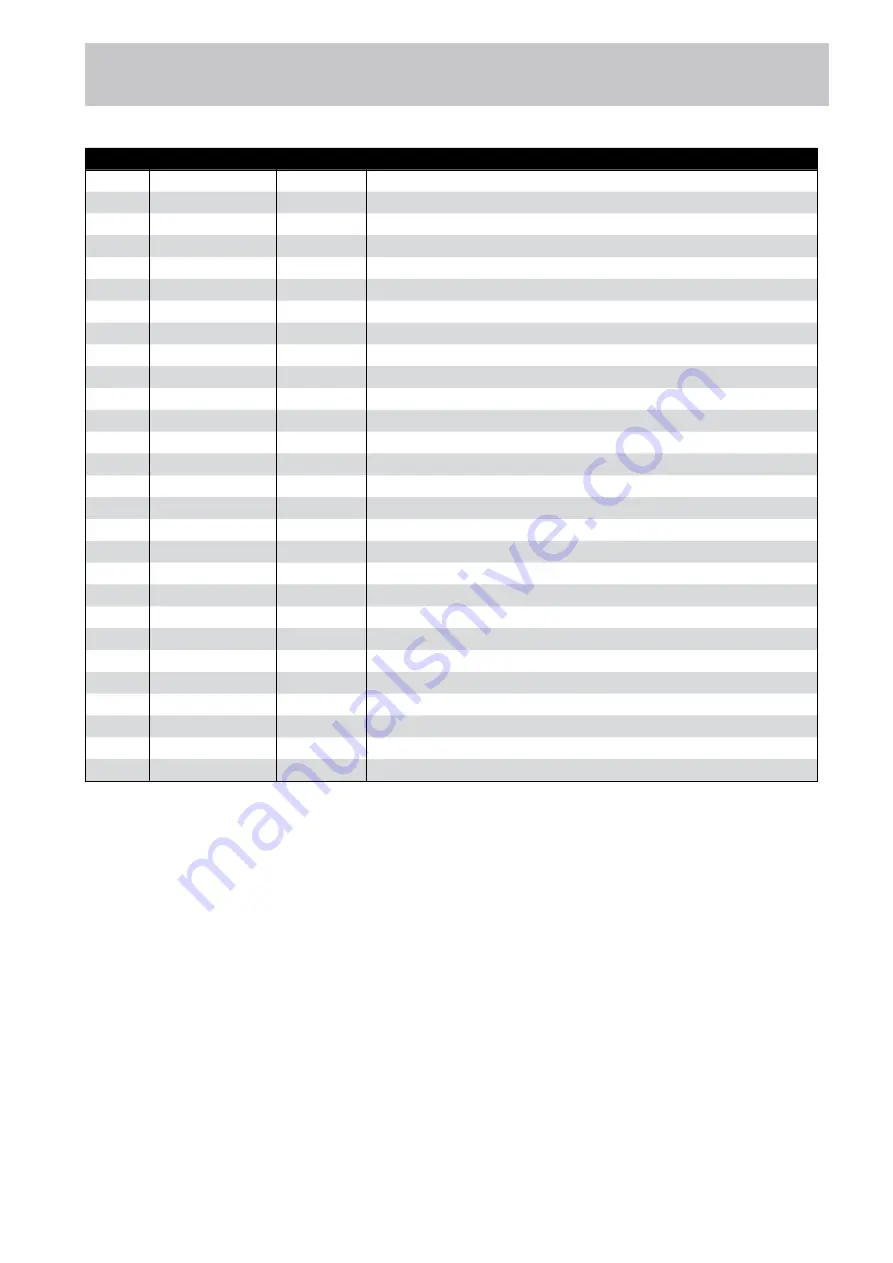
Spare parts list
13
Spare parts manual application unit (bead version)
Item
Order no.
Quantity
Designation
1
FD0241
1
Nozzle long 0.8 mm
2
FD0242
1
Nozzle long 1.0 mm
3
FD0243
1
Nozzle long 1.2 mm
4
FD0244
1
Nozzle long 1.5 mm
5
FD0245
1
Nozzle long 2.0 mm
6
FD0246
1
Nozzle long 3.0 mm
7
H105420
1
Nozzle head with heating cylinder
8
H105505
1
Flap
9
H105523
1
Spare part grip casing (see Fig. 2/1 on page 16)
10
H105524
1
Trigger and mounting parts (see Fig. 2/3 on page 18)
11
H105529
1
Heat insulation half shell (see Fig. 2/2 on page 17)
12
H105540
1
Heating cartridge with cable
13
H105702
1
Warning decal
14
H105703
1
Warning decal
15
HDH0157
1
Spacer ring
16
HDH0158
1
Support ring
17
KD0267
1
Support ring
18
KD0438
1
Fan-shaped washer
19
KD0495
7
Plastite screw
20
KDN0737
1
Screw
21
KDN1288
2
Tapping screw DIN 7981
22
LDH0144
2
O-ring
23
MDM0103
1
Set of needles, complete
24
NCH0416
1
Temperature sensor
25
NCN0422
1
Radio transmitter for hand-operated pistol
26
NCN0429
2
Magnet for radio control
27
NCN0442
1
Battery CR 2032 LI-MN 3V
28
NDM0002
2
Clamping block
Содержание HB 5010
Страница 10: ...2...
Страница 14: ...Special security advice 6...
Страница 16: ...Technical data 8 Figure 2 1 2 Location of type plate on the inside of the unit...
Страница 28: ...Operation 20...
Страница 40: ...Operation 32...
Страница 57: ...Repairs 49...
Страница 60: ......
Страница 62: ...Table of Contents 4 Table of contents...
Страница 64: ...Specific security advice 6...
Страница 68: ...Technical Data 10...
Страница 76: ...Maintenance 18...
Страница 80: ......
Страница 82: ...4 Inhaltsverzeichnis...
Страница 84: ...Specific safety instructions 6...
Страница 90: ...Construction and function 12...
Страница 92: ...Technical data 14...
Страница 104: ...What happens if 26...
Страница 107: ...Accessories 29...
Страница 110: ...Ersatzteillisten...
Страница 115: ...Spare parts list 3 1 HB 5010 Tank System basic unit Fig 1 1 Spare parts for basic unit Part 1...
Страница 128: ...Spare parts list 16 2 3 Spare parts bead and spray 19 9 Fig 2 11 Grip casing both versions...
Страница 129: ...Spare parts list 17 11 Fig 2 12 Heat insulation half shell both versions...
Страница 130: ...18 Spare parts list 10 Fig 2 13 Trigger and mounting parts both versions...
Страница 133: ...Table of contents 21...
Страница 136: ...Table of Contents 2...
Страница 138: ...4...