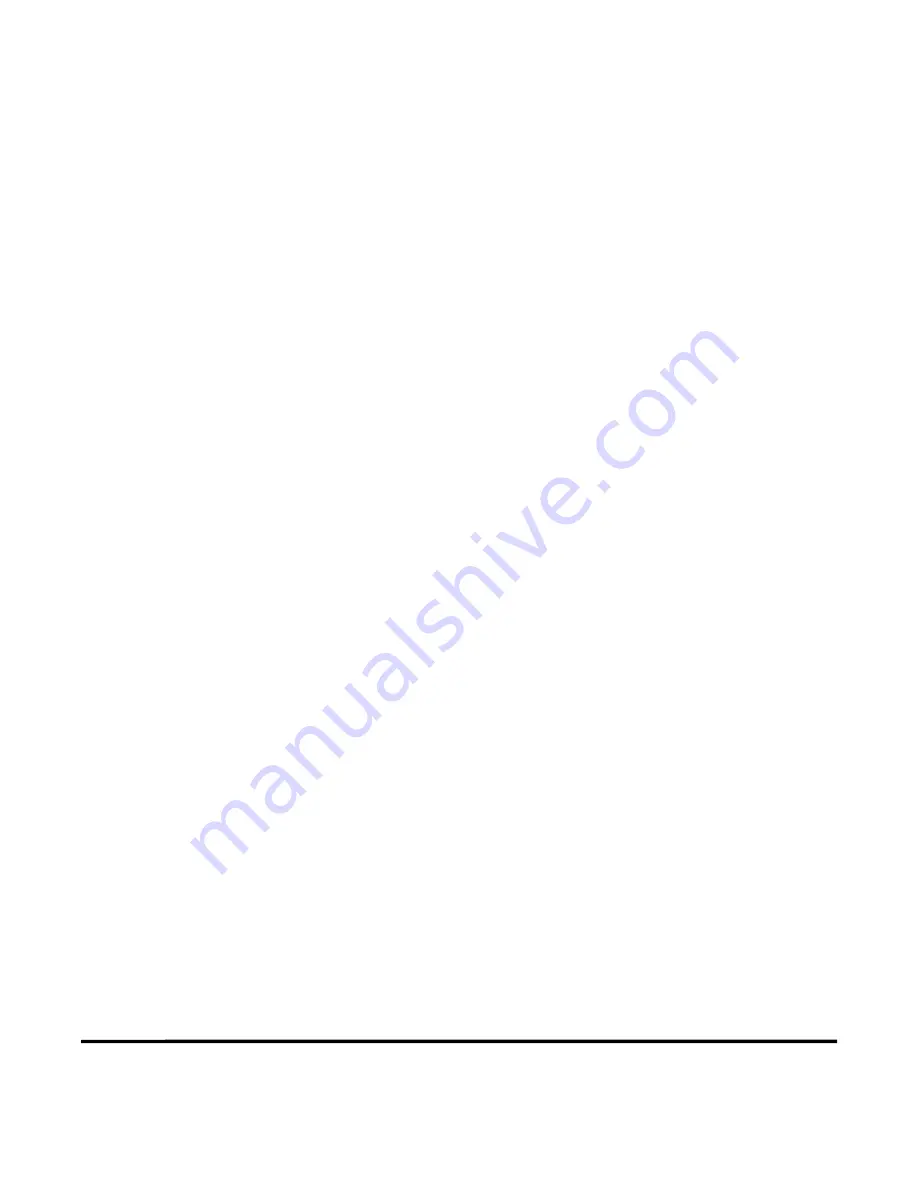
HF28 DC RESISTANCE WELDING SYSTEM
viii
990-372
CONTACT US
Thank you for purchasing a Miyachi Unitek™ Resistance Welding System Control.
Upon receipt of your equipment, please thoroughly inspect it for shipping damage prior to its
installation. Should there be any damage, please immediately contact the shipping company to file a
claim, and notify us at:
Amada Miyachi America
1820 South Myrtle Avenue
P.O. Box 5033
Monrovia, CA 91017-7133
Telephone: (626)
303-5676
FAX:
(626) 358-8048
e-mail: [email protected]
The purpose of this manual is to supply operating and maintenance personnel with the information
needed to properly and safely operate and maintain the Miyachi Unitek™ HF28 Resistance Welding
System Control.
We have made every effort to ensure that the information in this manual is accurate and adequate.
Should questions arise, or if you have suggestions for improvement of this manual, please contact us at
the above location/numbers.
Amada Miyachi America is not responsible for any loss due to improper use of this product.
Содержание 1-288-01
Страница 1: ...990 372 REV E DC RESISTANCE WELDING SYSTEM HF28 OPERATION MANUAL...
Страница 10: ...HF28 DC RESISTANCE WELDING SYSTEM x 990 372...
Страница 64: ......
Страница 88: ......
Страница 102: ......
Страница 114: ......
Страница 142: ......
Страница 144: ...AMADA MIYACHI AMERICA INC 1820 South Myrtle Ave Monrovia CA 91016 U S A TEL 1 626 303 5676 FAX 1 626 358 8048...