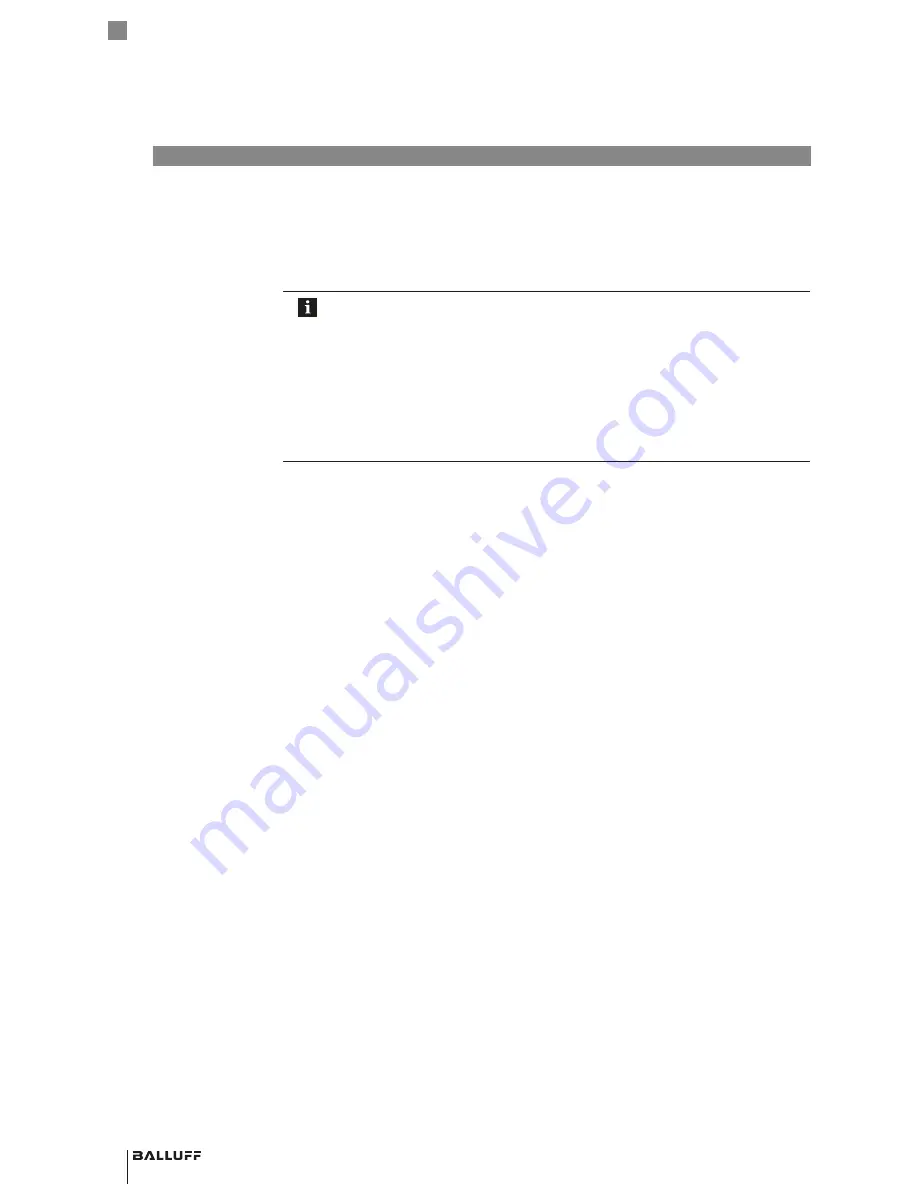
BIS V-6111 CC-Link
Processor unit
14
english
The BIS V-6111 processor unit and the controlling system communicate via CC-Link.
The CC-Link system consists of the following components:
– Bus master
– Bus modules/slaves (here, the BIS V-6111 processor unit)
Important note for implementation using PLCs
There are controllers where the CC-Link data range is not transmitted synchronously
with the update of the input/output map. If more than 2 bytes of data are transmitted,
a mechanism must be used that guarantees that the data in the PLC and the data in
the BIS V is always the same!
Synchronous data transmission as a setting on the master
In this method, the bus master ensures that all of the data necessary for the respec-
tive slave is transmitted together. Usually a special software function must be used in
the PLC that also controls the access between the PLC and bus master so that all
data is always transmitted together.
In order to configure the parameters for the bus master correctly based on type, the device
master data for the BIS V-6111 processor unit are included in the form of a CSP+ file. The CSP+
file can be found in the processor unit's internal memory and can be retrieved from there via the
USB interface.
Each device on a CC-Link line section must have a unique station address. Therefore, before
being used on the bus for the first time, it must be configured individually using the display or
using the CC-Link tool.
BIS V-6111 implements a CC-Link Remote Device Station. Depending on the project configura-
tion, the protocol used is compatible with CC-Link 1.0/1.1 or CC-Link 2.0.
CC-Link divides the cyclical process data buffer into words (16-bit, WW for output data and WR
for input data) and into points (1 bit, referred to in the CC-Link specification as RY for output data
and RX for input data). The number of points and words depends on how many station addres-
ses the device occupies. Between 1 and 4 station addresses are allowed. In addition, CC-Link
2.0 or higher allows you to use more words and points by using the extended cycles function. In
doing so, the process data size can be two, four or eight times as large as when using CC-Link
1.0 or 1.1.
Only words are used for the process data of the read/write heads. The IO-Link port likewise uses
words to transmit the IO-Link data in IO-Link operation. However, points are used for transmit-
ting acyclical IO-Link data and for status data.
As a word is assigned to a head or to the IO-Link port either entirely or not at all, the size of the
process data buffer is always an even number in bytes. Zero is used as the size for a head in
order to disable the corresponding head. The size zero for IO-Link switches off the IO-Link port.
The size of the process data buffer for each head and for the IO-Link port is identical for input
and output data.
6.1 CC-Link
Device data
Station address
Process data
6
Startup
Содержание BIS V-6111 series
Страница 1: ...BIS V 6111 CC Link Technical Description User s Guide english...
Страница 2: ...www balluff com...