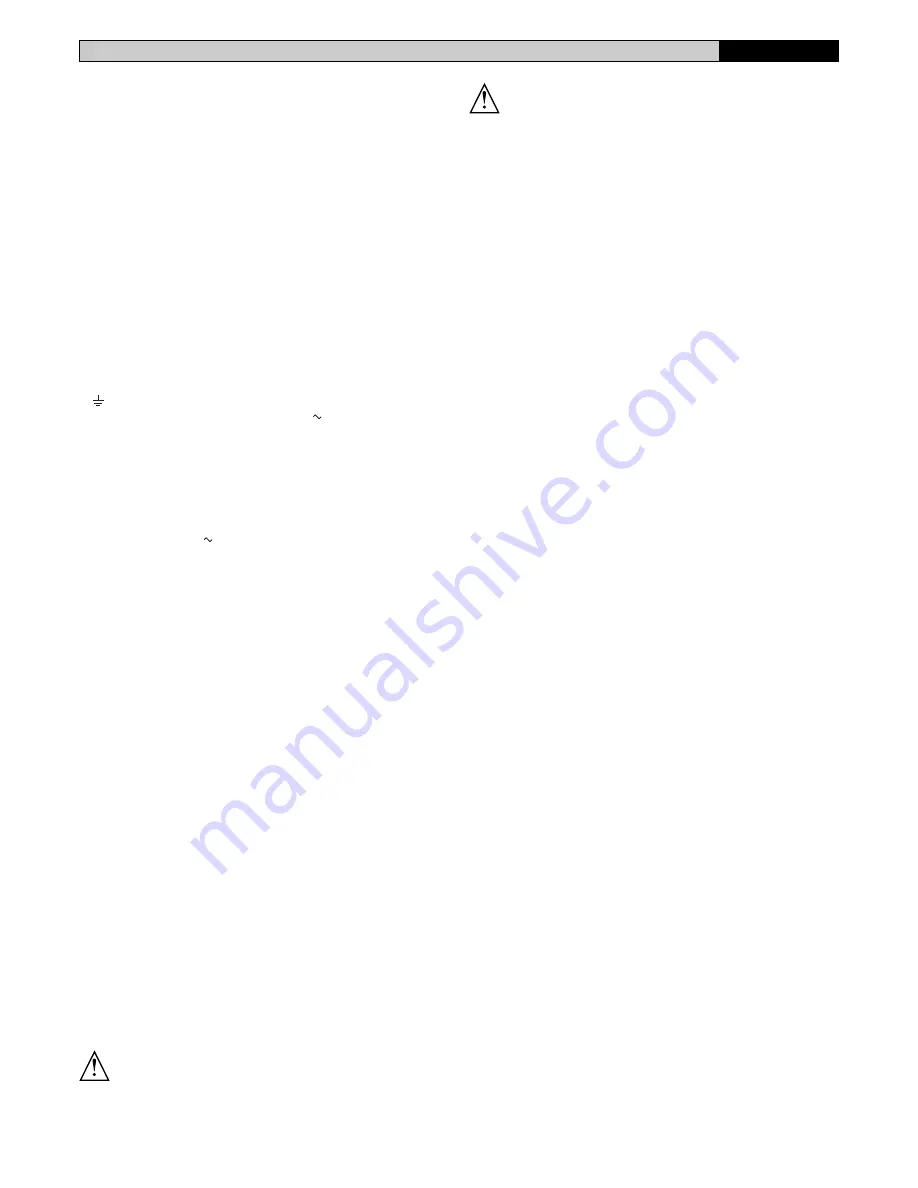
ICARO Ver. 03 -
15
D811310_03
INSTALLATION MANUAL
ENGLISH
12) TERMINAL BOARD CONNECTIONS
First pass the appropriate electric cables through the raceways and fix the
various automation components to the chosen points, then connect them
following the directions and diagrams contained in the control unit instruction
manual.
Carry out phase, neutral and (compulsory) earth connections. The protection
wire (earth) with yellow/green insulating sheath must be connected to the
appropriate terminals marked by their symbol.
Operate the automation only after having connected and checked all the
safety devices.
The mains power supply cables must be stripped as little as possible; the
power supply cable earth wire must be stripped for a greater length, in order
to reach the terminal purposely arranged in the box (fig. 16 ref. “A”).
The P1 cable-clamp is reserved for the mains power supply cables, the P2
cable-clamp is reserved for the accessory cables and safety devices.
The cables must be tied by additional fastening next to the terminals, by
means of clips for example.
All the operator wiring operations must be carried out by qualified personnel.
A description of the terminals in the control board mod. LEO mounted on the
actuator (fig.14) is provided here below:
JP1
1
GND terminal
2-3
Single-phase mains supply 230V
±
10% 50Hz (2=N) (3=L)
JP2
4-5
Blinker connection (mains voltage) 40W Max.
6-7-8-9
Motor connection:
6 operation 1 (brown) + capacitor
7 common (blue)
8 operation 2 (black)
9 capacitor
JP3
10-11
Output 24V
180mA max – power supply for photocells or
other devices.
12-13
Gate-open warning light output (24V 3W max)
JP5
Encoder connection
WARNING!
The maximum length of the connection cable of
the encoder should not exceed 3.00 m.
JP6
21-22
Open-Close button (N.O. Start), key selector.
21-23
Block button (N.C. Stop). If not used, leave jumped.
21-24
Photocell input (N.C.). If not used, leave jumped.
21-25
Opening limit switch connection (N.C. SWO). If not used,
leave jumped.
21-26
Closing limit switch connection (N.C. SWC). If not used, leave
jumped.
21-27
Pedestrian button connection (N.O. Ped)
21-28
Open-Button connection (N.O. Open)
21-29
Close-Button connection (N.O. Close)
21-30
Rubber edge connection (N.C.). If not used, leave jumped.
21-31
Timer input connection (N.O.). If the contact is open the leaves
close and the gate is ready for normal operation. If the contact
is closed (N.C.), the leaves open and remain open until the
contact is opened. If not used, leave jumped.
JP9
34
TX1 serial output
35
TX2 serial output
36
RX1 serial imput
37
RX2 serial input
38-39
Antenna input for snap-in radio receiver board (38 signal - 39
braid). Cable RG58
40-41
Second radio channel output of twin-channel receiver board
WARNING
- If the opening direction is not correct, invert the motor
connections no. 6 and 8 and connections no. 25 and 26 of the opening and
closing limit switches.
13) MOTOR TORQUE SETTING
WARNING: Check that the impact force value measured at the
points established by the EN 12445 standard is lower than that
specified in the EN 12453 standard.
The setting of the motor torque is electronically controlled by an encoder.
Refer to the LEO control board instructions for a correct setting of the
electronic antisquash safety device.
WARNING! The ICARO actuator does not offer the possibility of
adjusting the safety clutch. It is therefore necessary to use a
control board prearranged for the electronic control of the
motor torque.
14) MANUAL RELEASE
The manual or emergency release should only be activated when the gate
has to be opened manually or whenever the automation is not correctly or
totally functioning.
To carry out the emergency manoeuvre, proceed as follows:
•
Insert the personalised key into the lock and turn it anticlockwise by 90
°
.
•
Turn the release knob clockwise (fig. 17) as far as it will go. The pinion
will therefore become idle and the gate can then be opened manually.
•
Push the leaf of the gate all the way down to the end-of-stroke.
Warning
: do not push the gate leaf roughly, but move it gently all along
its stroke.
The key can be removed from the lock only after the knob has been
moved back to its initial position (motor-driven operation)
•
To re-activate motor-driven control, turn the knob anticlockwise as far as
it will go. Move the key back to its closing position, remove it and then
store it in a safe place, which is known to anyone who may need the
knob.
15) INSTALLATION CHECK
Before the automation device finally becomes operational, scrupulously
check the following conditions:
• Check that all the safety devices (limit microswitches, photocells, elec-
tric edges etc) operate correctly.
• Check that the rack and pinion are correctly meshed (minimum play 2mm).
• Check that the pushing force of the gate is within the limits provided for
by the current standards.
• Check that the opening and closing end-of-stroke runners are correctly
positioned and tightly secured.
• Check the starting and stopping operations using the manual control.
• Check the starting and stopping operations using the remote radio control.
• Check the normal or customised operation logic.
16) AUTOMATION DEVICE USE
Since the automation device can be controlled both remotely and in sight,
by means of a radio control device or a button, all the safety devices must
be frequently checked in order to ensure their perfect efficiency.
WARNING! In the event of any safety device malfunction, request
immediate assistance from qualified personnel.Children must be kept
at a safe distance from the automation operation area.
17) AUTOMATION CONTROL
The use of this control device allows the gate to be opened and closed
automatically. There are different types of controls (manual, radio control,
magnetic card access etc.) depending on the installation requirements and
characteristics. For the various control systems, see the relevant instruc-
tions.
The installer undertakes to instruct the user about correct automa-
tion operation, also pointing out the actions to be taken in case of
emergency.
18) MAINTENANCE
WARNING! Before proceeding to any maintenance, disconnect the
mains power supply and, if the battery is fitted, one of its poles.
These are the check and maintenance operations to be carried out:
•
Check the condition of lubrication of the metal racks once a year.
•
Keep the sliding track always clean and free from debris.
•
Occasionally clean the photocell optical elements.
•
Have a qualified technician (installer) check the correct torque limit
setting.
•
When any operational malfunction if found, and not resolved, disconnect
the mains power supply and request the assistance of a qualified
technician (installer). When the automation controller is out of service,
you can activate the manual release device (see paragraph on
“
Emergency manoeuvre
”) in order to set the pinion idling and therefore
allow the gate to be opened and closed by hand.
19) NOISE
The environmental noise produced by the gear-motor in normal operation
conditions is constant and does not exceed 70 dB (A).
20) SCRAPPING
Materials must be disposed of in conformity with the current regula-
tions.
Содержание ICARO
Страница 2: ...2 ICARO Ver 03 D811310_03 ...