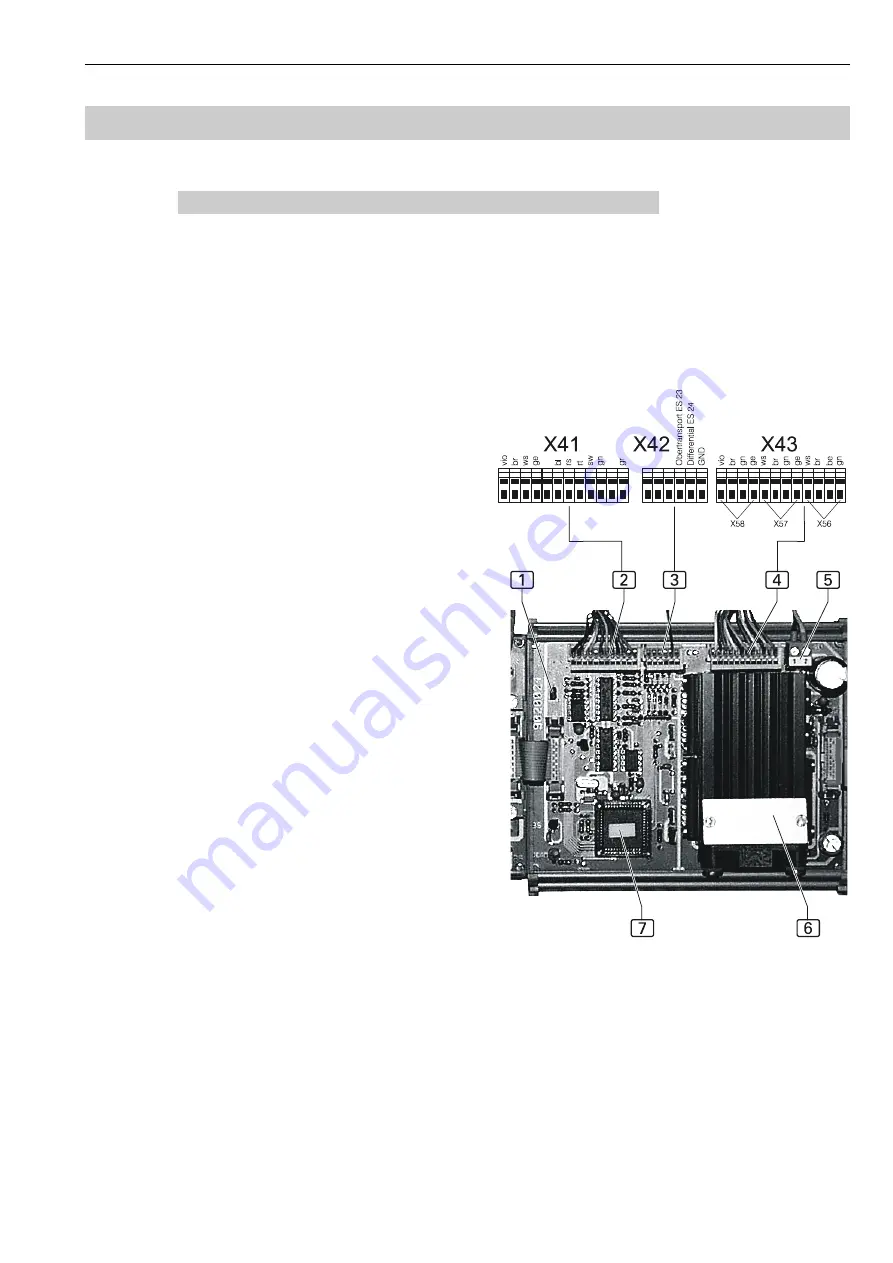
Service Instructions Automatic Single-Head Serging Machine 1265-4
Beisler GmbH
C-23
C.5
Maintenance
C.5.16 Stepper motor PCB with transmission
Fig. 14:
Efka control, initiators, and transport unit are connected to the
terminal strips X11-X13.
1
Sewing machine: Jumper (set)
2
Sewing machine: Efka controller
3
Sewing machine: Initiators
4
Sewing machine: Connection for top transport (X58),
differential transport (X57), puller (X56)
5
Sewing machine: 24 V power supply
6
Sewing machine: Fan
7
Sewing machine: EPROM CRC 0105
Fig. 14