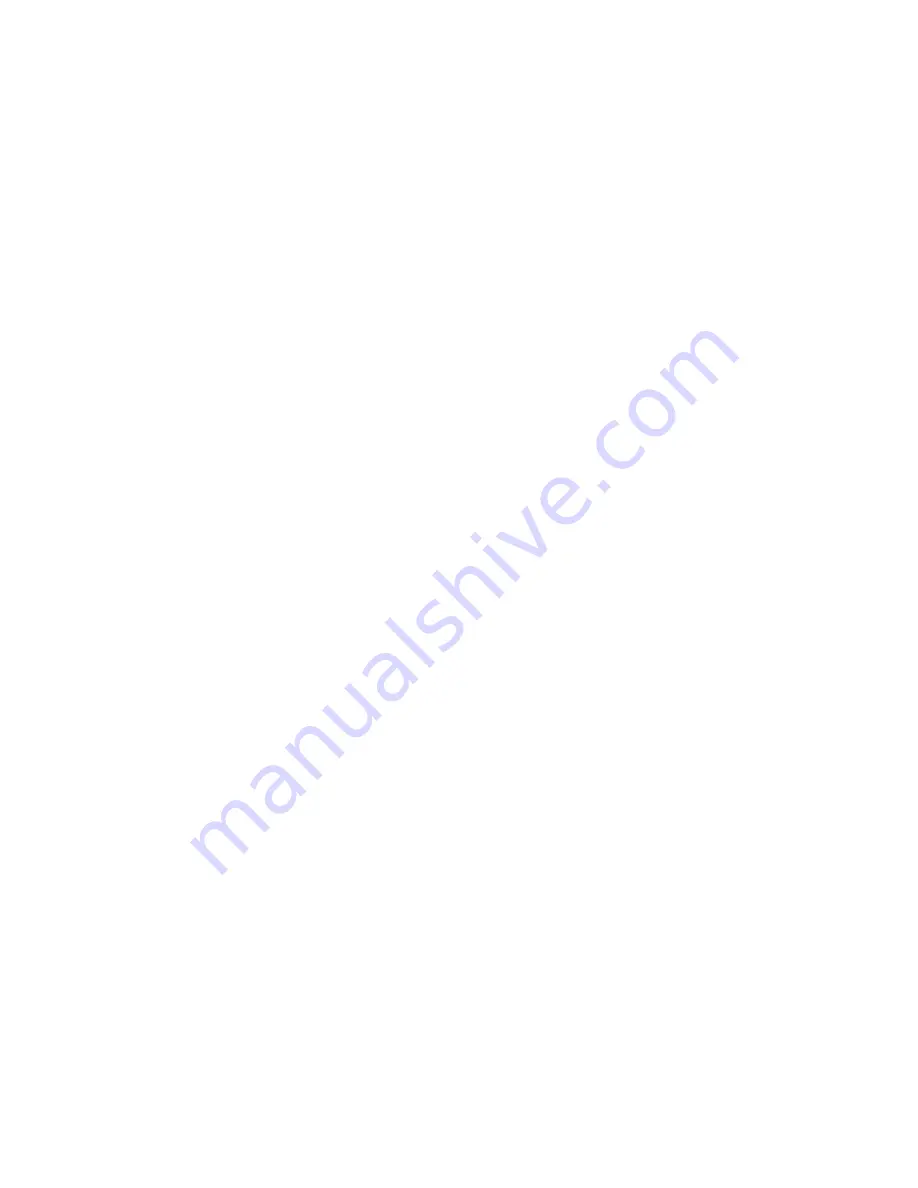
maintenance programme is adopted by the
user.
Quarterly Inspection
(a) Visual inspection of the burner
(b)Clean and check spark
electrode
(c) Clean and check photocell
(d) Check overheat safety is
operational
Bi-Annual Inspection
(a) As per quarterly inspection, plus...
(b) Combustion check
(c) Smoke test
Annual Inspection
(a) As per half year inspection,
plus...
(b) Heat exchanger and cleaning
(c) Electrical connections
(d) Main fan motor
(e) Main fan assembly
(f) Pulleys
(g) Fan belts
(h) Oil supply including filter
(i) Burner
(j) Air delivery system
(k) Flue
(l) Report
5.2 Servicing Procedure - Major
Component Parts
Flue
A visual inspection should be carried out to
ensure that the flue remains adequately
supported, both internally as well as externally,
and that the various joints are effectively
sealed.
Inspection covers, where fitted, should be
removed and the flue checked to see whether
cleaning is required
If inspection covers are not fitted the flue gas
exit duct and flue spigot will provide not only
an indication of the cleanliness of the flue, but
will also enable access for cleaning.
The presence of the flue terminal should be
checked.
If a condensate trap and drain facility is fitted
this should be checked to ensure that it
continues to function correctly, and the
drainage of condensates is not impaired.
Main Fan Motor
Remove access panel. Dust and other foreign
matter should be cleaned by blowing over with
compressed air and through the use of a soft
bristle brush and cloth.
Solvent wipes may be used to remove heavy
soiling from the motor casing.
Traces of surplus lubricants spreading from the
bearings should also be cleaned away.
Where motors are fitted with grease nipples
bearings should be lubricated with the correct
grade of lubricant. Motors which do not have
grease nipples feature sealed bearings which
are lubricated during manufacture for their life.
The electrical connections should be checked
as follows.
The cover to the terminal box should be
removed by undoing the screws which secure
it.
Check connections for signs of corrosion,
tightness, and ensure that there are no stray
strands which could form a short circuit.
Clean, tighten, and replace as necessary.
Replace cover and secure.
Main Fan
Remove dust and other foreign matter by
blowing off with compressed air or through the
use of a soft bristle brush.
Check that the bearings do not show signs of
excessive wear.
It should be noted that these bearings do not
require lubricating.
If the bearings require replacing the following
procedure should be followed.
(a) Remove belt(s).
(b) Loosen set screw on eccentric collar and
tap collar in the opposite direction to fan
rotation.
(c) Remove collar and bearing.
(d) Check shaft for alignment and straightness.
(e) Locate the bearing in its seat and place on
the shaft with the cam facing outwards.
Содержание MH300
Страница 2: ......
Страница 22: ...Wiring Diagram 20 49 146...