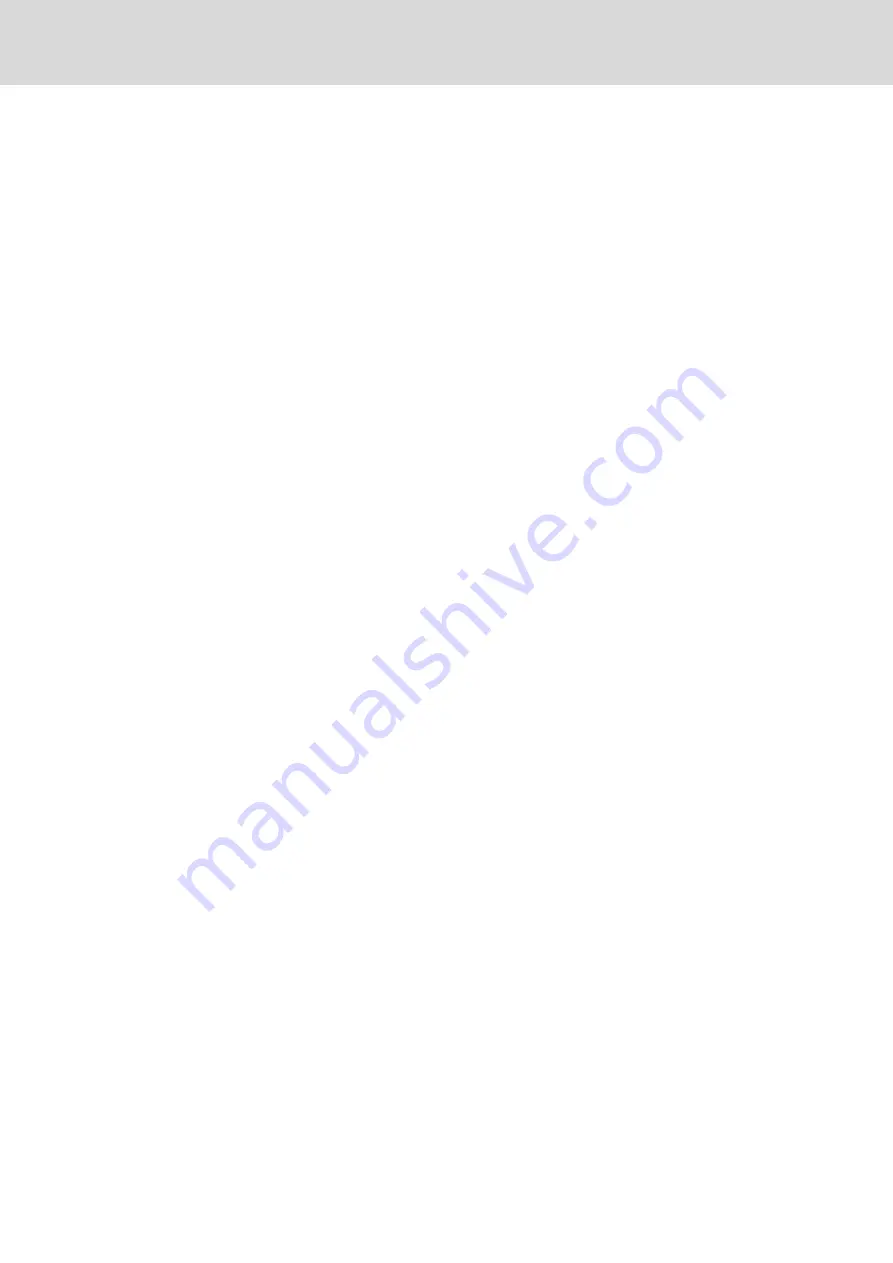
●
Improper or wrong wiring or cable connection
●
Operator errors
●
Wrong input of parameters before commissioning
●
Malfunction of sensors and encoders
●
Defective components
●
Software or firmware errors
These errors can occur immediately after equipment is switched on or even
after an unspecified time of trouble-free operation.
The monitoring functions in the components of the electric drive and control
system will normally be sufficient to avoid malfunction in the connected drives.
Regarding personal safety, especially the danger of injury and/or property dam‐
age, this alone cannot be relied upon to ensure complete safety. Until the
integrated monitoring functions become effective, it must be assumed in any
case that faulty drive movements will occur. The extent of faulty drive move‐
ments depends upon the type of control and the state of operation.
Dangerous movements! Danger to life, risk of injury, serious injury or property
damage!
A risk assessment must be prepared for the installation or machine, with its
specific conditions, in which the components of the electric drive and control
system are installed.
As a result of the risk assessment, the user must provide for monitoring func‐
tions and higher-level measures on the installation side for personal safety. The
safety regulations applicable to the installation or machine must be taken into
consideration. Unintended machine movements or other malfunctions are pos‐
sible if safety devices are disabled, bypassed or not activated.
To avoid accidents, injury and/or property damage:
●
Keep free and clear of the machine’s range of motion and moving machine
parts. Prevent personnel from accidentally entering the machine’s range
of motion by using, for example:
–
Safety fences
–
Safety guards
–
Protective coverings
–
Light barriers
●
Make sure the safety fences and protective coverings are strong enough
to resist maximum possible kinetic energy.
●
Mount emergency stopping switches in the immediate reach of the oper‐
ator. Before commissioning, verify that the emergency stopping equip‐
ment works. Do not operate the machine if the emergency stopping switch
is not working.
●
Prevent unintended start-up. Isolate the drive power connection by means
of OFF switches/OFF buttons or use a safe starting lockout.
●
Make sure that the drives are brought to safe standstill before accessing
or entering the danger zone.
●
Additionally secure vertical axes against falling or dropping after switching
off the motor power by, for example,
–
mechanically securing the vertical axes,
–
adding an external braking/arrester/clamping mechanism or
–
ensuring sufficient counterbalancing of the vertical axes.
DOK-SUPPL*-VEP*XX.4***-PR03-EN-P
Rexroth IndraControl VEP **.4 Embedded Terminal
Bosch Rexroth AG
19/139
Safety Instructions for Electric Drives and Controls
Содержание Rexroth IndraControl VEP 30.4
Страница 1: ...Electric Drives and Controls Pneumatics Service Linear Motion and Assembly Technologies Hydraulics ...
Страница 8: ...Bosch Rexroth AG DOK SUPPL VEP XX 4 PR03 EN P Rexroth IndraControl VEP 4 Embedded Terminal VI 139 ...
Страница 26: ...Bosch Rexroth AG DOK SUPPL VEP XX 4 PR03 EN P Rexroth IndraControl VEP 4 Embedded Terminal 24 139 ...
Страница 36: ...Bosch Rexroth AG DOK SUPPL VEP XX 4 PR03 EN P Rexroth IndraControl VEP 4 Embedded Terminal 34 139 ...
Страница 78: ...Bosch Rexroth AG DOK SUPPL VEP XX 4 PR03 EN P Rexroth IndraControl VEP 4 Embedded Terminal 76 139 ...
Страница 126: ...Bosch Rexroth AG DOK SUPPL VEP XX 4 PR03 EN P Rexroth IndraControl VEP 4 Embedded Terminal 124 139 ...
Страница 134: ...Bosch Rexroth AG DOK SUPPL VEP XX 4 PR03 EN P Rexroth IndraControl VEP 4 Embedded Terminal 132 139 ...
Страница 136: ...Bosch Rexroth AG DOK SUPPL VEP XX 4 PR03 EN P Rexroth IndraControl VEP 4 Embedded Terminal 134 139 ...
Страница 140: ...Bosch Rexroth AG DOK SUPPL VEP XX 4 PR03 EN P Rexroth IndraControl VEP 4 Embedded Terminal 138 139 ...
Страница 141: ...Notes DOK SUPPL VEP XX 4 PR03 EN P Rexroth IndraControl VEP 4 Embedded Terminal Bosch Rexroth AG 139 139 ...