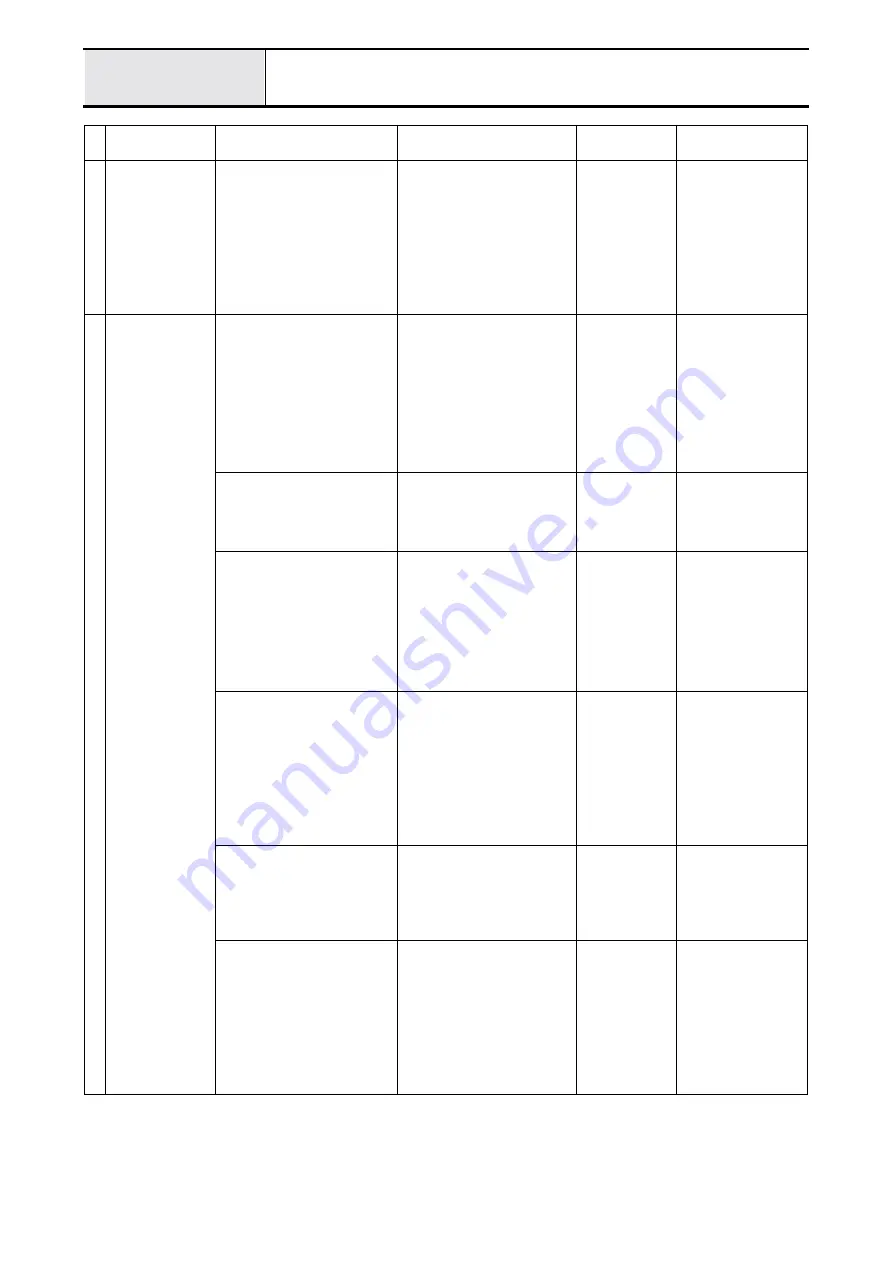
6 - 4
Repair Manual
11 Even if the drop
lever is returned to
the left, the feed
dog stays down
and does not return
(no material feed)
Drop knob damage
Replace drop knob
Drop function
With the needle bar in
the top position and the
drop lever to the right,
check that the feed dog
is down, and moving
the drop lever to the left
and turning the pulley
one turn by hand, that
the feed dog returns to
the original height.
Malfunction of vertical rod seat
Readjust vertical rod seat
operation
Bad vertical drop shaft
Replace vertical adjusting screw
Vertical drop shaft misalignment
Readjust vertical adjusting
screw
12 Bad pattern shape
Blocked by satin
pattern
Fine BH stitches
Straight line feed
too small
Stitches uneven
Vertical rattle in feed dog
Loose feed dog attachment
screw
Readjust feed dog attachment
screw
Back/front rattle
in feed dog
With the feed dog up,
check that there is no
rattle when the feed
dog is lightly moved
back and forth.
Vertical rattle in feed bar
Reattach the feed bar
Damage to horizontal feed cam
Replace lower shaft B assy.
Fork end spring slippage
Assemble spring
Rattle in feed adjuster assy.
Reattach the feed adjuster
assy.
Horizontal rattle in feed dog
Loose feed dog attachment
screw
Readjust feed dog attachment
screw
Left-right rattle in
feed dog
With the feed dog up,
check that there is no
rattle when the feed
dog is lightly moved left
and right.
Horizontal rattle in feed bar
Reattach the feed bar
Bad feed dog height adjustment
Adjust feed dog height
Feed dog height
With the feed dog in the
highest position, check
that the feed dog
comes out 0.9 – 1.1
mm from the top of
needle plate A at the
center of the needle
plate A needle hole.
Bad feed dog front-back position
adjustment
Adjust feed dog front-back
position
Feed dog front-
back position
Rotating the pulley by
hand in a 0 mm feed
position (test mode 3)
with the feed dog
aligned with needle
plate A, check that the
gap between the
middle tooth and the
needle plate is 3.3 – 3.9
mm.
Bad feed dog left-right position
adjustment
Adjust feed dog left-right
position
Feed dog left-
right position
Confirm that the feed
dog has a 0.5 – 0.7 mm
gap left and right
parallel to the needle
plate A needle hole.
Lateral feed bar operation
incorrect.
Reattach the feed bar.
Replace feed module.
Left and right
feed dog position
Select "side feed line"
from the patterns, and
check that the left and
right feed dog position
is uniform with respect
to the needle when the
pulley is turned by hand
and the feed dog
moved to the left and
right.
Problem
Primary factors and causes
Repair method
Items for
Inspection
Inspection method
and standards
Содержание Innov-is NX600
Страница 1: ......
Страница 2: ......
Страница 20: ...1 10 ...
Страница 22: ...2 2 Main parts location diagram Main unit ...
Страница 29: ...2 9 Disassembly Electrical parts and motors location diagram Main unit ...
Страница 36: ...2 16 Thread tension mechanism location diagram Main unit ...
Страница 42: ...2 22 Bobbin winder mechanism location diagram Main unit ...
Страница 46: ...2 26 Rotary hook drive mechanism Feed and bobbin mechanism Cutter assy location diagram Main unit ...
Страница 49: ...2 29 Disassembly Needle bar presser mechanism Upper shaft mechanism location diagram Main unit ...
Страница 53: ...2 33 Disassembly Needle presser module breakout diagram Modules ...
Страница 64: ...2 44 Feed and bobbin module breakout diagram Modules ...
Страница 72: ...2 52 Thread cutter module breakout diagram Modules ...
Страница 76: ...2 56 Thread cutter module Modules ...
Страница 78: ...3 2 Needle bar presser mechanism upper shaft mechanism location diagram Main unit ...
Страница 83: ...3 7 Assembly Rotary hook drive mechanism Feed and bobbin mechanism Cutter assy location diagram Main unit ...
Страница 88: ...3 12 Bobbin winder mechanism location diagram Main unit ...
Страница 92: ...3 16 Thread tension mechanism location diagram Main unit ...
Страница 100: ...3 24 Electrical parts and motors location diagram Main unit ...
Страница 109: ...3 33 Assembly Main parts location diagram Main unit ...
Страница 117: ...3 41 Assembly Needle presser module breakout diagram Modules ...
Страница 136: ...3 60 Feed module breakout diagram Modules ...
Страница 150: ...3 74 Thread cutter module breakout diagram Modules ...
Страница 184: ...4 30 Adjustment Modules ...
Страница 203: ...6 1 6 Repair Manual ...
Страница 213: ......
Страница 214: ......