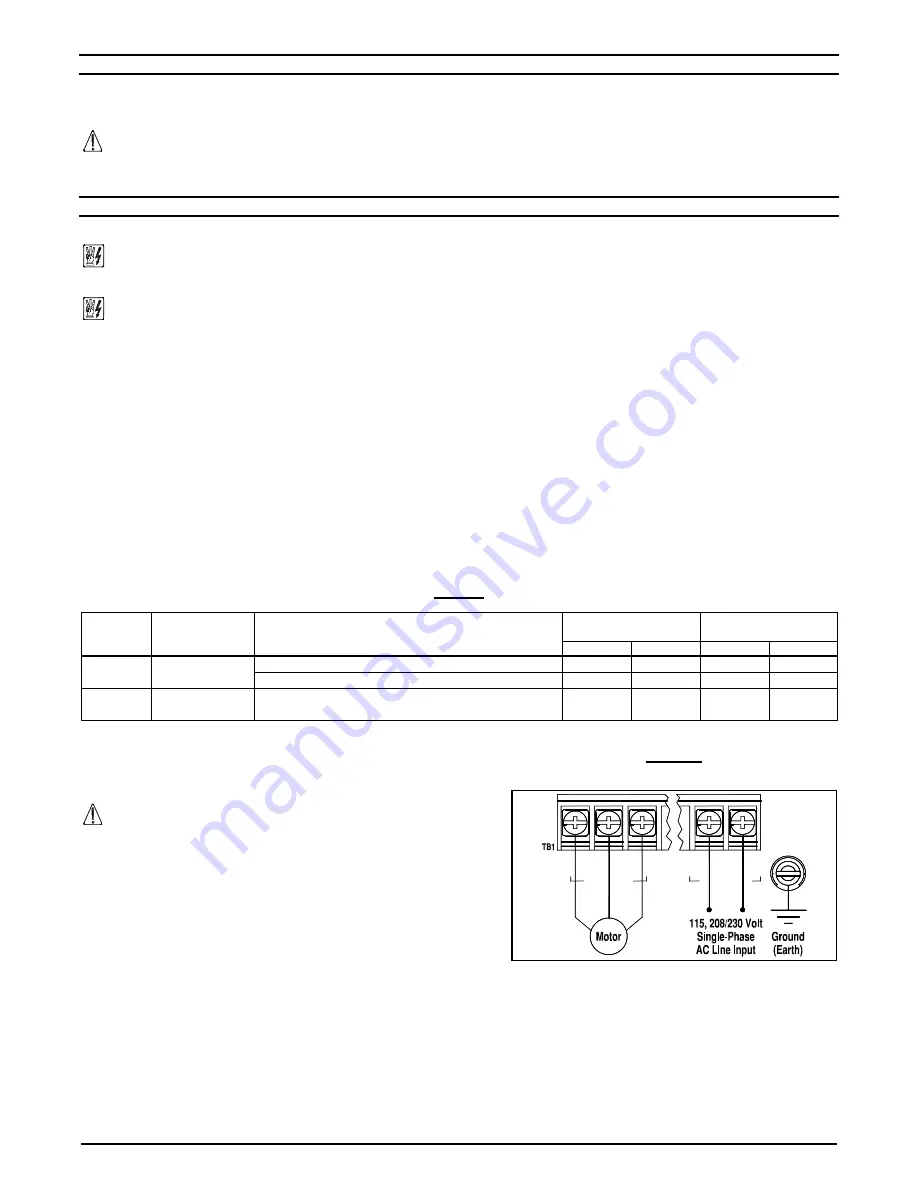
ASD SERIES INSTALLATION AND OPERATION MANUAL
13
6
–
AC LINE INPUT FUSING
The drive does not contain line fuses. Most electrical codes require that each ungrounded conductor contain circuit protection. Do not fuse
neutral or ground connections. It is recommended to install a fuse (Littelfuse 312/314, Buss ABC, or equivalent) or a circuit breaker in series
with each ungrounded conductor. Do not fuse motor leads. For the recommended fuse size, see Table 2 on page 7.
CAUTION!
Do not fuse neutral or grounded connections.
7
–
ELECTRICAL CONNECTIONS
Wire the drive in accordance with the National Electrical Code requirements and other local codes that may apply to the application.
WARNING!
Read Safety Warnings, on page 5, before using the drive. Disconnect main power before making connections to the drive.
To avoid electric shock, be sure to properly ground the drive.
WARNING! HIGH VOLTAGE! REMOTE CONNECTIONS OF POTENTIOMETER, SWITCHES, ETC., MAY HAVE WIRING THAT IS AT
LINE POTENTIAL.
Be sure to properly fuse each AC Line conductor that is not at ground potential. Do not fuse neutral or grounded conductors. A separate AC
Line switch or contactor must be wired as a disconnect so that each ungrounded conductor is opened. For fuse or circuit breaker selection, see
Table 1 on page 7. Also see Section 6.
To maintain the watertight integrity of the drive, be sure to use suitable liquidtight fittings and wiring which are appropriate for the application.
Liquidtight Fittings Kits are available for all models.
The drive is designed with a hinged case so that when the front cover is open, all wiring stays intact. To open the cover, the four screws must
be loosened so they are no longer engaged in the case bottom. After mounting and wiring, close the cover making sure that the wires do not
get caught or crimped as the cover is closed. Tighten the four screws so that the gasket is slightly compressed. The recommended tightening
torque is 12 in-lbs (14 kg-cm)
– do not overtighten. See Figures 7 and 8 on pages 11 and 12 for the tightening sequence.
Application Note:
To avoid erratic operation, do not bundle the AC Line and motor wires with each other or with wires from signal following,
start/stop contacts, or any other signal wires. Also, do not bundle motor wires from multiple drives in the same conduit. Use shielded cables on
all signal wiring over 12" (30 cm). The shield should be earth grounded on the drive side only. Wire the drive in accordance with the National
Electrical Code requirements and other local codes that may apply.
TABLE 3
DRIVE TERMINAL BLOCK WIRE SIZE AND TIGHTENING TORQUE SPECIFICATIONS
Terminal
Block
Description
Model
Maximum
Wire Size (Cu)
Recommended
Tightening Torque
AWG
mm
2
in-lbs
kg-cm
TB1
AC Line Input and
Motor Wiring
ASD-24D
12
3.3
7
8
ASD-27D, 29, 29 (1P), 45, 48
12
3.3
12
14
TB2
Run/Fault Relay
Output Contacts
ASD-24D, 27D, 29, 29 (1P), 45, 48
14
2.08
3.5
4
7.1
– AC LINE INPUT CONNECTION
Connect the AC Line input to Terminal Block TB1. See Figures 9 and 10 on
pages 13 and 14.
CAUTION!
The rated AC Line voltage of the drive must match the actual
AC Line input voltage. On ASD-24D, 27D the setting of Jumper J1 must match
the AC Line input voltage.
ASD-24D, 27D:
Designed to accept 1-phase AC Line input only (Terminals L1,
L2). Rated for 208/230 Volt AC Line input with Jumper J1 set to the "230V"
position (factory setting). Rated for 115 Volt AC Line input with Jumper J1 set to
the "115V" position. See Figure 9.
ASD-29 (1P):
Designed to accept 1-phase AC Line input (Terminals L1, L2).
Rated for 208/230 Volt AC Line input only. See Figure 9.
ASD-29:
Designed to accept 1-phase (Terminals L1, L2) or 3-phase (Terminals L1, L2, L3) AC Line input. Rated for 208/230 Volt AC Line input
only. See Figure 10 on page 14.
ASD-45, 48:
Designed to accept 3-phase AC Line input only (Terminals L1, L2, L3). Rated for 400/460 Volt AC Line input only. See Figure 10
on page 14.
FIGURE 9
ASD-24D, 27D, 29 (1P)
AC LINE INPUT, MOTOR, AND GROUND CONNECTIONS