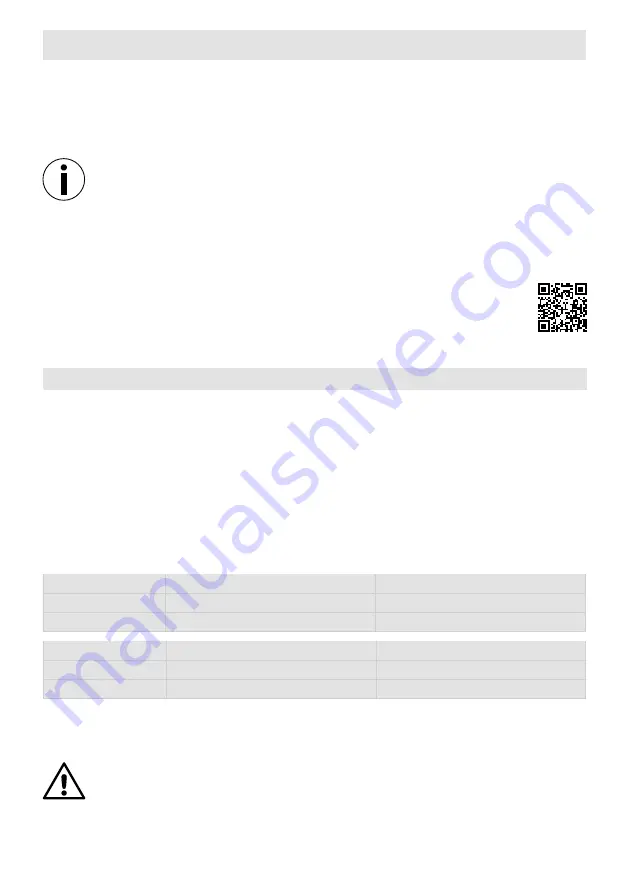
3
Operating instructions
(translation of original operating instructions)
Read the operating manual carefully before commissioning
and keep it on hand for later consultation.
We congratulate you on the purchase of a GEOSTAR wedge welder.
You have selected a first-class wedge welder comprised of high-quality materials. This device was developed and
produced in accordance with the latest welding technologies. Every GEOSTAR is subjected to strict quality monitor-
ing before it leaves the factory in Switzerland.
1. Use
For welding materials made of
PVC
, a device model designed for that purpose with a
steel wedge
must be used.
Additional materials upon request
More information about GEOSTAR and myLeister can be found at www.leister.com
GEOSTAR G5 LQS/G5
Material
Material thickness reference value
Copper
PE-HD, PE-LD, PP, TPO, FPO
0.8 – 3.0 mm
Steel
PVC-P
0.8 – 3.0 mm
GEOSTAR G7 LQS/G7
Material
Material thickness reference value
Copper
PE-HD, PE-LD, PP, TPO, FPO
1.0 – 3.0 mm
Steel
PVC-P
1.0 – 3.0 mm
GEOSTAR G5 LQS/G5
GEOSTAR G7 LQS/G7
Wedge welder
The GEOSTAR G5/G7 with and without LQS is designed for overlap welding of thermoplastic films and sealing
sheets. Only use original Leister spare parts and accessories; otherwise, any warranty and/or guarantee claims will
be invalidated.
Welding geometry
• The maximum overlap width of the lower and upper membranes is 150 mm.
• Welding seam widths 50 mm.
• Welding seam with/without test channel (depending on version).
1.1 Intended use
1.2 Non-intended use
Any other use or any use beyond the type of use described is deemed to be a non-intended use.