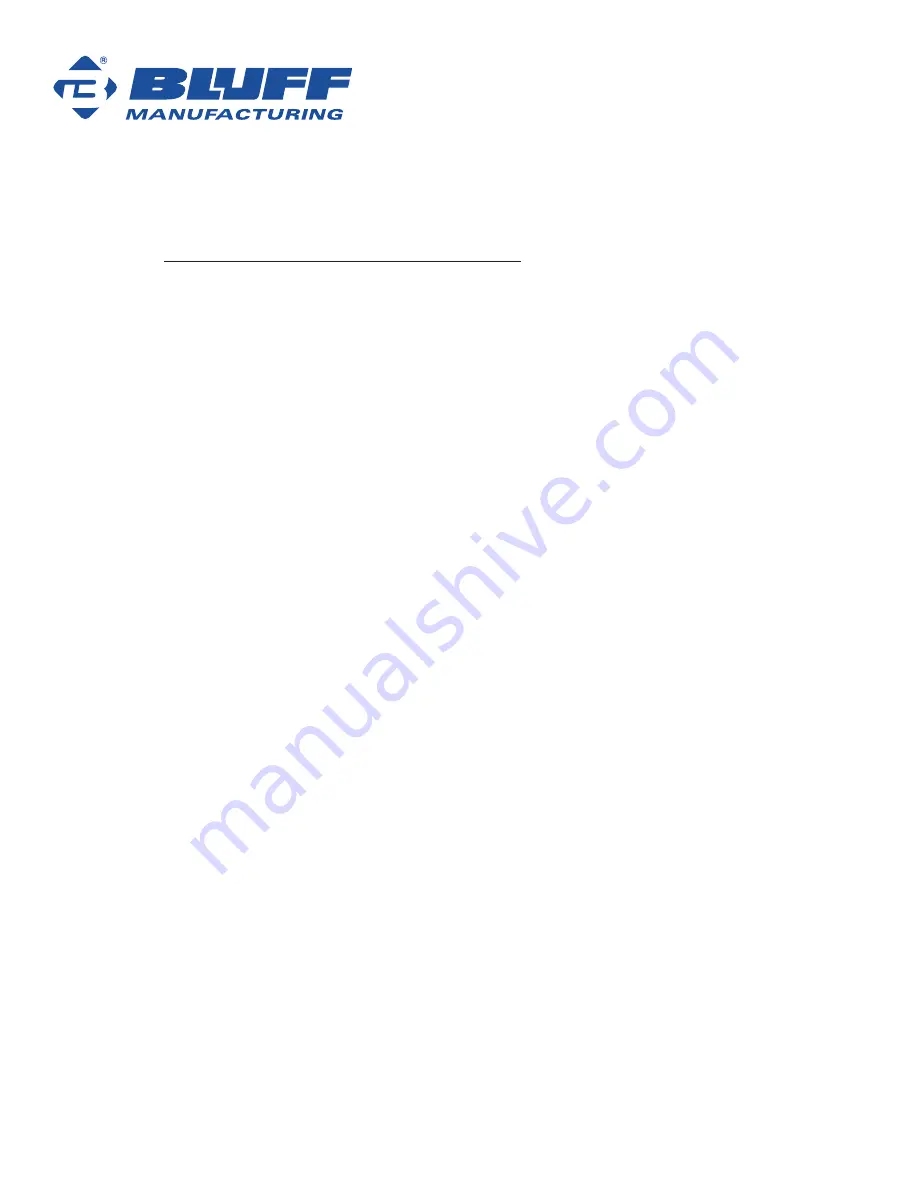
49
DuraSweeper
®
Bluff DuraSweeper
®
Snow Removal System Warranty
Bluff Manufacturing warranties our products to be free from defects in material and workmanship for
a period of one year from shipping date to original purchaser. Warranty eligibility requires all products
are used and serviced in accordance with the company’s recommendations, product selection guides,
product manuals and installation instructions.
Steel Structure: limited 10 year warranty
Brush motor: limited one year warranty
Brush: limited 6-month warranty
Electrical Panel: limited one-year warranty
Hoist Motor: limited one-year warranty
Bluff Manufacturing’s obligation under this warranty shall be limited to the repair, by Bluff Manufacturing
or a Bluff Manufacturing authorized technician, or exchange of any part of parts which may prove
defective under normal service within the time limitations set forth above, and which our examination
shall disclose to our satisfaction to be defective. Bluff Manufacturing requires the purchaser to send
date stamped photographs for initial review of warranty claim products.
This limited warranty does not cover any defects, malfunction or failure caused by or resulting from
improper or unauthorized service, maintenance, installation repair or use not in conformance or
accordance with Bluff Manufacturing’s recommendations, product selection guides, product manuals
or installation instructions and the intended use and capacities or specifications or from abuse, neglect,
accident, weather related issues or any other cause beyond the control of Bluff Manufacturing. This
limited warranty is made only to the original purchaser, which shall be deemed to mean that person or
organization to which the product is originally shipped or installed.
Bluff Manufacturing does not approve nor authorize any other person or entity to obligate Bluff
Manufacturing to any other liability not described herein concerning the sale of its products.
Bluff Manufacturing shall not be liable for any incidental or consequential damages. And liability
hereunder is expressly limited to repair or replacement of any part or parts which may prove defective
within the time prescribed hereon.
This warranty is expressly in lieu of all other warranties, expressed or implied, including the warranties
of merchantability and fitness for a particular purpose and all other obligations or liabilities on our part.