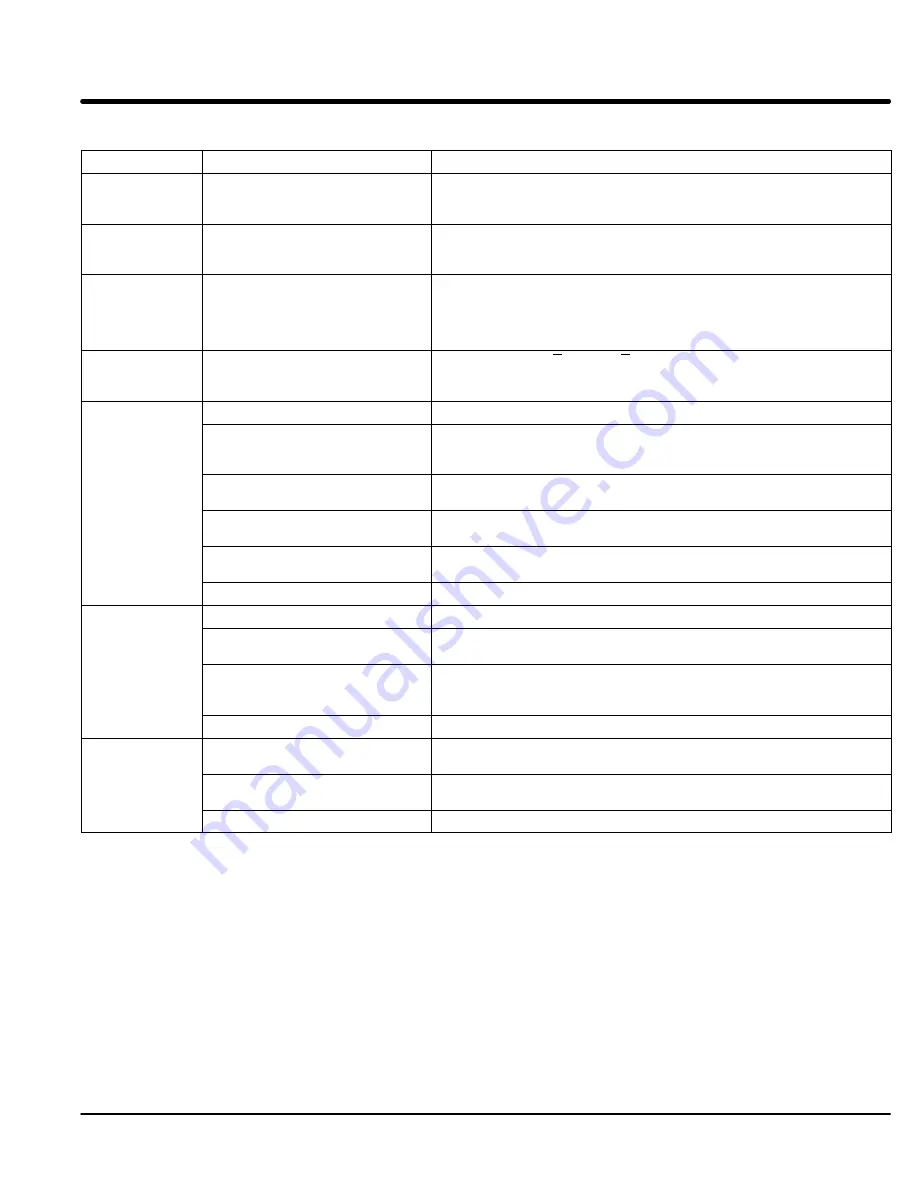
Section 1
General Information
Troubleshooting 5-7
MN718
Table 5-2 Troubleshooting
Continued
INDICATION
POSSIBLE CAUSE
CORRECTIVE ACTION
Motor has wrong
response to
Speed Command
Analog input common mode voltage
may be excessive.
Connect control input source common to control common to minimize
common mode voltage. Maximum common mode voltage at terminals
J1-4 and J1-5 is
±
15VDC referenced to chassis common.
Motor Shaft
Oscillates back
and forth
Incorrect encoder alignment
direction.
Change the Feedback Align parameter in the Level 1 Vector Control block.
If it is Reverse, change it to Forward. If it is Forward, change it to Reverse.
Motor Shaft
rotates at low
speed regardless
of commanded
speed
Incorrect encoder alignment
direction.
Check encoder connections.
Change the Feedback Align parameter in the Level 1 Vector Control block.
If it is Reverse, change it to Forward. If it is Forward, change it to Reverse.
Motor Shaft
rotates in wrong
direction
Incorrect encoder wiring.
Reverse the A and A or B and B encoder wires at the J1 input to control
and change encoder direction in the Feedback Align parameter in the
Level 1 Vector Control block.
Motor Will Not
Start
Not enough starting torque.
Increase Current Limit setting.
Start
Motor overloaded.
Check for proper motor loading.
Check couplings for binding.
Verify proper sizing of control and motor.
Control not in local mode of
operation.
Place control in local mode.
Motor may be commanded to run
below minimum frequency setting.
Increase speed command or lower minimum frequency setting.
Incorrect Command Select
parameter.
Change Command Select parameter to match wiring at J1.
Incorrect speed command.
Verify control is receiving proper command signal at J1.
Motor Will Not
Reach Maximum
Max Output Speed set too low.
Adjust MAX Output Speed parameter value.
Reach Maximum
Speed
Motor overloaded.
Check for mechanical overload. If unloaded motor shaft does not rotate
freely, check motor bearings.
Improper speed command.
Verify control is set to proper operating mode to receive speed command.
Verify control is receiving proper command signal at input terminals.
Check velocity loop gains.
Speed potentiometer failure.
Replace potentiometer.
Motor Will Not
Stop Rotation
MIN Output Speed parameter set
too high.
Adjust MIN Output Speed parameter value.
Improper speed command.
Verify control is receiving proper command signal at input terminals.
Verify control is set to receive speed command.
Speed potentiometer failure.
Replace potentiometer.
Содержание 18H Series
Страница 1: ...SERIES 18H AC Flux Vector Control Installation Operating Manual 9 97 MN718 VECTOR DRIVE ...
Страница 105: ...Section 1 General Information 5 18 Troubleshooting MN718 ...
Страница 109: ...Section 1 General Information 6 4 Manual Tuning the Series 18H Control MN718 ...
Страница 144: ...Appendix C Appendix C 1 MN718 ...