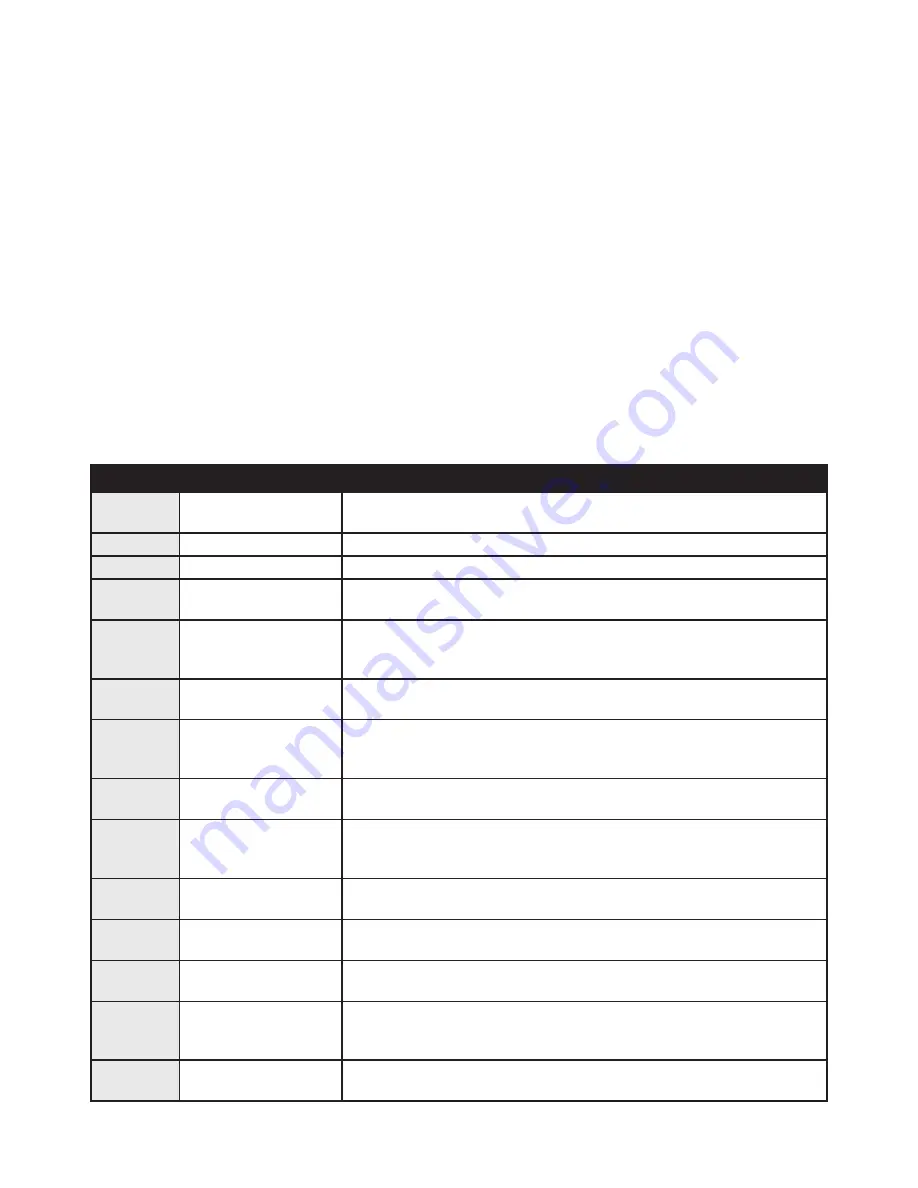
August 2012
L010796
41
Problem:
The DPE25611 controller has a fault condition.
Possible Solutions:
1. Verify your program for improper syntax that may cause an error code.
2. Physically press the reset button on the DPE25611 to clear an error.
3. Another way to clear an error is by using either the SMC60WIN software or the direct
mode command instructions set.
4. The SMCWIN can clear an error in the real time motion tab section by clicking on the
verify parameters button.
5. The direct mode command “!” can clear an error by simply prompting the error code
register to return the value back to the PC or PLC.
Note: Read the Error returned to the screen to better understand what can be causing
the fault condition. The error is return in binary coded decimal format. If two errors were
received, their binary values would be added together.
Error Code
Type
Description
1
Receive Overflow
Error
The serial communications had a receiving error. This is an internal
error caused by the computer.
2
Encoder Error 1
The encoder needed to correct the index.
4
Encoder Error 2
The encoder could not finish the index. Output 8 is set with this error.
8
Command Error
A bad command was sent to the controller. Please check to see that
the command being sent is valid.
16
Motor Error
Motor speed profiles are set incorrectly. Please make sure that the
base speed is less than the max speed and that the speeds are within
their valid ranges.
32
Range Overflow Error The go to position has an overflow error. This is caused by the P com
-
mand trying to find a position that is out of its range.
64
Range Error
There was an invalid number of commands and characters sent to the
controller. Check to see if the parameters are invalid for the command
that was sent.
128
Transmit Error
To many parameters sent back to the PC. This is an internal error
caused by the EEProm.
256
Mode Error
Controller is in a wrong mode. Some commands are good only in pro-
gramming mode, while others are good only in direct mode. Check the
direct mode section to see which commands are good in direct mode.
512
Zero Parameters Error There were no parameters sent to the controller. A command was sent
to the controller that expected to see parameters after the command.
1024
Busy Error
The controller is busy indexing. The controller is sending out clocks to
the driver and can not execute the next instruction.
2048
Memory Range Error
The specified address is out of range. This is caused by overflowing
the program memory by having a program that is to large.
4096
Memory Command
Error
The command pulled from memory is invalid. The command that was
stored into the EEProm was non-executable by the program. This is
an internal error.
8192
Thumbwheel Read
Error
There was an error reading the thumbwheel or the thumbwheel is not
present.
Error Codes
July 2018