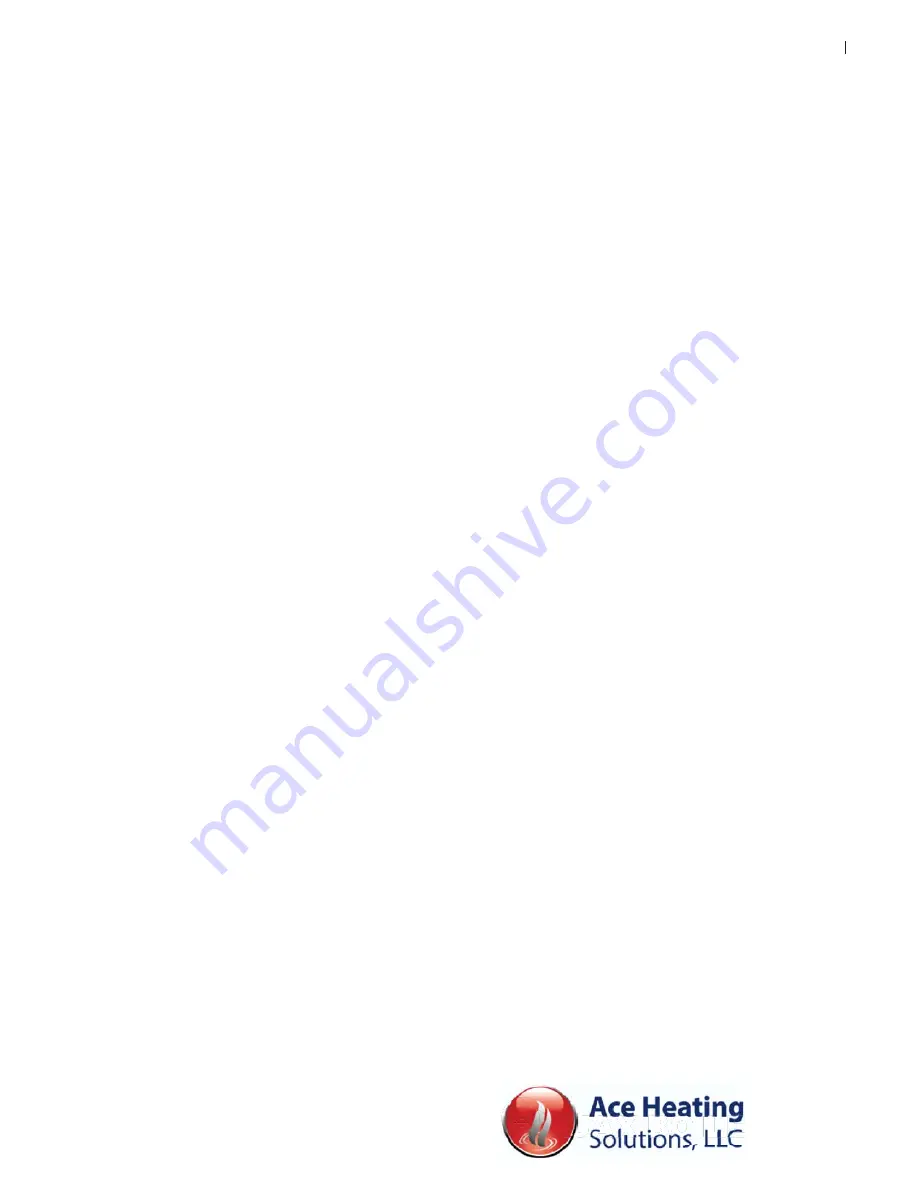
F 45
G. WARRANTY
Ajax Boiler Inc. (ABI), warrants to the original owner and
at the original installation site subject to the terms and
conditions herein that all products manufactured by ABI
(“Products”) comply, at the time of manufacture, with recog-
nized hydronics industry regulatory agency standards and
requirements then in effect and will be free from defects in
materials and workmanship for a period of 12 years from
date of shipment. (the “Warranty Period”). The burner is
also covered under the limited warranty for 5 years from
date of shipment (the “Warranty” Period). For products or
parts not manufactured by ABI, the warranty obligations of
ABI shall, in all respects, be limited to 2 years.
I. REMEDY
A. Should an Atlas Triton Series™ Boiler fail due to de-
fects in materials or workmanship within the Warranty
Period, ABI will repair or replace, at ABI’s sole discre-
tion, any part found to be defective under conditions
of normal use. Labor, transportation, or other expens-
es for removal and/or installation are not included.
B. Warranty - The owner must notify the original Installer
of the Product and ABI in writing, within the Warranty
Period, providing a detailed description of all claimed
defects. Transportation to a factory or other designat-
ed facility for repairs of any products or items alleged
defective shall, in all events, be the responsibility and
at the cost of the owner.
II. EXCLUSIONS
ABI shall have no liability for and this warranty does not
cover:
A. Incidental, special or consequential damages, such
as loss of the use of products, facilities or production,
inconvenience, loss of time or labor expense involved
in repairing or replacing the alleged defective Prod-
uct.
B. The performance of any Product under conditions
varying materially from those under which such Prod-
uct is usually tested under industry standards as of
the time of shipment.
C. Any damage to the Product due to abrasion, erosion,
corrosion, deterioration, abnormal temperatures or
the inuence of foreign matter or energy.
D. The design or operation of owner’s plant or equip-
ment or of any facility or system of which any Product
may be made a part.
E. The suitability of any Product for any particular ap-
plication.
F. Any failure resulting from misuse, modication not
authorized by ABI in writing, improper installation or
lack of, or improper maintenance.
G. Equipment furnished by the owner, either mounted or
unmounted, or when contracted for by the owner to
be installed or handled.
H. Leakage or other malfunction caused by:
1. Defective installations in general and specically,
any installation which is made:
a. in violation of applicable state or local plumb-
ing housing or building codes;
b. without a certied ASME, pressure relief
valve, or;
c. contrary to the written instructions furnished
with the unit.
2. Adverse local conditions in general and, speci
cally, sediment or lime precipitation in the tubes
and/or headers or corrosive elements in the
atmosphere.
3. Misuse in general and, speci cally, operation
and maintenance contrary to the written instruc-
tions furnished with the unit, disconnection,
alteration or addition of components or appara-
tus, not approved by seller, operation with fuels
or settings other than those set forth on the rating
plate or accidental or exterior damage.
I.
Production of noise, odors, discoloration or rusty
water.
J. Damage to surrounding area or property caused by
leakage or malfunction. Costs associated with the
replacement and/or repair of the unit including: any
freight, shipping or delivery charges, any removal,
installation or reinstallation charges, any material
and/or permits required for installation, reinstallation
or repair, charges to return the boiler and or compo-
nents.
Seller’s liability under this warranty shall not in any case
exceed the amount paid for the Product found to be defec-
tive.
III. THIRD-PARTY WARRANTIES
For goods or components not manufactured by Seller,
the warranty obligations of Seller shall, in all respects,
conform and be limited to one year from the date of
shipment.
IV. SEVERABILITY
To the extent that any provision of this warranty would
be void or prohibited under applicable law, such provi-
sions shall be limited in effect to the minimum extent
necessary to render the remaining provisions hereof
enforceable.
V.
“Quality, value and service since 1919”
LIMITED WARRANTY
Ace Heating Solutions, LLC (AHS), warrants to the original
owner and at the original installation site subject to the
terms and conditions herein that all products manufactured
by AHS (“Products”) comply, at the time of manufacture,
with recognized hydronics industry regulatory agency
standards and requirements then in effect and will be free
from defects in materials and workmanship for a period of
12 years from date of shipment. (the “Warranty Period”).
The burner is also covered under the limited warranty for 5
years from date of shipment (the “Warranty” Period). For
products or parts not manufactured by ABI, the warranty
obligations of AHS shall, in all respects, be limited to 2
years.
A. Should an Atlas Triton Series™ Boiler fail due to
defects in materials or workmanship within the Warranty
Period, AHS will repair or replace, at AHS’s sole
discretion, any part found to be defective under
conditions of normal use. Labor, transportation, or other
expenses for removal and/or installation are not included.
B. Warranty - The owner must notify the original Installer
of the Product and AHS in writing, within the Warranty
Period, providing a detailed description of all claimed
defects. Transportation to a factory or other designated
facility for repairs of any products or items alleged
defective shall, in all events, be the responsibility and
at the cost of the owner.
AHS shall have no liability for and this warranty does not
cover:
A. Incidental, special or consequential damages, such
as loss of the use of products, facilities or production,
inconvenience, loss of time or labor expense involved
in repairing or replacing the alleged defective Product.
B. The performance of any Product under conditions
varying materially from those under which such Product
is usually tested under industry standards as of
the time of shipment.
C. Any damage to the Product due to abrasion, erosion,
corrosion, deterioration, abnormal temperatures or
the influence of foreign matter or energy.
D. The design or operation of owner’s plant or equipment
or of any facility or system of which any Product
may be made a part.
E. The suitability of any Product for any particular
application.
F. Any failure resulting from misuse, modification not
authorized by AHS in writing, improper installation or
lack of, or improper maintenance
“
“
“Q
Q
“Qu
Q
Q
Q
Q
Q
Q
Q
ali
l
l
li
ali
t
t
ty, va
lu
l
l
lue
lu
ue
a
a
a
Содержание Triton T-80
Страница 31: ...E 29 E 3 ELECTICAL WIRING DIAGRAM ...
Страница 43: ...F 41 ...
Страница 44: ...F 42 ...
Страница 45: ...F 43 ...
Страница 46: ...F 44 Notes ...