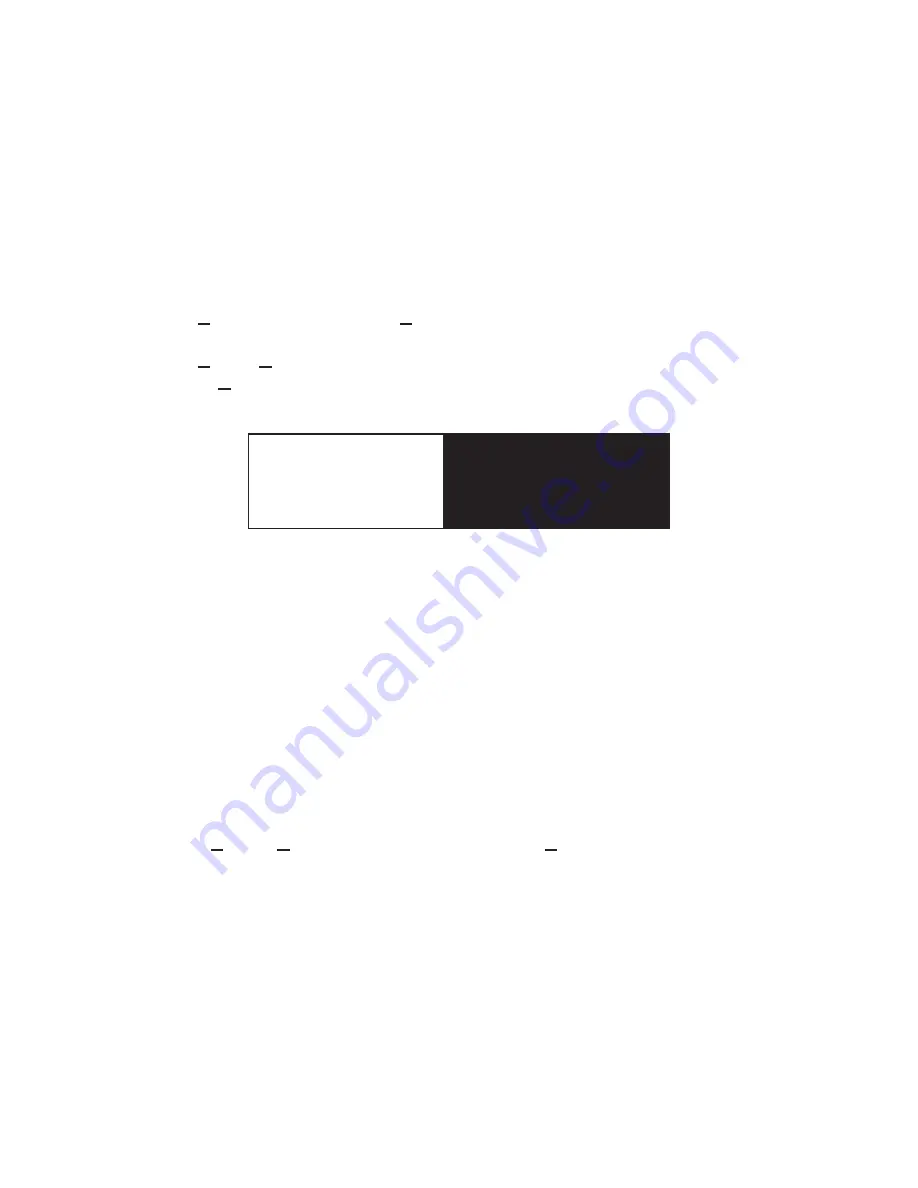
September 2012
L010194
31
Troubleshooting
Problem:
Can not establish communications with the controller.
Possible Solutions:
1. Make sure the controller has power. Is the controller’s Green LED on?
2. Check RS485 connections.
3. Check for loose cable connection either on the controller or COM Port.
4. Was the software installed successfully?
5. Go to
S
etup│Communication
Settings
and verify COM Port and baud rate settings.
6. Physically verify that the axis address matches with the controller unit selected address.
7. Go to
S
etup│
Axis
and verify address settings are the same.
8. Click on
Connect
icon to communicate with the controller.
9. If problems still exist, contact Anaheim Automation Tech Support.
Problem:
There is no power to the controller.
Possible Solutions:
1. Is the driver connected to the appropriate power supply?
2. Check the driver pack’s fuse.
3. If problems still exist, contact Anaheim Automation, Inc. Tech Support.
Problem:
My program won’t “Autostart”.
Possible Solutions:
1. Verify that the Autostart Function has been enabled.
2. Go to
S
etup│
Autostart Program
and Click on
Enable
.
3. If problems still exist, contact Anaheim Automation Tech Support.
Section 5: Troubleshooting
Anaheim Automation, Inc.
Tech Support:
4985 E Landon Drive
Anaheim, CA, 92807
Phone: (714) 992-6990
Fax: (714) 992-0471
www.anaheimautomation.com
July 2018