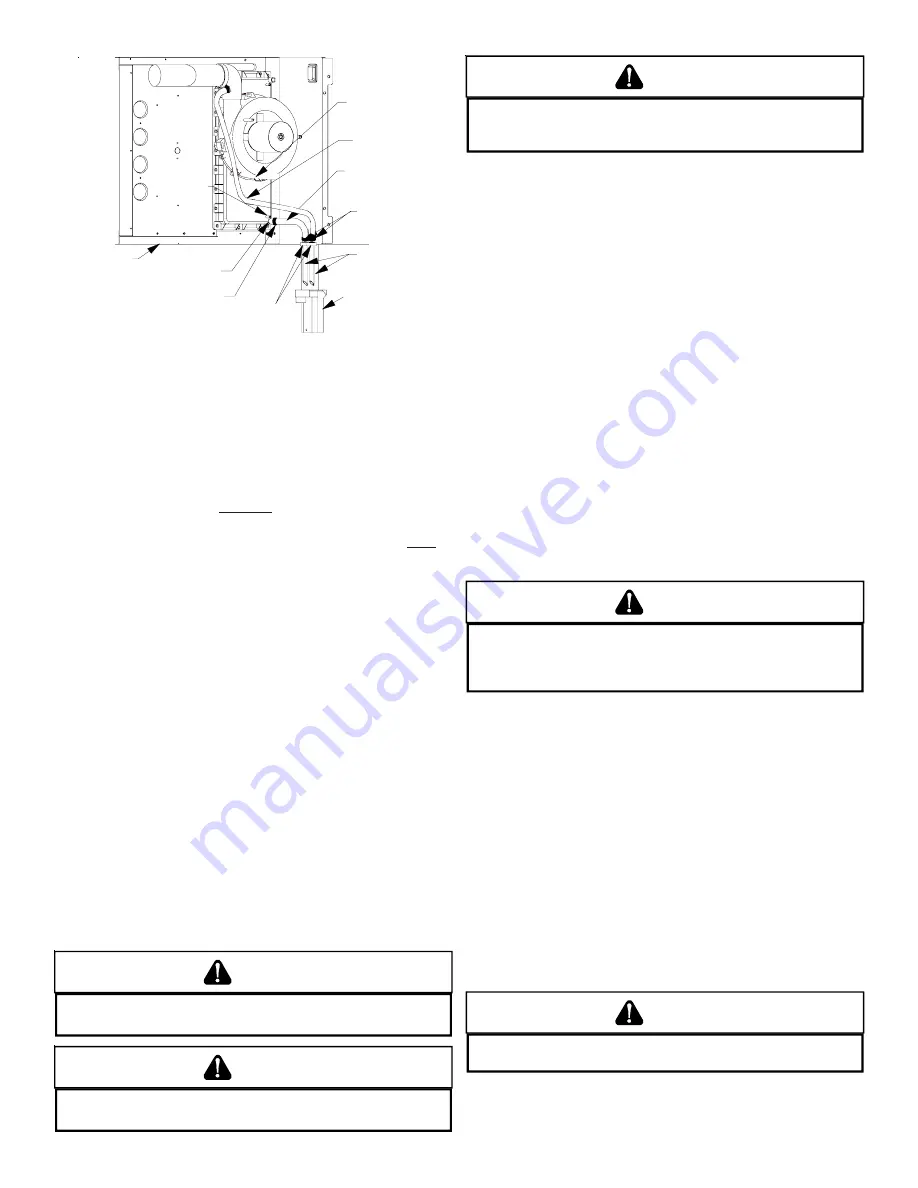
21
LEFT SIDE
PANEL
FRONT COVER
DRAIN PORT
SIDE PANEL
GROMMET
HOLES
DRAIN TRAP
TUBE(S) 2
GREEN HOSE
CLAMPS
(3 PLACES)
HOSE A
HOSE B
INDUCED
DRAFT BLOWER
DRAIN PORT
FRONT
COVER
PRESSURE
TAP
RED HOSE CLAMP
Horizontal Connections - Left Side Down
(Upflow Shown, Counterflow Similar)
4. Remove the rubber cap from the side drain port on the rubber
elbow.
5. Secure the short end of Hose B to rubber elbow side drain
port using a green hose clamp.
NOTE:
For left side drainage,
route hose to far left (down) side panel grommet holes.
NOTE:
Horizontal left side connections (when using new
side port drain elbow) does not require connecting a hose
to the induced draft blower housing.
6. Cut 5 1/2 inches straight length from the long end of each
Tube 2.
7. Insert approximately one inch of each Tube 2 through left
side panel grommet hole. Secure tubes to Hose A and
Hose B with a green hose clamps.
NOTE:
Tube must
reach bottom of trap. Ensure hoses and tubes maintain a
downward slope for proper drainage and that they are not
kinked or binding.
For details concerning mounting of the drain trap, refer to
Section
X, Condensate Drain Lines and Drain Trap - Upright Drain Trap
Mounting.
H
ORIZONTAL
D
RAIN
T
RAP
M
OUNTING
(L
EFT
OR
R
IGHT
S
IDE
P
ANEL
)
1. Position the drain trap against side panel with drain tubes
inserted into trap. Note that the trap may be orientated with
the outlet facing either the furnace’s top cover or base pan.
2. Secure drain trap to side panel at the dimples or crosshairs
located on either side of the grommet drain holes.
3. Confirm that tubes reach bottom of drain trap and that all
hoses maintain a downward slope and are not kinked or
binding.
4. Attach PVC drain line to drain trap outlet with either a 90°
elbow or coupling.
XI. ELECTRICAL CONNECTIONS
WARNING
T
O AVOID THE RISK OF ELECTRICAL SHOCK, WIRING TO THE UNIT MUST BE
POLARIZED AND GROUNDED.
WARNING
T
O AVOID INJURY, ELECTRICAL SHOCK OR DEATH, DISCONNECT ELECTRICAL
POWER BEFORE SERVICING OR CHANGING ANY ELECTRICAL WIRING.
CAUTION
L
ABEL ALL WIRES PRIOR TO DISCONNECTION WHEN SERVICING CONTROLS.
W
IRING ERRORS CAN CAUSE IMPROPER AND DANGEROUS OPERATION.
V
ERIFY PROPER OPERATION AFTER SERVICING.
W
IRING
H
ARNESS
The wiring harness is an integral part of this furnace. Field alteration
to comply with electrical codes should not be required. Wires are
color coded for identification purposes. Refer to the wiring dia-
gram for wire routings. If any of the original wire as supplied with
the furnace must be replaced, it must be replaced with wiring ma-
terial having a temperature rating of at least 105°C. Any replace-
ment wiring must be copper conductor.
115 V
OLT
L
INE
C
ONNECTIONS
Before proceeding with electrical connections, ensure that the sup-
ply voltage, frequency, and phase correspond to that specified on
the unit rating plate. Power supply to the furnace must be N.E.C.
Class 1, and must comply with all applicable codes. The furnace
must be electrically grounded in accordance with local codes or, in
their absence, with the latest edition of The National Electric Code,
ANSI NFPA 70 and/or The Canadian Electric Code CSA C22.1.
Use a separate fused branch electrical circuit containing properly
sized wire, and fuse or circuit breaker. The fuse or circuit breaker
must be sized in accordance with the maximum overcurrent protec-
tion specified on the unit rating plate. An electrical disconnect must
be provided at the furnace location.
NOTE:
Line polarity must be observed when making field
connections.
WARNING
I
N UPRIGHT UPFLOW INSTALLATIONS, THE DRAIN TRAP MUST BE MOUNTED ON
THE OPPOSITE SIDE OF THE UNIT FROM THE JUNCTION BOX.
T
HIS WILL
REDUCE THE RISK OF WATER REACHING THE JUNCTION BOX IN THE EVENT OF
A BLOCKED DRAIN CONDITION.
Connect hot, neutral, and ground wires as shown in the wiring
diagram located on the unit’s blower door. For direct vent applica-
tions, the cabinet opening to the junction box must be sealed air
tight using either a UL approved bushing such as Heyco Liquid
Tight or by applying a UL approved non-reactive sealant to bush-
ing.
Line polarity must be observed when making field connections. Line
voltage connections can be made through either the right or left side
panel. The furnace is shipped configured for a left side (right side for
counterflows) electrical connection with the junction box located in-
side the burner compartment. To make electrical connections
through the opposite side of the furnace, the junction box must be
relocated to the other side of the burner compartment prior to mak-
ing electrical connections. To relocate the junction box, follow the
steps shown below.
NOTE:
Wire routing must not to interfere with circulator blower
operation, filter removal, or routine maintenance.
CAUTION
E
DGES OF SHEET METAL HOLES MAY BE SHARP.
U
SE GLOVES AS A
PRECAUTION WHEN REMOVING HOLE PLUGS.
1. Remove the burner compartment door.