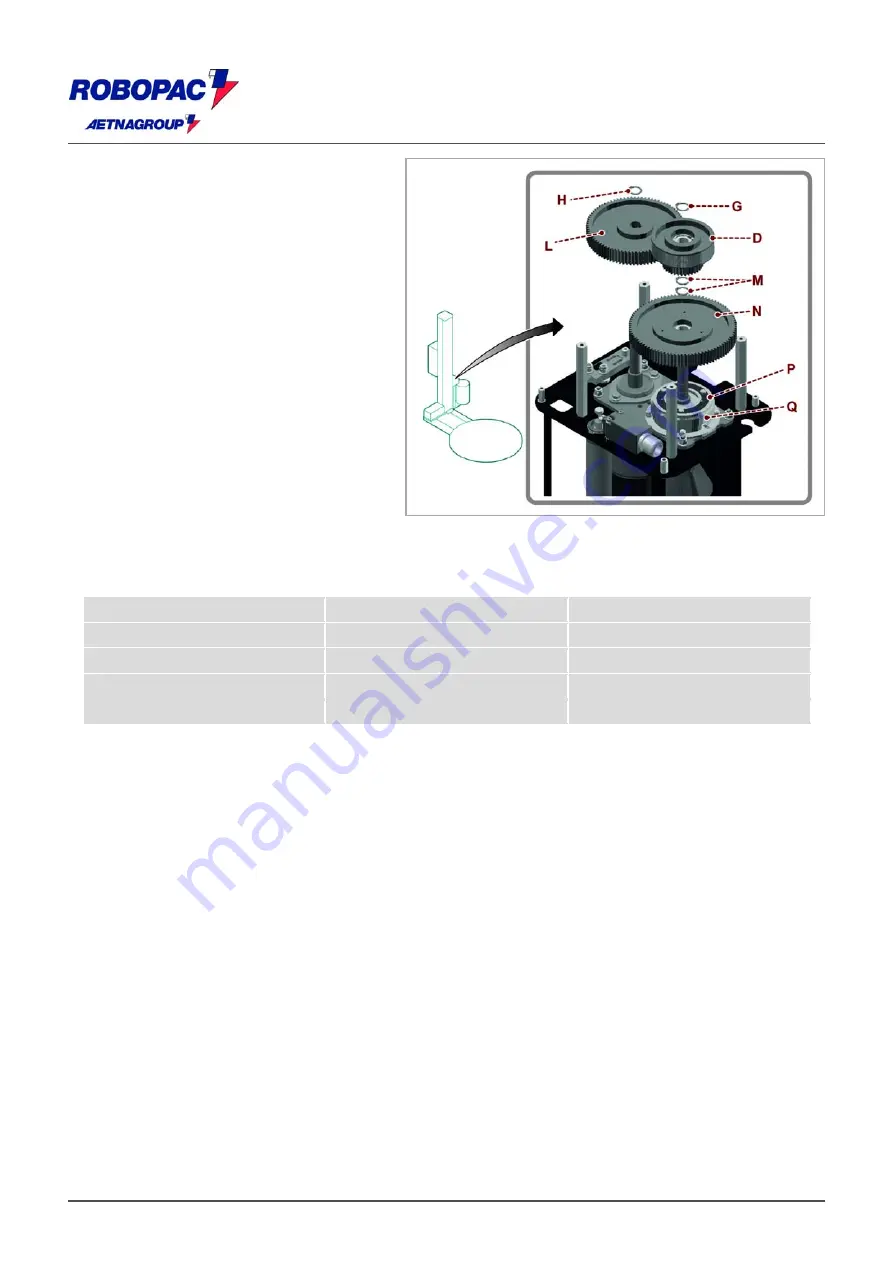
TECHNOPLAT CS/CW
TECHNOPLAT CS/CW TP
7.
Remove the stopping ring
(G)
.
8.
Remove the pulley
(D)
.
9.
Remove the stopping ring
(H)
.
10.
Remove the gear
(L)
.
11.
Remove the stopping ring
(M)
.
12.
Remove the gear
(N)
.
13.
Loosen the screws and remove the small
plate
(P)
from the gear
(N)
.
14.
Select the couple of gears
(L-N)
relating
to the pre-stretch percentage involved
(see the table).
The table lists the pre-stretch values obtainable with the relevant driving ratio.
|
Important
Set the pre-stretch depending on the resistance and the quality of the coating to obtain low consumption.
Pre-stretch percentage
Gear code (L)
Gear code (N)
150%
(∗)
(∗)
200%
(∗)
(∗)
250%
(∗)
(∗)
300%
(∗)
(∗)
(∗)
See spare parts catalogue.
15.
Assembly the small plate and correctly fix it to the gear of the new driving ratio.
16.
Assembly the gear of the new driving ratio.
17.
Position the gear with the side of the small plate coupled to the friction.
18.
Assembly the stopping ring.
19.
Assembly the gear of the new driving ratio.
20.
Assembly the stopping ring.
21.
Assembly the pulley.
22.
Assembly the stopping ring.
|
Important
During re-assembly remember to pay attention to the proper insertion of the coupling tabs.
43/79