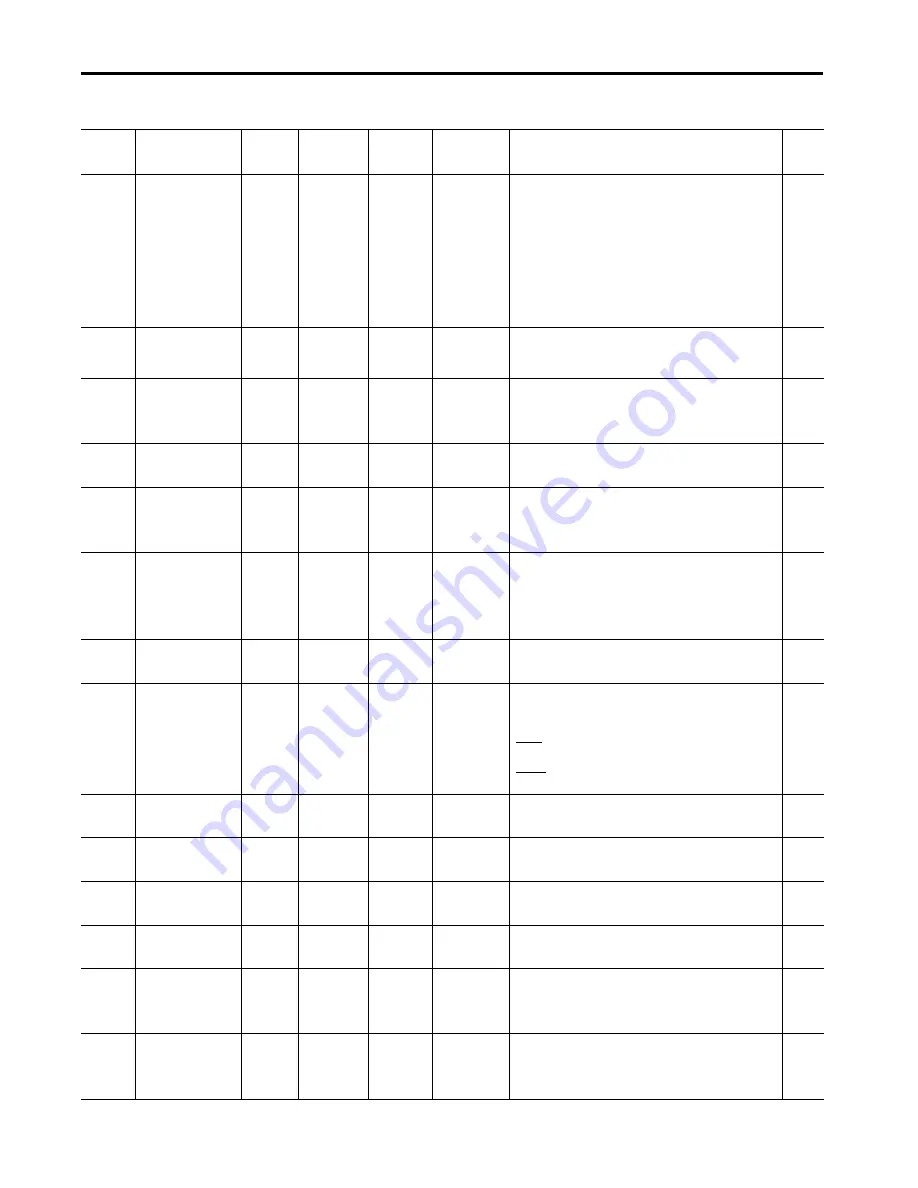
216
Rockwell Automation Publication 1560F-UM001A-EN-P - June 2019
Appendix A
Parameter Information
186
UTS Level
%
0/100
75
The SMC-50 has the ability to determine if the motor is up-to-
speed (UTS). If the SMC-50 encounters a problem detecting
motor UTS, this parameter can be modified by the user to
compensate. If the SMC-50 is detecting the UTS condition to
soon (e.g., abrupt speed change), this number should be
increased (this typically occurs on high efficiency motors). If the
SMC-50 is detecting the UTS condition to late or not at all
(display does not indicate At Speed), this number should be
lowered. Contact RA Technical Support for assistance.
R/W
187
Stall Level
%
0/100
75
Allows the user to set the motor winding voltage level (as a
percentage of line voltage) at which the SMC-50 will consider
the motor stalled.
R/W
188
Stall Delay
Secs
0/30
1.0
Allows the user to configure the time period after the start
maneuver start time that the motor has to reach UTS, or else a
stall fault will occur.
R/W
189
Stall Position
%
0/100
75
Allows the user to set the change in the notch position at which
the SMC-50 will consider the motor stalled.
R/W
190
Notch Maximum
(Pump Control)
50/70
60.0
Allows the user to change the maximum notch value during
pump stop. This parameter is not typically modified and it is
recommended that RA Technical Support be contacted for
assistance before attempting to do so.
R/W
191
Notch Position
%
40/100
87.5
Enables the user to make a manual adjustment to an internal
value used for notch control gain, which impacts the SMC-50
starting control algorithm. This parameter is not typically
modified and it is recommended that RA Technical Support be
contacted for assistance before attempting to do so.
R/W
192
Bypass Delay
Secs
2/10
2
During the coast to stop, the bypass contactor will be hold by
this number after the Main Contactor open.
R/W
194
Forced Tuning
0/1
1
FALSE
[TRUE]
Enables the controller's tuning algorithms to analyze the load
and supply and adjust parameters for easy set up and optimum
performance.
FALSE
: Do not run tuning algorithm (was already run or
disabled by user).
[TRUE]
: Run tuning algorithm at next start command
[Default].
R/W
195
Stator R
Ohms
0/50
0.00
Enables the user to read/view the motor stator resistance value
that was measured during the tuning process.
R
196
Total R
Ohms
0/50
0.00
Enables the user to read/view the motor total load resistance
that was measured during the tuning process.
R
197
Coupling Factor
0/10
0.00
This is a coefficient inserted by the controller during the tuning
process and viewable by the user.
R
198
Inductance
mH
0/1000
0.00
Enables the user to read/view the motor inductance that was
measured during the tuning process.
R
199
Speed Pgain
1/10000
1000
Provides the ability to adjust the gain factor used in speed
measurement algorithms. These parameters are not typically
modified and it is recommended that RA Technical Support be
contacted for assistance before attempting to do so.
R/W
200
Transient Mag
0/2
0.90
Provides the ability to adjust the gain factor used in speed
measurement algorithms. These parameters are not typically
modified and it is recommended that RA Technical Support be
contacted for assistance before attempting to do so.
R/W
Table 66 - SMC -50 Parameter List (Continued)
Number
Name
Unit
Min/Max
Default
Enum Text
Description
R/W
Содержание SMC-50
Страница 10: ...10 Rockwell Automation Publication 1560F UM001A EN P June 2019 Table of Contents Notes ...
Страница 12: ...12 Rockwell Automation Publication 1560F UM001A EN P June 2019 Preface Notes ...
Страница 68: ...68 Rockwell Automation Publication 1560F UM001A EN P June 2019 Chapter 2 Installation Notes ...
Страница 120: ...120 Rockwell Automation Publication 1560F UM001A EN P June 2019 Chapter 4 Programming Notes ...
Страница 130: ...130 Rockwell Automation Publication 1560F UM001A EN P June 2019 Chapter 5 Metering Notes ...
Страница 134: ...134 Rockwell Automation Publication 1560F UM001A EN P June 2019 Chapter 6 Optional HIM Operation Notes ...
Страница 144: ...144 Rockwell Automation Publication 1560F UM001A EN P June 2019 Chapter 7 Communications Notes ...
Страница 156: ...156 Rockwell Automation Publication 1560F UM001A EN P June 2019 Chapter 8 Diagnostics Notes ...
Страница 198: ...198 Rockwell Automation Publication 1560F UM001A EN P June 2019 Chapter 10 Maintenance Notes ...
Страница 240: ...240 Rockwell Automation Publication 1560F UM001A EN P June 2019 Appendix A Parameter Information Notes ...
Страница 242: ...242 Rockwell Automation Publication 1560F UM001A EN P June 2019 Appendix B Controller Duty Cycle Ratings Notes ...
Страница 250: ...250 Rockwell Automation Publication 1560F UM001A EN P June 2019 Appendix C 1560F and 1562F Relay Control Notes ...
Страница 280: ...280 Rockwell Automation Publication 1560F UM001A EN P June 2019 Appendix G Using DeviceLogix Notes ...
Страница 284: ...284 Rockwell Automation Publication 1560F UM001A EN P June 2019 Appendix H Spare Parts Notes ...
Страница 286: ...286 Rockwell Automation Publication 1560F UM001A EN P June 2019 Appendix I Accessories Notes ...
Страница 291: ......