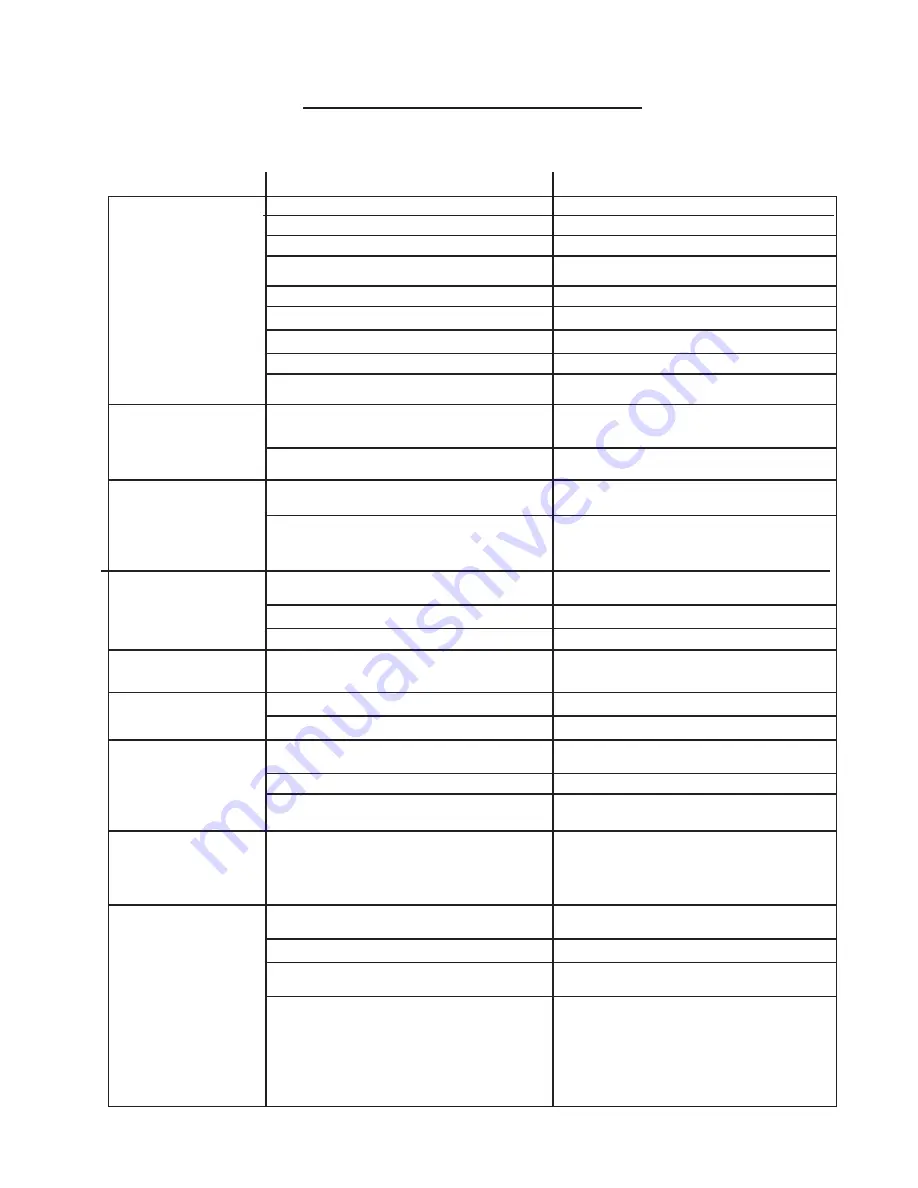
31
P r o b l e m
Typical Solution
TROUBLESHOOTING
1)
Insufficient Purifier
Production.
Issue / Message Displayed
2)
Scale Buildup
within the Cell.
Retest with new Reagents or Strips.
k
Increase your pump run time.
Increase the Purifier % output.
If the output is 100% then “Cell Power” may be inadequate.
Purifier loss due to intense sunlight.
The body of water being purified leaks.
The bather load has increased.
The circulation run time is insufficient.
The DIG-220 is set too low in relation to purifier demand.
The test kit reagents or test strips are old or expired.
Follow the INSTALLER SETUP instructions, see page 23.
Check the residual salt level and adjust as needed.
Increase the Purifier % output or add a Non-Chlorine Shoc
containing Potassium
Monopersulfate
to supplement.
.
Repair the leak and rebalance as needed.
“Cell Type” selection not matched to the cell installed.
Low Salt.
Check your stabilizer level and adjust if needed.
Follow programming directions on page 23 to increase the power
level.
The water being purified contains high pH, total alkalinity and calcium
hardness levels. (Cell scales within 2 – 3 weeks)
Contact the factory for Warranty Status/Procedures.
3)
DC Plug and Cell
Terminals Burned.
Power Supply not reversing polarity.
(Cell constantly scales within 3 – 5 days)
Calculate Saturation Index to assure balanced water. Adjust
chemicals and clean the cell. See page-24 & 25 and page-28 &
29.
4)
Premature Cell
Failure (Requires
Replacement Cell).
The Cell terminals are wet due to an incorrectly oriented (upside
down) cell, failure to dry terminals, or leaking cell body.
Make sure cell is installed correctly. See page- 29. Contact the
factory for Warranty Status/Procedures.
The Cell plug is not securely pushed onto the cell terminals,causing
electrical arcing in the cell cord terminals.
Abnormally high Cell usage due to an insufficient Stabilizer (Cyanuric
acid) level.
5)
White Flakes in the
Water.
This occurs when excessive calcium hardness is present. Usually
due to waterchemistry imbalance
Adjust your water chemistry, visually inspect Cell for scale buildup
and if necessary clean the cell as describ
ed on
page-29.
6)
No Power to the
Control Box.
Check the stabilizer level and adjust to recommended levels.
“Cell Type” selection not matched to the Cell installed.
Excessive Scale/Debris in the Cell.
Follow the INSTALLER SETUP instructions, see page-29.
See Section 2 above.
Circuit Breaker tripped.
Check the power going to the Control Box. Reset the Circuit Breaker.
7)
CHECK SYSTEM
Light Flashing.
Message Displayed
“PURIFIER OFF - CHECK
FLOW” (No purifier
generation during this
display)
Check and replace fuse. See page-27.
Internal Power Fuse blown.
Insufficient Flow (Min 15 gpm) (3.4 m³/hr)
Ensure your Filter and Cell are clean of debris. Check all valves
that might divert flow away from the cell.
Contact the factory for Warranty Status/Procedures.
Tri-
s
ensor Defective.
Contact the factory for Warranty Status/Procedures.
Tri-
s
ensor Cord Defective.
Ensure the Cell cord plug is pressed completely onto the Cell
terminal. Check the terminals and clean with a dry cloth to remove
all dirt and corrosion. If the cell cord is corroded or burned then
it must be replaced to prevent damage to the cell.
8)
CHECK SYSTEM
Light Flashing.
Extremely Low Cell Amperage. Select “Test Pool Pilot” menu and
note cell volts and amps.
Same as LOW SALT message below.
Message Displayed
“LOW AMPS – CELL”
(Purifier still producing)
9)
CHECK SYSTEM
Light Flashing.
Message Displayed
“CHECK/CLEAN CELL”
(Purifier still producing)
Low Cell Amperage.
Cell heavily scaled. If cell is already clean, replace
cell.
Power Supply has failed.
The Cell Cord is Loose.
Pool has low salt and the unit needs salt calibration.
Contact the factory for Warranty Status/Procedures.
Ensure that the cord is firmly pressed into the cell and the wires
properly connected into the banana plugs.
Add salt to pool, recalibrate salt sensor.
Continued Next Page...