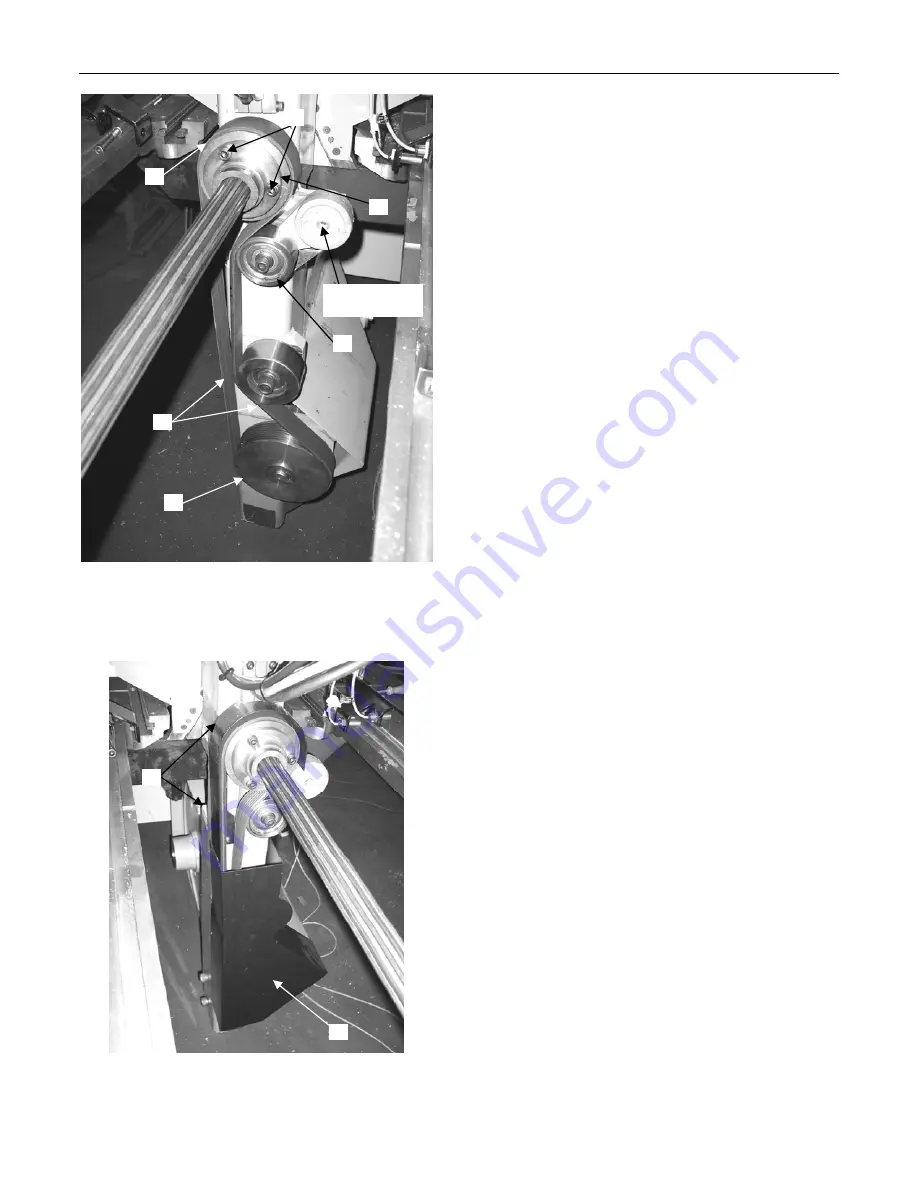
MARVEL 8 MARK III
MAINTENANCE
G-22
© MARVEL MFG. CO., INC. MANUAL 8SDN10871N (04/08)
A – Final Drive Belt
B – Spring Loaded Belt
Tensioner
C – Bevel Gear Belt Pulley
D – Pivot Belt Pulley
E – 3 Bolts (attach the Spline
Hub)
F – Spline Hub
G1 – Upper Drive Belt Guard
G2 – Lower Drive Belt Guard
D
C
A
E
F
Tensioner
Adjustment Bolt
B
G1
G2
Содержание marvel 8 mark III Series
Страница 6: ...This page intentionally left blank...