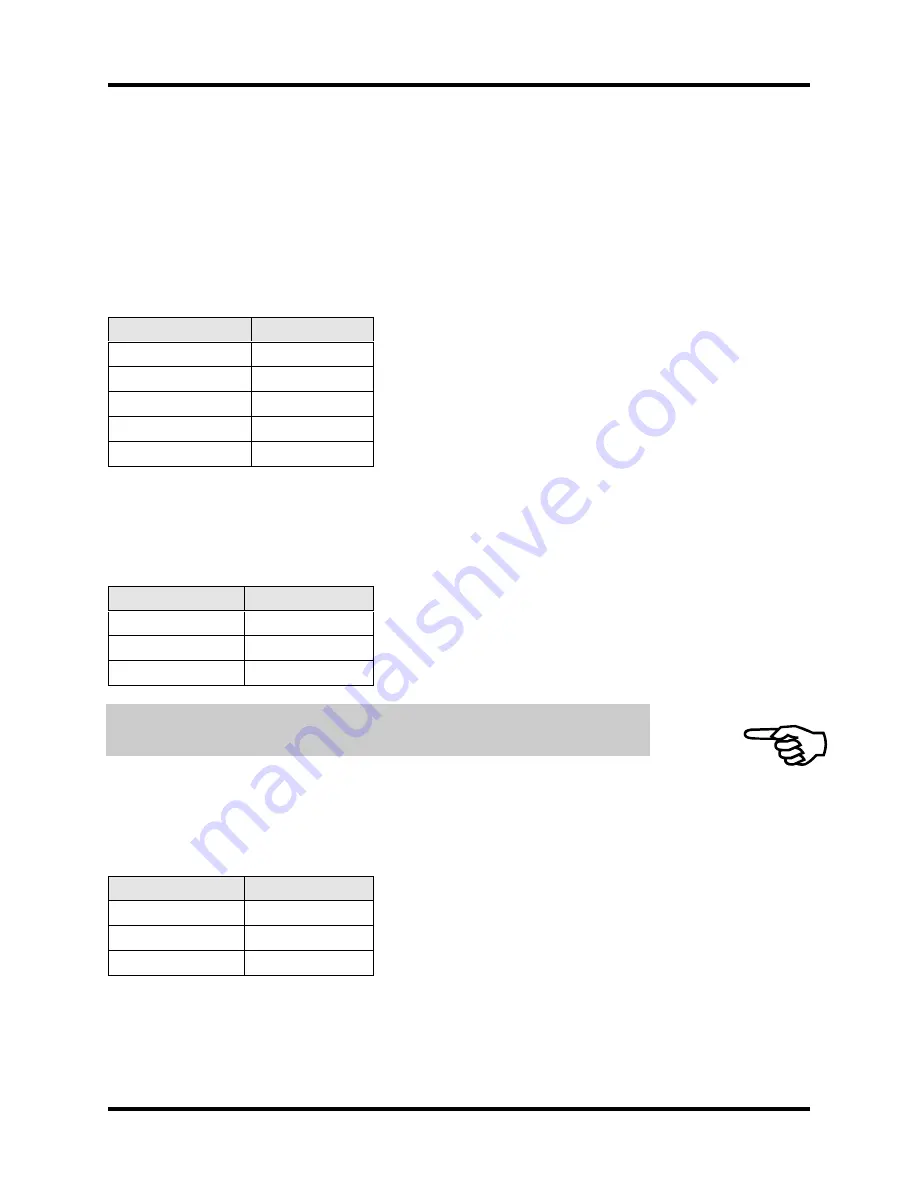
BA Intellidrive User’s Manual
Parameters
Version 1.4
Aerotech, Inc.
4-25
4.3.
Limit Parameters
4.3.1. PRM:60 Limit Check
This parameter determines whether or not the limits should be checked during motion. If
PRM:60=0, no limits are checked and homing is not allowed. If PRM:60=1, limits are
checked and homing is allowed. If PRM:60=2, limits are not checked, but homing is
allowed. Refer to Table 4-47 for parameter settings.
Table 4-47.
Settings for Limit Check PRM:60
PRM:60
Settings
Default Value
1 (enabled)
Maximum Value
2
Minimum Value
0
Type
Long (32bit)
Units
-
4.3.2. PRM:61 Limit Type
This parameter defines the polarity of the hardware limits. Refer to Table 4-48 for
parameter settings.
Table 4-48.
Settings for Limit Type PRM:61
PRM:61
Settings
Default
0
Active High
1
Active Low
0
Requires a reset (CTRL-D) before taking effect.
4.3.3. PRM:62 Home Direction
This is the initial direction the axis takes to seek the home limit switch. Refer to
Table 4-49 for parameter settings.
Table 4-49.
Settings for Home Direction PRM:62
PRM:62
Settings
Default
0
CCW
0
CW
1
Artisan Technology Group - Quality Instrumentation ... Guaranteed | (888) 88-SOURCE | www.artisantg.com