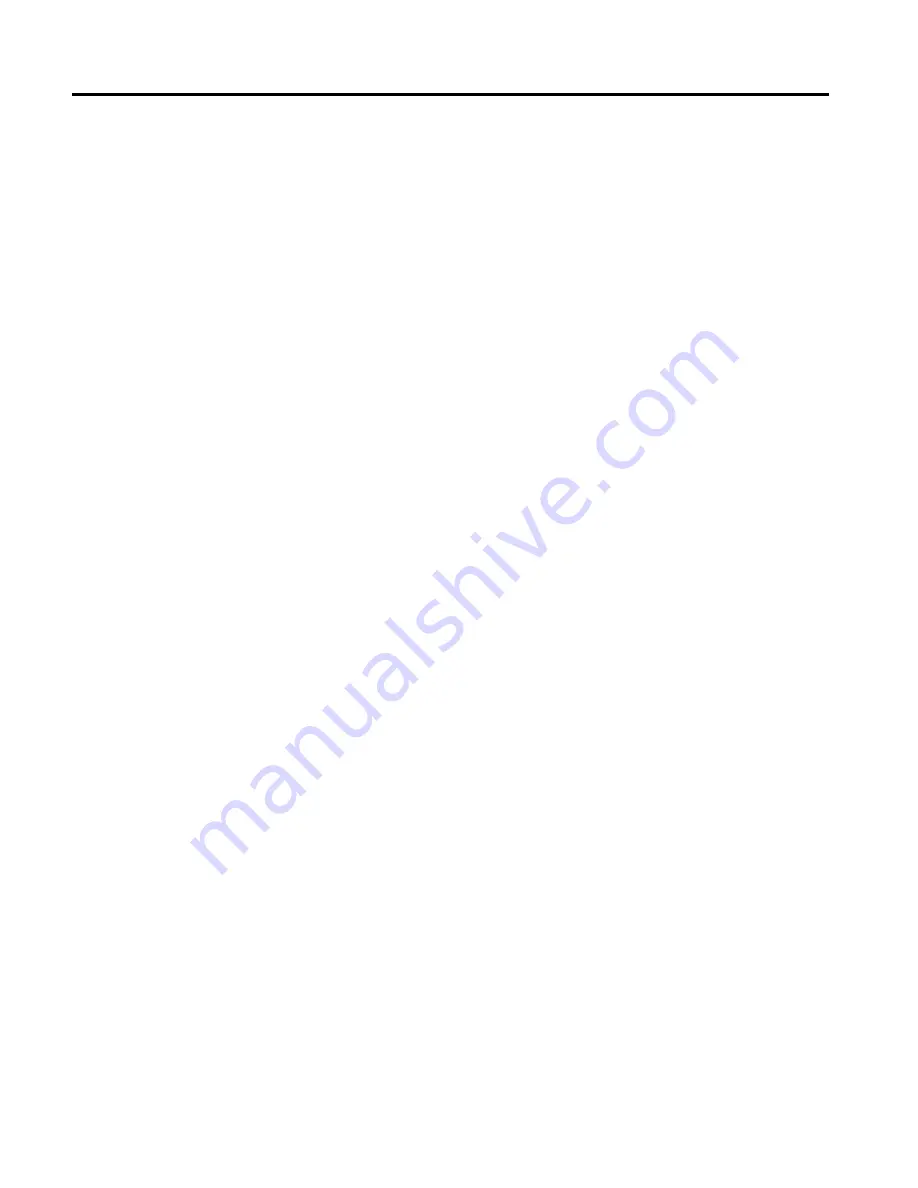
Chapter 2
Behavior models used in CIP Motion
84
Rockwell Automation Publication MOTION-RM003I-EN-P - February 2018
Basic Volts/Hertz Operation
There are a number of attributes that are used to specify the relationship the drive
device uses between output frequency (speed) and output voltage for a given
(induction) motor.
The Break Frequency and Break Voltage attributes define the point on the
Volts/Hertz curve below which the Start Boost feature is applied. As the name
indicates, Start Boost is used to provide a non-zero output voltage to the motor at
stand-still to assist startup.
The contribution of Start Boost to the output voltage of the drive device tapers off
to zero when the motor reaches the Break Frequency. Above the break point,
output voltage and output frequency follow a linear slope to the point defined by
the Motor Rated Frequency and Motor Rated Voltage. From this point on, the
Volts/Hertz curve follows another linear slope to the point defined by the Max
Frequency and Max Voltage attributes. This segment of the Volts/Hertz curve
allows for operation above the rated frequency and voltage of the motor in
applications where that is required.
Sensorless Vector Operation
Sensorless Vector is an alternative Velocity Control Method that does not require
configuration of a Volts/Hertz curve. Instead, by knowing the Stator Resistance
and Leakage Inductance of the motor, the drive device can calculate the
appropriate Output Voltage required for a given Output Frequency. This method
provides better low speed Velocity Control behavior than by using the Basic
Volts/Hertz method.
Slip Compensation
When driving an induction motor at a specific frequency, the actual motor
velocity is generally less than the command speed, given by the output frequency
divided by the motor pole count, by an amount that is proportional to the load
torque applied to the motor. This difference in speed is called 'Slip' and is a
configuration attribute associated with the motor. The Motion Device Axis
Object supports a Slip Compensation feature that is common to Variable
Frequency Drives. The amount of Slip Compensation applied to the Velocity
Reference is the product of the measured torque producing current, Iq, and the
configured Induction Motor Rated Slip Speed.
Velocity Droop
Another feature defined for the Frequency Control method is the droop function.
The droop function reduces the velocity reference by a scaled fraction of the
torque producing current, Iq, as controlled by the droop gain setting, Kdr. As
torque loading on the motor is increased, actual motor speed is reduced in
Содержание Kinetix 5500
Страница 10: ......
Страница 86: ......
Страница 470: ......
Страница 496: ...Index 496 Rockwell AutomationPublicationMOTION RM003I EN P February 2018 D device functioncodes 96 E exceptions 496 ...