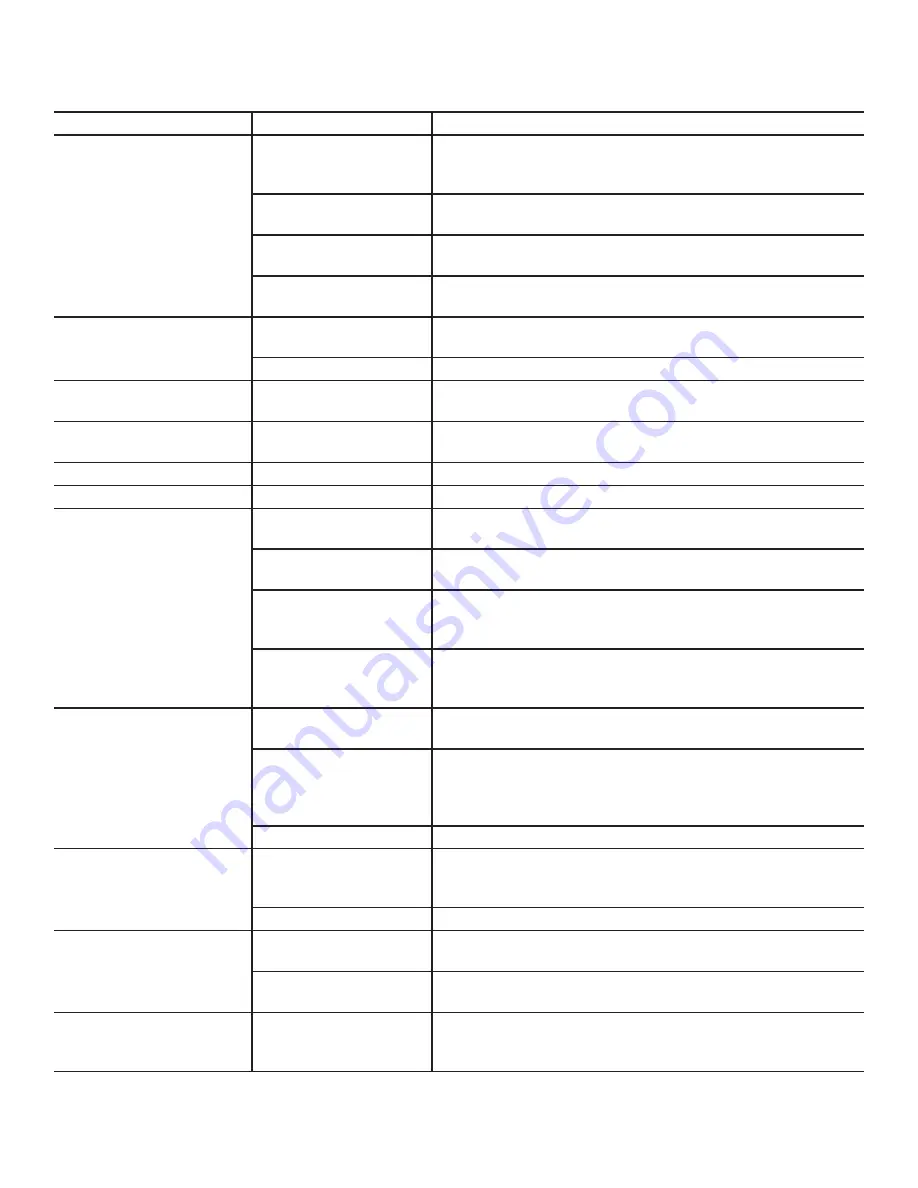
10
Condition/Problem
Things to Check
Solution
Unit will not turn on, power switch
does NOT light up
Outlet
Make sure outlet is functioning correctly. Verify this by plugging another
device (ex: lamp) into the outlet. If outlet is connected to a light switch, check
to make sure it is on. If outlet is not functioning find a working outlet.
Power cord not plugged in
Make sure the power cord is firmly secured to A/C inlet on the unit and firmly
inserted into a non-GFI wall socket.
Power switch turned off
Make sure the power switch at the rear of the unit is in the “ON” position.
Switch will light up red to indicate power is present.
Safety key not plugged in
Plug Safety Key into Console (See Safety Key - Emergency Stop Procedures
within Features section).
Power switch is lit but display
screen does not turn on
I/O Cable
Check I/O Cable connections at back of console. If display still will not light
up, replace I/O Cable.
If problem persists
Contact Customer Service.
Speed displayed is not accurate
Display set to wrong unit of
measure. (English/Metric)
Change display units.
Console displays drive error code
(“C”, “S”, or “H” with a number )
Unit needs to be restarted
Cycle power off for 10 seconds using power switch at rear of unit, then
restart.
Error code diagnostic
Contact Customer Service.
Console displays “LUbE” code
Belt lubrication
Consult lubrication schedule and apply if necessary. Push START button.
Heart rate not displayed while
using chest strap
Transmitter not making good
contact with skin
Moisten skin contact area on the chest strap.
Electromagnetic interference
Turn off any television, AM radio, microwave, or computer within 6 feet (2
meters) of the fitness machine.
Chest strap transmitter
Test chest strap with another HR monitoring device such as HR watch or a
machine at a gym. If transmitter has good skin contact and still is not found
to be emitting HR signal, replace chest strap transmitter.
HR receiver
If chest strap is known to work with other devices and no sources of interfer-
ence are present, or console has been tested with a Pulse Simulator and is
not receiving the signal, contact Customer Care for replacement HR receiver.
Walking belt misalignment
Rear belt guides
Belts should ride on top of walking belt guides at the outside edge of
treadles.
Tracking adjustment
Belts are not required to be perfectly centered and are typically farther out in
the rear than they are in the front. This may vary depending on user’s stride.
If belt is tracking to one side far enough to cause rubbing of belt, follow the
“Adjusting the Walking Belts” procedure.
If problem persists
Contact Customer Care for further assistance.
Speed dependent grinding or
scraping noise
Belt alignment
Check walking belt alignment. Belt contact with metal guides under Treadle
can make a loud grinding sound. If belts are misaligned, follow the “Adjusting
the Walking Belts” procedure.
Rollers or motor
Contact Customer Care for further assistance.
Knocking noises when unit is
operating
IGUS bushing
If knocking sound seems to be coming directly from the rear roller, check
IGUS (yellow “hat” shaped) bushings and replace if cracked.
Hydraulic cylinder bolts
Check and tighten both upper and lower bolts that connect the hydraulic
cylinders to the unit.
“Tick” sound once per revolution
or scraping noise from under
Treadle
Belt alignment
Belt seam may be contacting metal belt guide under treadle. Slight adjust-
ment of belt should alleviate noise. Follow the “Adjusting the Walking Belts”
procedure.
TROUBLESHOOTING