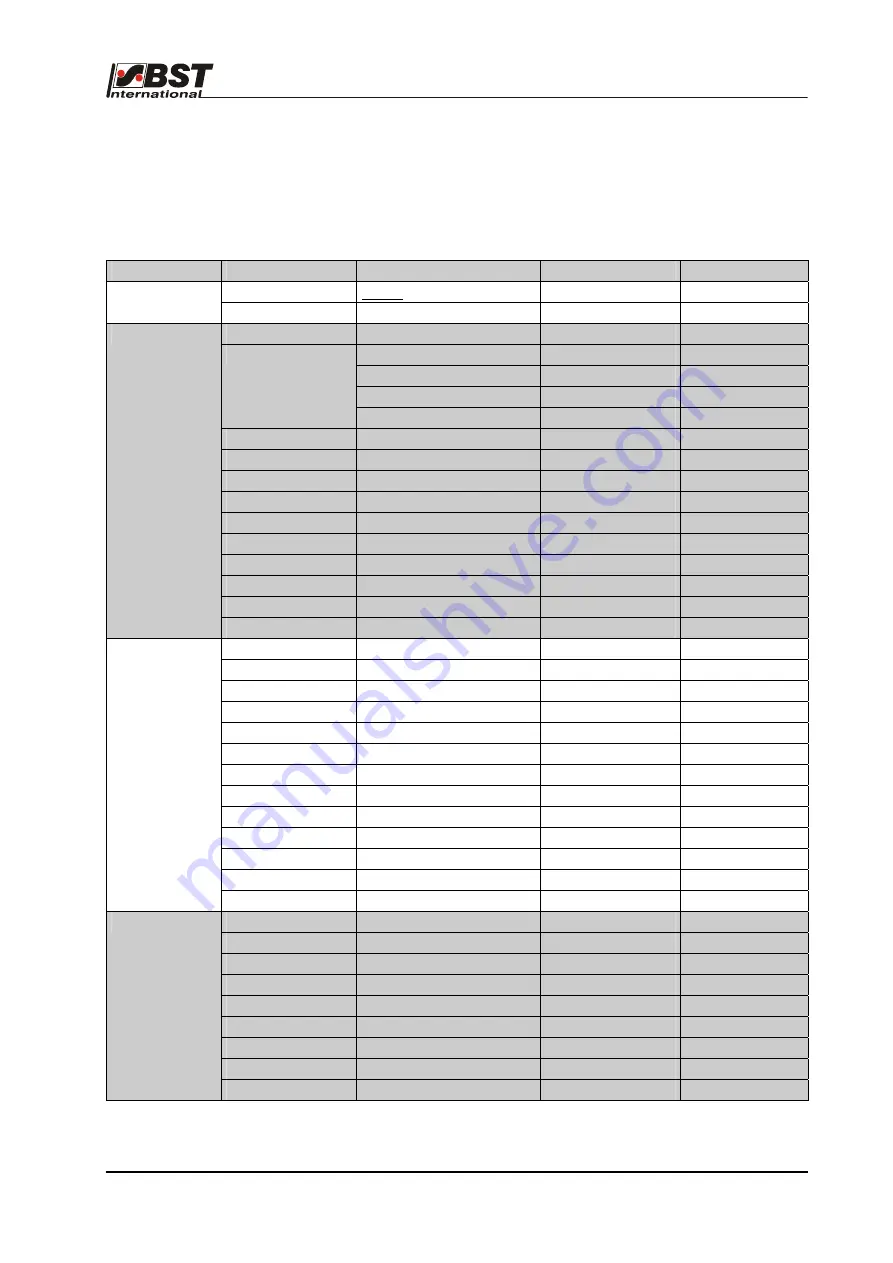
Default settings
D 2
ekrPro Com
60
web guide controller
EDV-No.:
MD.191.01.05/1.6.x Chapter:
D2
with analog sensors
Date:
23.11.2007
Page:
1/6
Appendix D 2 Default settings
The default settings have been set up in the controller in the
factory. The following settings are set up again after a reset has
been carried out:
Menu
Parameter Level 1 Parameter Level 2
Parameter Level 3 Default Value
User Level
Active user level
Admin.
Change User
Password
2
Type (EMS&Hydr.)
EMS
17
Zero elevation [%]
0
Dither amplitude [mA]
0
Use teach table
off
Hydraulics Add-on
Specific current control
off
Direction
Dir. inverted
off
SC Transducer
Type & Dir.
Type
EMS
Pot.
Inversion
off
Pos. Limit
active
off
Limit left
-2048
Limit right
+2047
SC W & XP
Setpoint
0
Gain
20.00
Man Pos. Control
off
Actuator
Man Speed
[1/1000]
700
Sensor 1
IR2005
Dark
-2048
Bright
+2047
Inv.
Off
Sensor 2
IR2005
Dark
-2048
Bright
+2047
Inv.
avtive
Sensor 3
not connected
Dark
-2048
Bright
+2047
Inv.
off
Sensors/EFE
EFE Remote Adj.
Choose EFE if present
not connected
Gain & Offset
Edge 1
W
0
xp
5.00
Edge 2
W
0
xp
5.00
Center 1&2
W
0
xp
5.00
Edge 3
W
0
xp
5.00
Control loop
Speed control
active