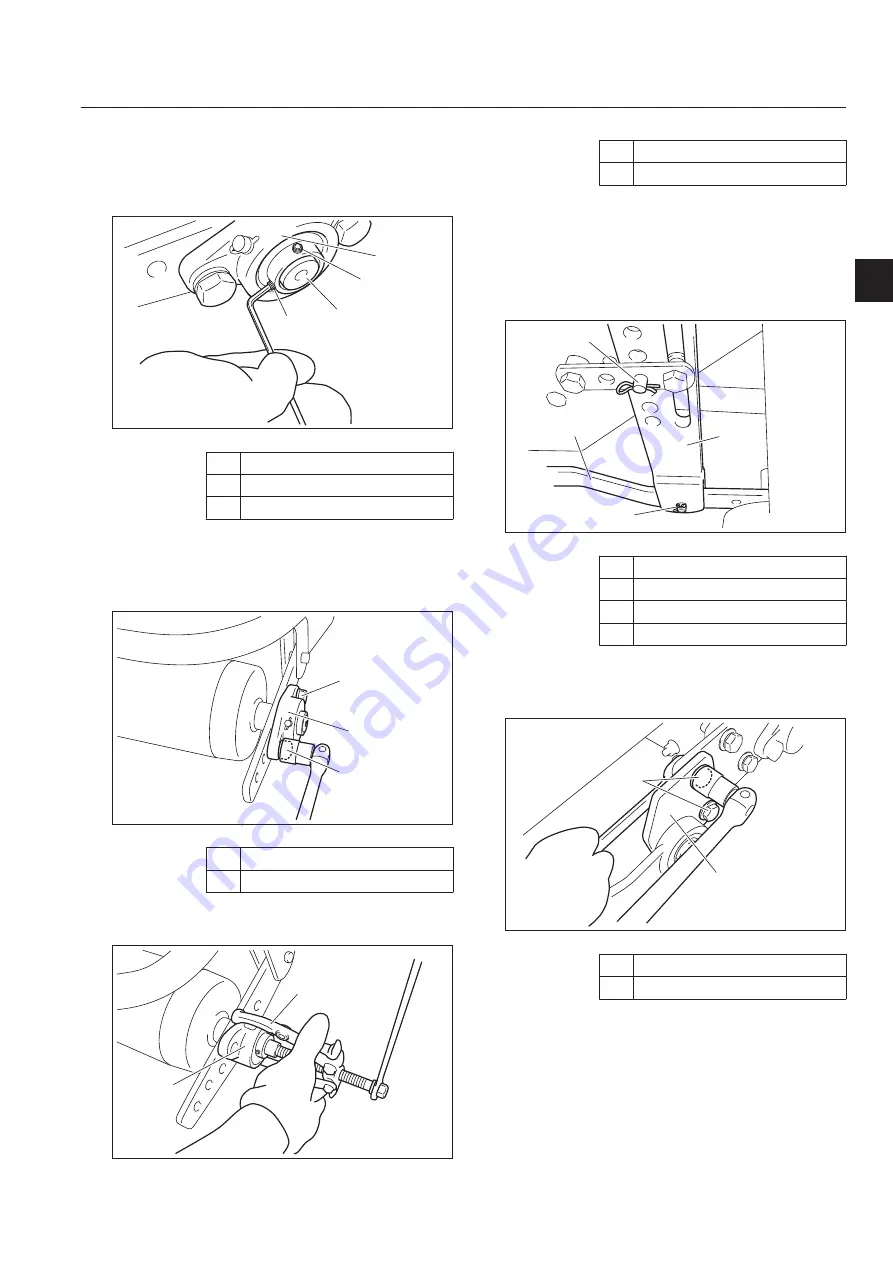
Loosen the hollow set securing the roller
shaft of the flange unit.
Follow the same steps to loosen the one on
the opposite side.
1
2
2
3
oxwlid-003
Removal of rear roller Assy_003
1
Flange unit
2
Hollow set
3
Roller shaft
Remove the bolts and spring washers of
the flange unit.
Follow the same steps to remove those on
the other side.
1
2
2
oxwlid-004
Removal of rear roller Assy_004
1
Flange unit
2
Bolt and spring washer
Remove the flange unit by using a pulley
puller.
1
2
oxwlid-005
Removal of rear roller Assy_005
3.
4.
5.
1
Pulley puller
2
Flange unit
Remove snap pin A and the flat-head pin
securing the rear roller bracket (R).
Remove snap pin B and the flat-head pin
securing the roller mounting strap, lift the
strap to the top, and then secure it with
snap pin B and the flat-head pin.
1
2
3
4
oxwlid-006
Removal of rear roller Assy_006
1
Snap pin A and flat-head pin
2
Snap pin B and flat-head pin
3
Rear roller bracket (R)
4
Roller hanging strap
Remove the bolt, washer, and U nut from
the front roller bracket and then the bracket
mounting board.
2
1
oxwlid-007
Removal of rear roller Assy_007
1
Bolt, washer, and U nut
2
Bracket mounting board
6.
7.
8.
Operating Machine and Mower Units
TDA1200
・
TDA1600
Operating Machine and Mower Units
Page 4-21
Removal and installation of each section
Содержание TDA1200
Страница 1: ...Tractor Mounted Aerator Service Manual Serial No TDA1200 20004 TDA1600 20004 Ver 1 1...
Страница 4: ...TDA1200 TDA1600 Contents...
Страница 10: ...TDA1200 TDA1600 Safety Page 1 6 Safety Signs and Instruction Signs...
Страница 11: ...Waste Disposal Page 2 2 About the Waste disposal Page 2 2 Disposal TDA1200 TDA1600 Disposal Page 2 1...
Страница 22: ...TDA1200 TDA1600 Maintenance standards and maintenance Page 3 10 Greasing...