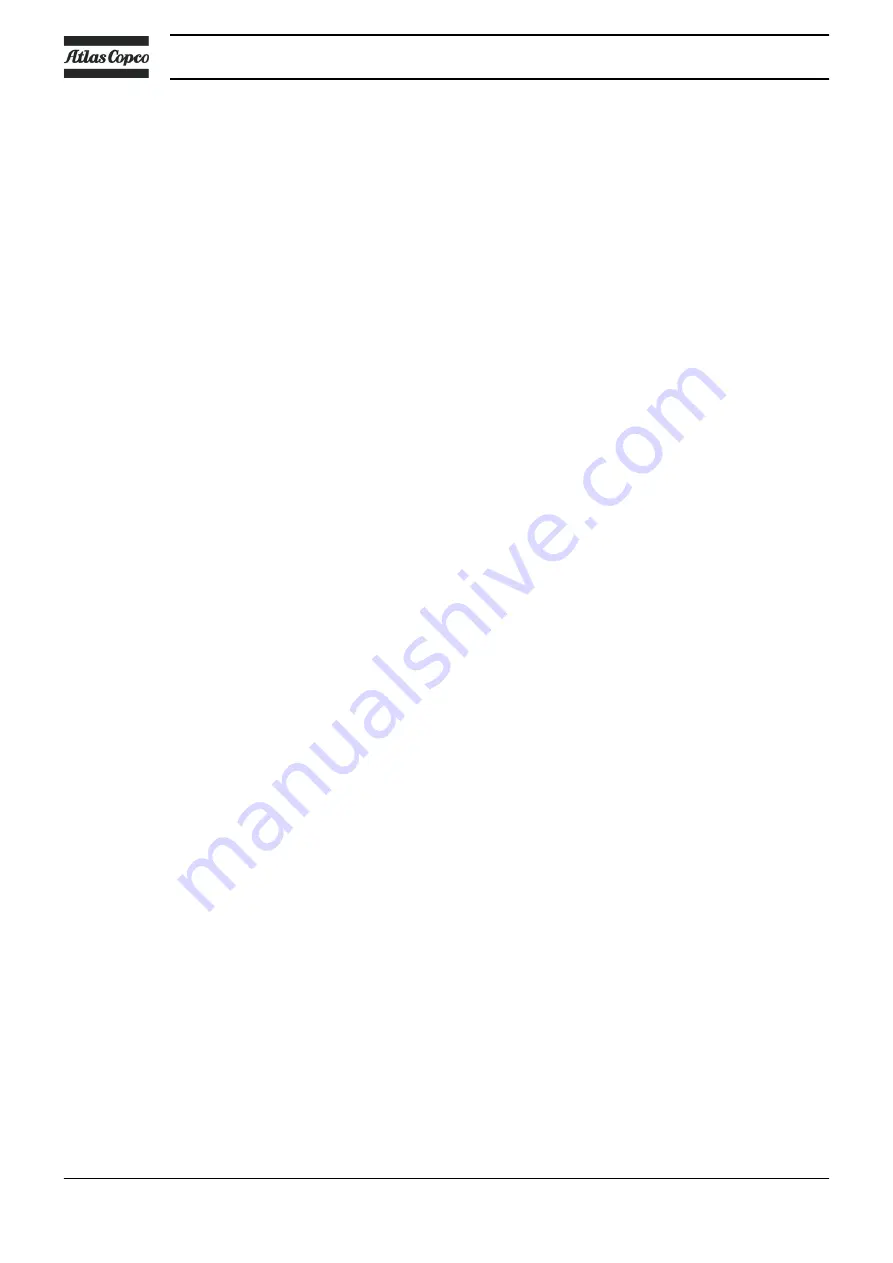
Roto Synthetic Fluid ULTRA
Roto Synthetic Fluid ULTRA is a synthetic oil based 4000 hours lubricant, specially developed for
use in single stage oil injected screw compressors running in demanding conditions. Roto
Synthetic Fluid ULTRA can be used for compressors operating at ambient temperatures between
0 ˚C (32 ˚F) and 45 ˚C (113 ˚F). For more extreme conditions, or when longer oil life is required, it
is recommended to use Roto Synthetic Fluid XTEND DUTY.
Roto Synthetic Fluid XTEND DUTY
Atlas Copco's Roto Synthetic Fluid XTEND DUTY is a high quality synthetic 8000 hours lubricant
for oil injected screw compressors which keeps the compressor in excellent condition. Because
of its excellent oxidation stability, Roto Synthetic Fluid XTEND DUTY can be used for
compressors operating at ambient temperatures between 0 ˚C (32 ˚F) and 46 ˚C (115 ˚F). Roto
Synthetic Fluid XTEND DUTY is the standard lubricant for oil injected screw compressors
equipped with freeze protection or Energy Recovery.
If the compressor is regularly operating in ambient temperatures above 40 °C (104 °F), oil lifetime
is reduced (see table oil lifetime
Preventive maintenance schedule
).
Roto-Foodgrade Fluid
Special oil, delivered as an option.
Atlas Copco's Roto-Foodgrade Fluid is a unique high quality synthetic lubricant, specially created
for oil injected screw compressors that provide air for the food industry. This lubricant keeps the
compressor in excellent condition. Roto-Foodgrade Fluid can be used for compressors operating
at ambient temperatures between 0 ˚C (32 ˚F) and 40 ˚C (104 ˚F).
Roto-Foodgrade Fluid has all required certification for use in food & beverage industry: like
NSFH1, Kosher, Halal and Allergen Free approvals.
If the compressor is regularly operating in ambient temperatures above 35 °C (95 °F), oil lifetime
is reduced (see table oil lifetime
Preventive maintenance schedule
).
8.3
Drive motor
Bearing maintenance
The motor bearing is lubricated by oil injection. Re-greasing is not necessary.
Instruction book
114
2920 7118 31
Содержание GA 11+
Страница 1: ...INSTRUCTION BOOK OIL INJECTED ROTARY SCREW COMPRESSORS GA 11 GA 15 GA 18 GA 22 GA 26 GA 30 ...
Страница 2: ......
Страница 44: ... BOOT Software nr Instruction book 42 2920 7118 31 ...
Страница 81: ...5 4 Pictographs Description Pictographs 1 2 3 4 5 6 7 8 9 10 11 12 13 14 Instruction book 2920 7118 31 79 ...
Страница 99: ...Prefilter components Reference Name 1 4 Prefilter Instruction book 2920 7118 31 97 ...
Страница 109: ...7 6 Stopping Control panel Elektronikon Touch Control panel Elektronikon Swipe Instruction book 2920 7118 31 107 ...
Страница 151: ......