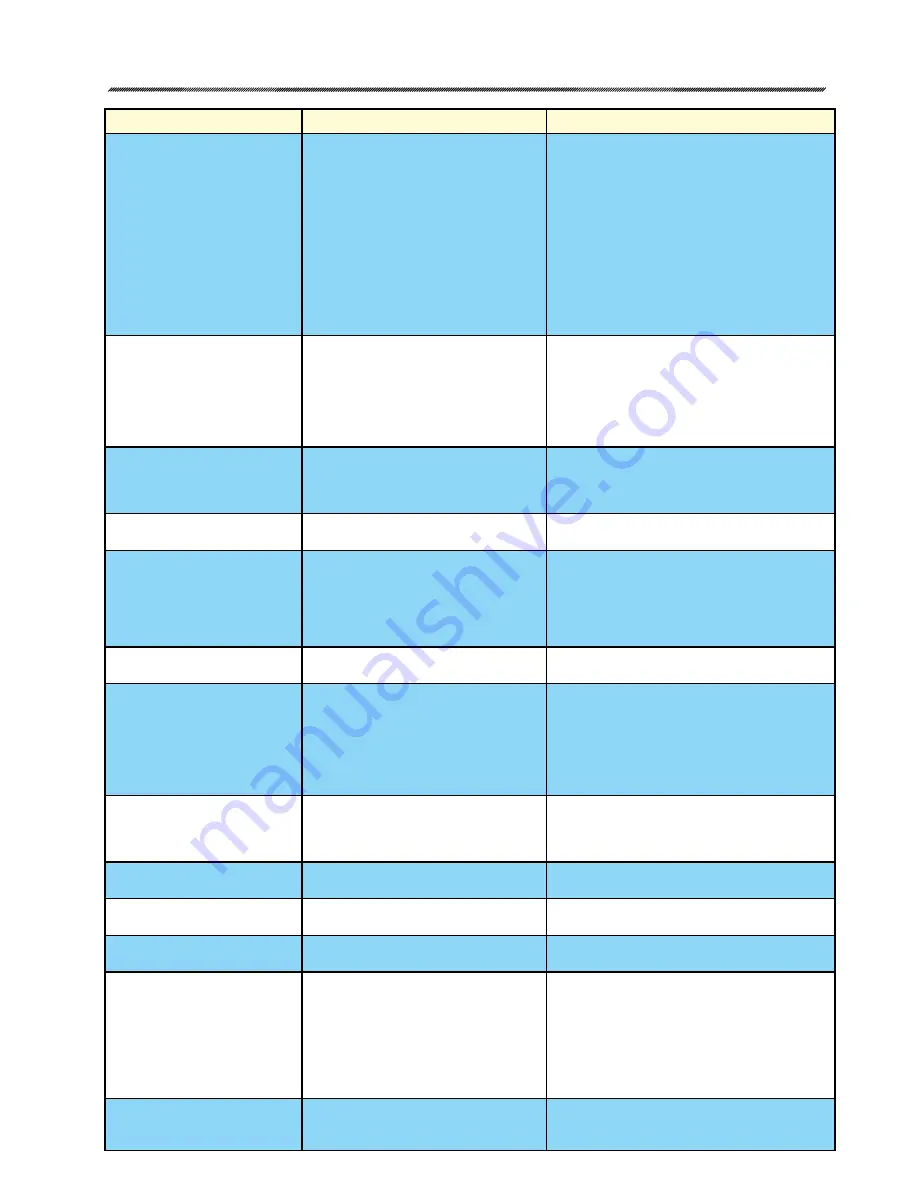
22
80-0042-00, Rev. 06.9
MAINTENANCE
Troubleshooting
CONDITIONS
POSSIBLE CAUSES
CORRECTIONS
Actuator will not run in either
direction with input signal
applied.
a.
b.
c.
d.
e.
f.
g.
Handswitch left in wrong position.
No 120 Vac line supply. No lamps lit
on control board.
Fuse F-1 open. No lamps lit on
control board.
External auto/man switch in wrong
position (Position-all).
Torque on driven load shaft exceeds
actuator torque rating. "S" LED on.
Input signal below range or reversed.
"L" LED on.
Control board failure.
a.
b.
c.
d.
e.
f.
g.
Return Handswitch to auto position.
Check fuses and switches in power panel.
Check for possible shorts, then replace
fuse. Use only Beck part no. 11-1370-10 for
proper protection of triacs.
Return switch to auto position.
Check operation with Handswitch and
remove obstruction.
Input signal voltage between terminal 11 and
12 (+) must be between 1-5 Vdc.
Replace control board.
Actuator runs only in one
direction in auto and both
directions with Handswitch in
forward or reverse.
a.
b.
c.
d.
Zero adjustment incorrect.
Loss of signal feature activated and
actuator set to go to full forward or
reverse position. "L" LED is on.
Loss of feedback signal.
Control board failure.
a.
b.
c.
d.
Readjust Zero. See calibration, p.17.
Check input signal against LOS trigger.
Check feedback signals at terminals 13, 14
or 15.
Replace control board.
Actuator runs in the wrong
direction with input signal
applied.
a.
b.
Input signal reversed. "L" LED on.
Wiring to limit switches reversed.
a.
b.
Check polarity of input signal. Terminal 12 is
positive, 11 negative.
Check limit switch connections. See Limit
Switch adjustment, p.12.
Actuator shaft position
oscillates.
a.
b.
Excessive noise on input signal.
Control board failure.
a.
b.
Check input signal.
Replace control board.
Actuator does not stop at
normal or desired limit of shaft
travel.
a.
b.
c.
d.
Span or Zero adjusted incorrectly.
Limit switches adjusted incorrectly.
Loss of input signal. "L" LED on.
Limit switch failure.
a.
b.
c.
d.
Check control board calibration. See
calibration procedure, p.18.
Readjust limit switches. See limit switch
adjustment, p.12.
Restore input signal to actuator.
Replace limit switch. Contact factory.
Loss of signal feature does not
function.
a.
Control board failure.
a.
Replace control board. See p.19.
Actuator activates to full retract
or extend position and stays.
a.
b.
c.
d.
Handswitch left in forward or reverse
position.
Loss of input signal when LOS go to
position is selected. "L" LED on.
Loss of feedback signal.
Control board failure.
a.
b.
c.
d.
Return forward/reverse Handswitch (S1) to
center STOP position.
Restore input signal to drive.
Check feedback signal at terminals 13, 14
or 15.
Replace control board.
Actuator movement erratic while
driving from full extend to full
retract and runs normally from
full retract to full extend.
a.
b.
Feedback potentiometer dirty. Loss
of wiper contact moves actuator in
reverse direction.
Feedback potentiometer open.
a.
b.
Replace feedback potentiometer.
Replace feedback potentiometer.
Actuator moves uncontrollably
to position, then oscillates.
a.
Feedback potentiometer open.
a.
Replace feedback potentiometer.
Pilot LED light out.
a.
b.
No power.
Control section transformer failure.
a.
b.
Check power sources.
Replace control section transformer.
Feedback signal decreases
when it should increase.
a.
Plug P4 in wrong position on control
board.
a.
Check feedback calibration procedure. See
p.16.
Feedback signal does not
reach maximum, but low end
calibration is correct.
a.
b.
c.
d.
Output overload; load resistance is
too low for voltage range or too high
for current range.
Low voltage.
Feedback pot. not set correctly.
Incorrect actuator feedback
configuration
a.
b.
c.
d.
Check load resistance against suggested
feedback signal terminal hookup.
Check line voltage at terminal board.
Check feedback calibration procedure, p.16.
Check feedback calibration procedure for
correct R2 component on terminal board.
See p.16.
Actuator does not reach desired
travel limit.
a.
Physical obstruction; e.g., valve
jammed or load exeeds actuator
rating. "S" LED on.
a.
Check operation with Handswitch and
remove obstruction.