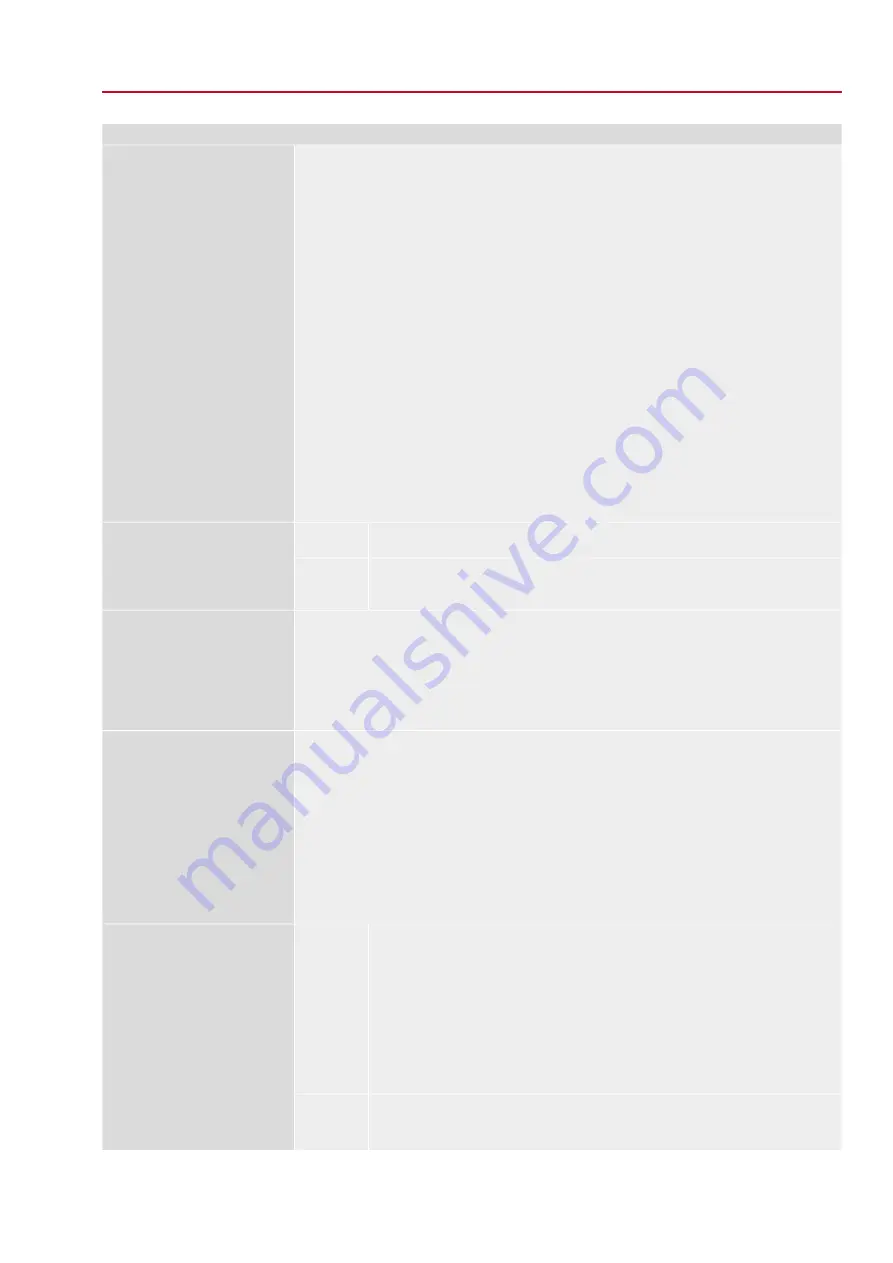
Features and functions
Additional, binary output signals (only available in combination with additional input signals (option)
●
6 programmable output contacts:
-
5 potential-free NO contacts with one common, max. 250 V AC, 1 A (resistive load)
Default configuration: End position CLOSED, end position OPEN, selector switch REMOTE,
torque fault CLOSE, torque fault OPEN
-
1 potential-free change-over contact, max. 250 V AC, 5 A (resistive load)
Default configuration: Collective fault signal (torque fault, phase failure, motor protection tripped)
●
6 programmable output contacts:
-
5 potential-free change-over contacts with one common, max. 250 V AC, 1 A (resistive load)
-
1 potential-free change-over contact, max. 250 V AC, 5 A (resistive load)
●
6 programmable output contacts:
-
6 potential-free change-over contacts without one common, max. 250 V AC, 5 A (resistive load)
●
6 programmable output contacts:
-
4 mains failure proof potential-free NO contacts with one common, max. 250 V AC, 1 A (resistive
load), 1 potential-free NO contact, max. 250 V AC, 1 A (resistive load), 1 potential-free change-
over contact, max. 250 V AC, 5 A (resistive load)
●
6 programmable output contacts:
-
4 mains failure proof potential-free NO contacts, max. 250 V AC, 5 A (resistive load), 2 potential-
free change-over contacts, max. 250 V AC, 5 A (resistive load),
All binary output signals must be supplied with the same potential.
●
Analogue output signal for position feedback
-
Galvanically isolated position feedback 0/4 – 20 mA (load max. 500
Ω
)
Fieldbus interface with additional
output signals (option)
Auxiliary voltage 24 V DC: max. 100 mA for supply of control inputs, galvanically isolated
from internal voltage supply.
Standard:
Voltage output
Auxiliary voltage 115 V AC: max. 30 mA for supply of control inputs, galvanically isolated
from internal voltage supply
(Not possible in combination with PTC tripping device)
Option:
Redundant line topology with universal redundancy behaviour according to AUMA redundancy I or II
Redundant loop topology in combination with SIMA Master Station
●
Max. number of actuators with actuator controls per redundant loop: 247 units
●
Max. possible cable length between the actuators equipped with actuator controls without external
repeater: 1,200 m
●
Max. possible total length per redundant ring: approx. 290 km
●
Automatic commissioning of the redundant ring by means of the SIMA Master Station
Redundancy (option)
●
Connector types: ST or SC connector
●
FO cables
-
Multi-mode: 62,5(50)/125 µm, range approx. 2.5 km (max. 2.0 dB/km)
-
Single-mode: 9/125 µm, range approx. 15 km (max. 0.4 dB/km)
●
Topologies: Line, star and redundant ring (with single-channel Modbus RTU interface)
●
Baud rate: up to 115.2 kbit/s
●
Optical budget:
-
Multi-mode: 13 dB
-
Single-mode: 17 dB
●
Wave length: 1,310 mm
●
FO coupler by EKS required at DCS, reference addresses: AUMA or www.eks-engel.com
FO cable connection (option)
●
Selector switch: LOCAL - OFF - REMOTE (lockable in all three positions)
●
Push buttons OPEN, STOP, CLOSE, RESET
-
Local STOP
The actuator can be stopped via push button STOP of local controls if the selector
switch is in position REMOTE. (Not activated when leaving the factory.)
●
6 indication lights:
-
End position and running indication CLOSED (yellow), torque fault CLOSE (red),
motor protection tripped (red), torque fault OPEN (red), end position and running
indication OPEN (green), Bluetooth (blue)
●
Graphic LC display: illuminated
Standard:
Local controls
●
Special colours for the indication lights:
-
End position CLOSED (green), torque fault CLOSE (blue), torque fault OPEN
(yellow), motor protection tripped (violet), end position OPEN (red)
Option:
79
SQ 05.2 – SQ 14.2 / SQR 05.2 – SQR 14.2 Control unit - electromechanical
AC 01.2 Intrusive Modbus RTU
Technical data