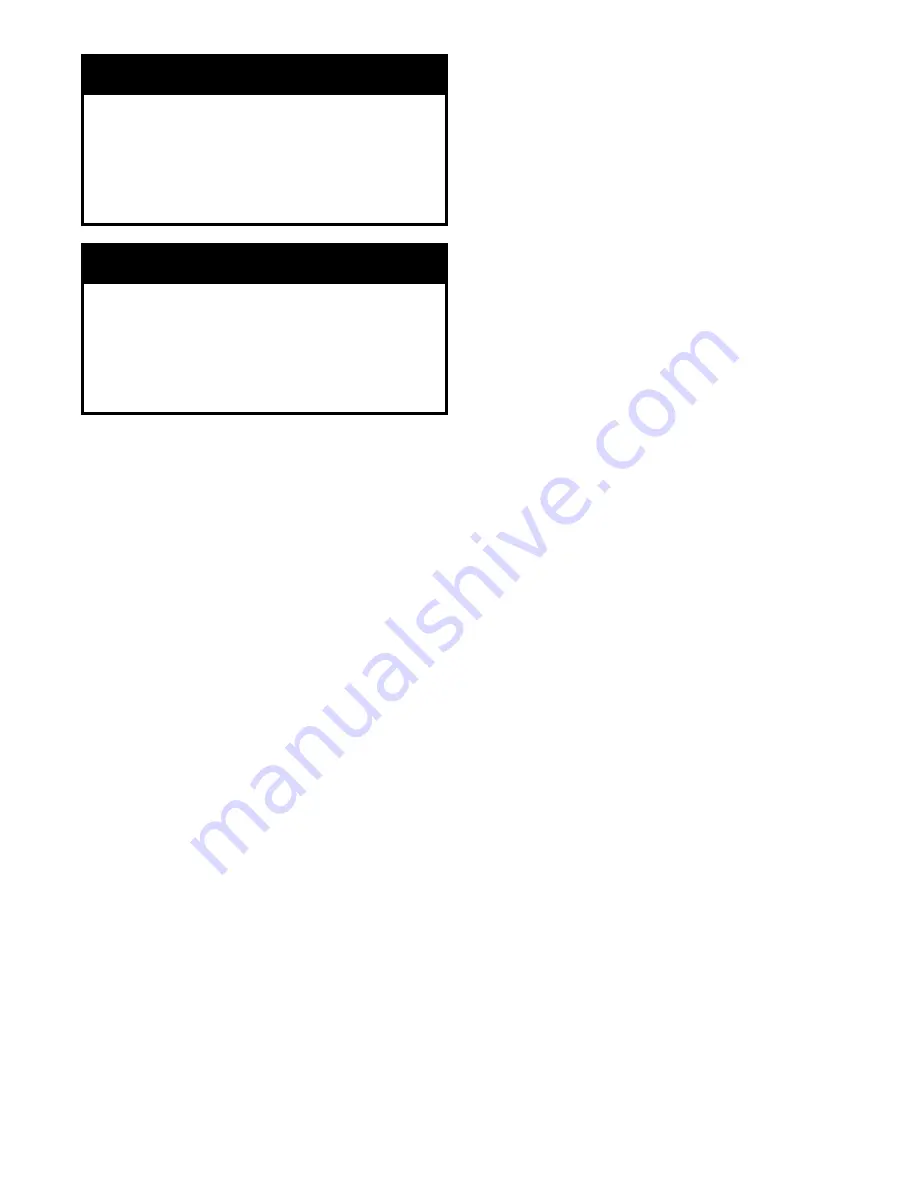
1
WARNING
This is a forced draft fired boiler and sealant must
be applied where specified for proper and safe
performance. Burnham Commercial has approved
section joint sealants (silastics) manufactured
by Dow-Corning under the product number RTV
76, and Sil-Bond under the product number RTV
6500.
WARNING
Sections must be drawn-up tight immediately
after properly applying sealant for best results.
Although sections may be joined within two
() hours of applying sealant, humidity and
temperature affect cure time. If a “thick skin” has
been formed on the sealant bead, remove and re-
apply sealant.
step k.
Position the next adjoining section to be
assembled,
so that the side with the sealing
tongue around the combustion chamber and
perimeter is facing the mating side of the rear
section
. Sections must always be assembled
so that the rope groove on one section mates
to the sealing tongue on the next section in the
assembly.
step l.
Clean and lubricate the nipple ports on the
mating (tongue) side of the adjoining section.
Place the nipple ports of the adjoining section
onto the nipples previously installed in the rear
section. To facilitate assembly, it is advisable
to enter the upper nipple first in its port. Then
enter the lower nipple in it’s respective port. If
necessary, place a lifting bar (crowbar) under the
center of the section and lift the nipple port onto
the upper nipple. Drive section in place with a
heavy block of wood, striking blows as squarely
as possible over nipple ports.
step m.
From Manual Draw-up Kit, locate and
assemble two (2) sets that include a ¾” x 23”
lg. threaded rod, 6½” dia. pressure plate, ¾”
flat washer and ¾” hex nut as shown in Figure
5. Insert one assembly through each of the 3”
and 4” NPT bosses on rear section until pressure
plate is tight against the boss. Locate and place
the 8¾” dia. pressure plate on the opposite end
of threaded rod in upper nipple port. Place
remaining 6½” dia. pressure plate on rod
protruding through lower nipple port. Install a
¾” washer, ¾” coupling spacer, ¾” washer and
¾” hex nut on each rod. Center upper pressure
plates on nipple port and boss while tightening
nut until tension holds assembly in place. Repeat
for lower assembly. Refer to Figure 5 to verify
proper arrangement.
step n.
DRAW UP SECTION SLOWLY
AND EVENLY. When you start, machined
surfaces between adjoining sections should
be approximately 3/8” to 1/2” apart. The 7”
nipple will pull harder than the 3” nipple. If
two (2) people are pulling simultaneously,
stop periodically to verify that gaps between
adjoining sections are equal at both nipple
ports. If not, pull the nipple with the larger
gap until equal before proceeding. Continue
draw-up, paying close attention to the nipple
lubricant as it squeezes when the sections come
in close contact. The lubricant should continue
to squeeze out until the sections are connected
metal to metal at the designated inspection
pads shown in Figure 8.
if the sections still
do not appear to be drawn metal to metal,
use the feeler gauge provided to measure any
gaps at the locations identified in figure 8.
(Unless specified otherwise, gaps should be only
measured at these locations). A maximum gap
of .025”.
KEEP NIPPLES ALIGNED WITH NIPPLE
PORTS. If necessary, tap edge of nipples lightly
with a blunt tool or rod to keep nipples from
cocking while sections are being drawn-up.
DO NOT DRAW UP SECTION WHEN
NIPPLES ARE COCKED. If the torque
required becomes excessive, periodically place a
heavy block of wood over each nipple port and
strike as squarely as possible with several blows
to relieve tension on the draw-up rods.
step o.
Remove Draw-up Rod Assemblies and set
aside.
step p.
Prepare center section on block assembly
to receive next casting, see Figure 5. Clean the
rope grooves around the combustion chamber
and perimeter of the section with a wire brush.
Repeat Step ‘d’ through step ‘p’ with the
following exceptions:
•
During Step ‘d’ procedure, apply multi-
purpose spray adhesive to combustion
chamber rope groove as well as perimeter
groove.
•
During Step ‘e’ procedure, locate 86”
length of red silicone coated fiberglass rope.
Starting at 9 o’clock position, push rope into
groove and continue around combustion
chamber until rope overlaps starting point.
Mark joint, cut-off excess and seal joint per
instructions.
•
During Step ‘j’ procedure, apply sealant to
the (6) flueway sealing grooves on the center
section.
BE SURE TO APPLY THE SILICONE
COATED FIBERGLASS ROPE AND
SEALANT to the grooved joints between
Содержание MPC
Страница 19: ...19 Figure 5 Manual or Hydraulic Draw up Section Assembly ...
Страница 28: ...28 Table VII Modular Return Water Mixing Tube RWMT RC ...
Страница 29: ...29 Figure 13 Return Water Mixing Tube RC Assembly and Installation ...
Страница 78: ...78 Figure 56 MPC Common Bare Boiler Components ...
Страница 80: ...80 Figure 56 MPC Common Bare Boiler Components continued ...
Страница 82: ...82 Figure 57 MPC Front Center Section Frame Rail Assembly ...
Страница 84: ...84 Figure 58 MPC Rear Section Frame Rail Assembly ...
Страница 86: ...86 Figure 59 MPC Return Water Mixing Tube RC Assembly ...
Страница 88: ...88 Figure 60 MPC Heat Exchanger Insulation Wrapper ...
Страница 90: ...90 Figure 61 MPC Internal Wiring Harness Components ...
Страница 92: ...92 Figure 62 MPC Jacket Panel Assembly ...
Страница 94: ...94 Figure 62 MPC Jacket Panel Assembly continued ...
Страница 96: ...96 Figure 63 MPC 2 nd and 3 rd Pass Flueway Baffles ...
Страница 98: ...98 Figure 64 MPC Standard 50 PSI Trim Control with 30 PSI and 80 PSI Working Pressure Trim Options ...
Страница 100: ...100 Figure 64 MPC Standard 50 PSI Trim and Control with 30 PSI and 80 PSI Working Pressure Trim Options continued ...
Страница 102: ...102 Figure 65 MPC Optional Controls ...