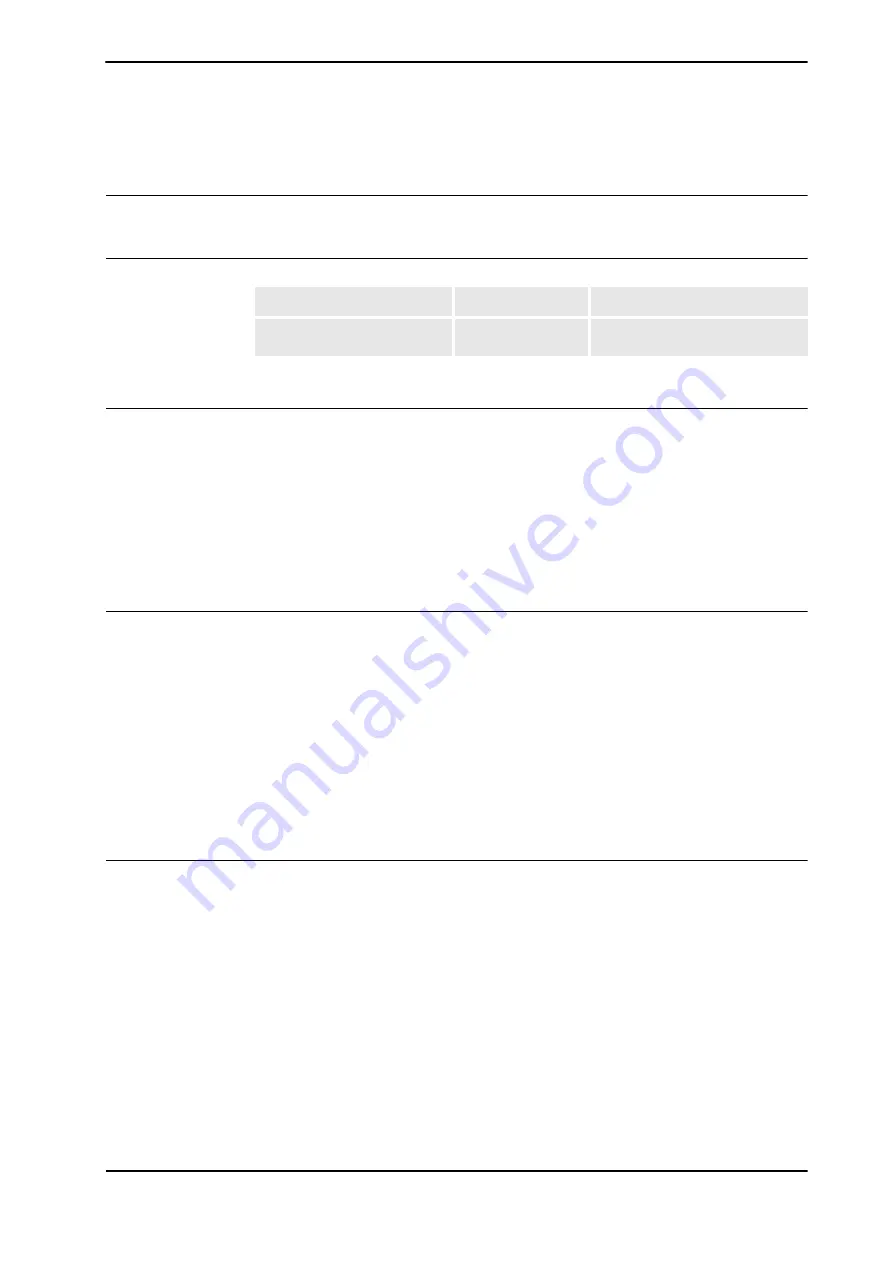
4 Repair
4.2.2. Mounting instructions for bearings
113
3HAC022032-001 Revision: E
© Copyri
ght
200
4-2008 ABB.
All rights reserved.
4.2.2. Mounting instructions for bearings
General
This section details how to mount and grease different types of bearings on the robot.
Equipment
Assembly of all bearings
Follow the instructions below when mounting a bearing on the robot.
1. To avoid contamination, let a new bearing remain in its wrapping until it is time for fitting.
2. Ensure that all parts included in the bearing fitting are free from burrs, grinding waste and
other contamination. Cast components must be free from foundry sand.
3. Bearing rings, inner rings and roller elements must under no circumstances be subjected
to direct impact. Furthermore, the roller elements must not be exposed to any stresses
during the assembly work.
Assembly of tapered bearings
Follow the previous instructions for assembly of all bearings, when mounting a tapered
bearing on the robot.
In addition to those instructions, the procedure below must be carried out to enable the roller
elements to adjust to the correct position against the race flange.
1. Tension the bearing gradually until the recommended pre-tension is achieved.
Note! The roller elements must be rotated a specified number of turns before pre-
tensioning is carried out and also rotated during the pre-tensioning sequence.
2. Make sure the bearing is properly aligned, as this will directly affect the lifespan of the
bearing.
Greasing of bearings
The bearings must be greased after assembly, according to instructions below:
•
The bearings must not be completely filled with grease. However, if space is available
beside the bearing fitting, the bearing may be totally filled with grease when mounted,
as excessive grease will be pressed out from the bearing when the robot is started.
•
During operation, the bearing should be filled to 70-80% of the available volume.
•
Ensure that grease is handled and stored properly, to avoid contamination.
Grease the different types of bearings as detailed below:
•
Grooved ball bearings must be filled with grease from both sides.
•
Tapered roller bearings and axial needle bearings must be greased in the split
condition.
Equipment, etc.
Art. no.
Note
Grease
3HAB 3537-1
Used to grease the bearings, if not
specified otherwise.
Содержание IRB 4400 - 45
Страница 2: ......
Страница 8: ...Table of Contents 6 3HAC022032 001 Revision E Copyright 2004 2008 ABB All rights reserved ...
Страница 236: ...4 Repair 4 9 2 Repair routines 3HAC022032 001 Revision E 234 Copyright 2004 2008 ABB All rights reserved ...
Страница 256: ...Product documentation M2004 3HAC022032 001 Revision E 254 Copyright 2004 2008 ABB All rights reserved ...
Страница 294: ...7 Part list 7 5 Position switch axis 1 3HAC022032 001 Revision E 292 Copyright 2004 2008 ABB All rights reserved ...
Страница 296: ......
Страница 297: ... Copyright 2004 2006 ABB All rights reserved Foldout 1 ...
Страница 298: ... Copyright 2004 2006 ABB All rights reserved Foldout 2 ...
Страница 299: ... Copyright 2004 2006 ABB All rights reserved Foldout 3 1 ...
Страница 301: ... Copyright 2004 2006 ABB All rights reserved Foldout 4 ...
Страница 302: ... Copyright 2004 2006 ABB All rights reserved Foldout 5 ...
Страница 303: ... Copyright 2004 2006 ABB All rights reserved Foldout 6 1 ...
Страница 304: ... Copyright 2004 2006 ABB All rights reserved Foldout 6 2 ...
Страница 305: ... Copyright 2004 2006 ABB All rights reserved Foldout 6 3 ...
Страница 306: ... Copyright 2004 2006 ABB All rights reserved 4 3 9 R1 SMB R2 SMB R1 G 8 5 7 3hab 3365 1 x Seriemätenhet Foldout 7 ...
Страница 307: ... Copyright 2004 2006 ABB All rights reserved Foldout 8 ...
Страница 309: ...9 Circuit diagram 8 1 Introduction 3HAC022032 001 Revision E 296 Copyright 2004 2008 ABB All rights reserved ...
Страница 311: ... Copyright 2004 2006 ABB All rights reserved List of Contents Location of Connection Point Sheet 101 ...
Страница 312: ... Copyright 2004 2006 ABB All rights reserved Brake Release Unit Serial Measurement Board Sheet 102 ...
Страница 313: ... Copyright 2004 2006 ABB All rights reserved Motor Axis 1 3 Sheet 103 ...
Страница 314: ... Copyright 2004 2006 ABB All rights reserved Feed Back Axis 1 3 Sheet 104 ...
Страница 315: ... Copyright 2004 2006 ABB All rights reserved Motor Axis 4 6 Sheet 105 ...
Страница 316: ... Copyright 2004 2006 ABB All rights reserved Feed Back Axis 4 6 Sheet 106 ...
Страница 317: ... Copyright 2004 2006 ABB All rights reserved Customer Connection Sheet 107 ...
Страница 318: ... Copyright 2004 2006 ABB All rights reserved Pos Indicator Axis 1 Option Sheet 108 ...
Страница 321: ......
Страница 322: ...ABB Robotics S 721 68 VÄSTERÅS SWEDEN Telephone 46 0 21 344000 Telefax 46 0 21 132592 3HAC 022032 001 Revision E en ...