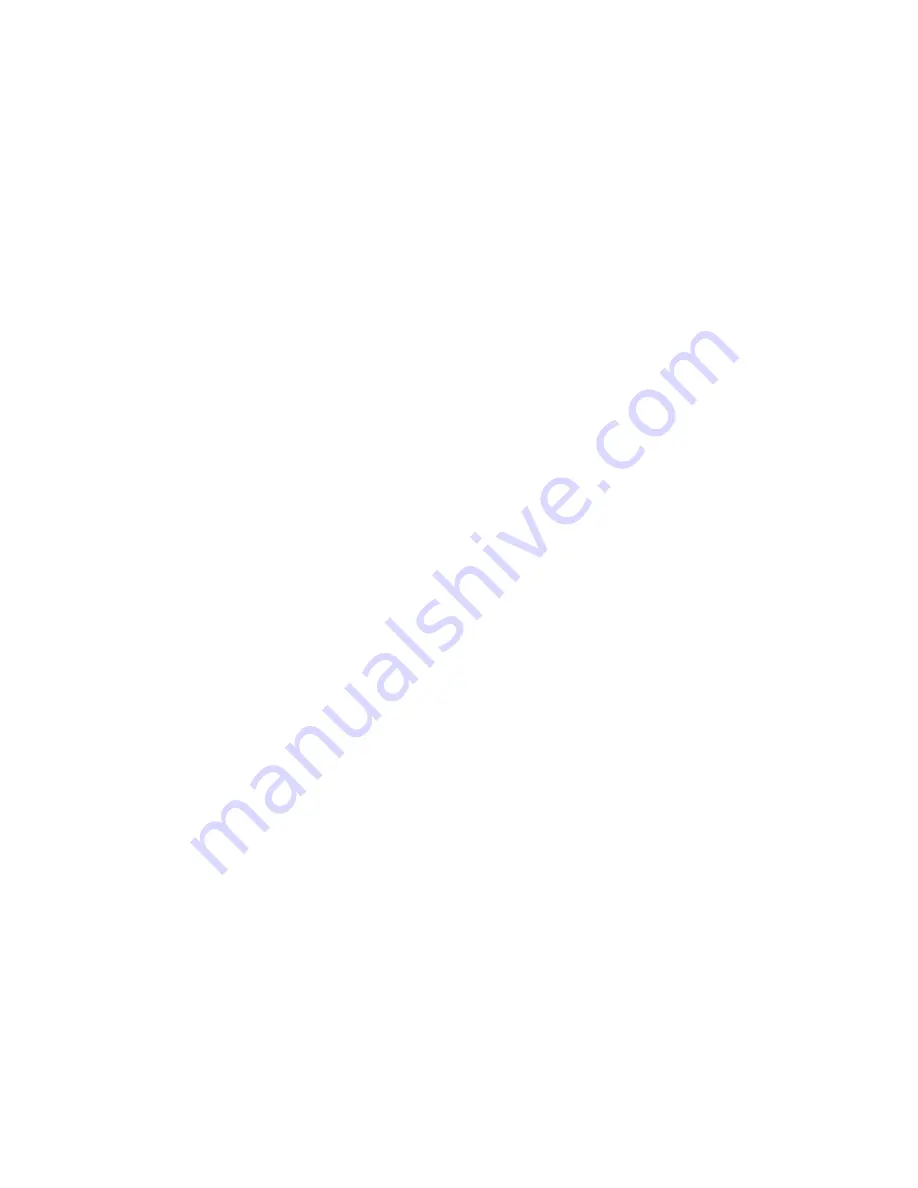
II K 4-38
Overview of Software
Speed controller
Attention: Motor will accelerate twice to 80% of
Base Speed now
Autotuning
• On the panel press button LOC; LOC is dis-
played in the panel status row.
• Select parameter
Contr Service (7.02)
=
Sp
Autotun
and confirm with ENTER.
• Within the next 30 seconds press the (I) button
on the panel. This starts the autotuning proce-
dure.
• Main contactor is switched On and motor will
start turning.
The autotuning procedure is successfully finished if
the panel displays the message
None
.
• Main contactor is switched Off.
After successful autotuning the following controller
parameters are set:
Speed Reg KP (5.07)
Speed controller proportional gain
Speed Reg TI (5.08)
Speed controller integral time constant
If the autotuning procedure failed the alarm message
Autotuning Failed
(A10)
is displayed. Detailed infor-
mation for the failure reason can be read from param-
eter
Diagnosis (7.03)
. More explanations to the diag-
nosis messages are available in the chapter Trouble-
shooting.
Pressing the LOC button on the panel again the
control is switched back to the input/output terminals.
The LOC message in the panel status row disap-
pears.
Flux adaptation
Attention: Motor will accelerate to 50% of Base
Speed now
Autotuning
• On the panel press button LOC; LOC is dis-
played in the panel status row.
• Select parameter
Contr Service (7.02)
=
Flux
Adapt
and confirm with ENTER.
• Within the next 30 seconds press the (I) button
on the panel. This starts the autotuning proce-
dure.
• Main contactor is switched On and motor will
start turning.
The autotuning procedure is successfully finished if
the panel displays the message
None
.
• Main contactor is switched Off.
After successful autotuning the following controller
parameters are set:
Field Cur 40% (4.07)
Field current for 40% flux
Field Cur 70% (4.08)
Field current for 70% flux
Field Cur 90% (4.09)
Field current for 90% flux
If the autotuning procedure failed the alarm message
Autotuning Failed
(A10)
is displayed. Detailed infor-
mation for the failure reason can be read from param-
eter
Diagnosis (7.03)
. More explanations to the diag-
nosis messages are available in the chapter Trouble-
shooting.
Pressing the LOC button on the panel again the
control is switched back to the input/output terminals.
The LOC message in the panel status row disap-
pears.
Thyristor diagnosis
(Motor does not turn)
Self diagnosis
• On the panel press button LOC; LOC is dis-
played in the panel status row.
• Select parameter
Contr Service (7.02)
=
Thyr
Diag
and confirm with ENTER.
• Within the next 30 seconds press the (I) button
on the panel. This starts the self-diagnosis
procedure.
• Main contactor is switched On.
The thyristor diagnosis procedure is successfully
finished if the panel displays the message
None
. That
means no defective thyristor(s) were detected.
• Main contactor is switched Off.
If the diagnosis procedure failed the fault message
Hardware Fault
(F02)
is displayed. Detailed informa-
tion for the failure reason can be read from parameter
Diagnosis (7.03)
. More explanations to the diagnosis
messages are available in the chapter Troubleshoot-
ing.
Pressing the LOC button on the panel again the
control is switched back to the input/output terminals.
The LOC message in the panel status row disap-
pears.
Содержание DCS 400
Страница 1: ...II K 1 1 DCS Thyristor power converter for DC drive systems 20 to 1000 A 9 to 522 kW Manual DCS 400 ...
Страница 24: ...II K 3 14 Technical data ...
Страница 29: ...II K 4 5 Overview of Software ...
Страница 158: ...II K 6 36 Operating Instructions ...
Страница 181: ...II K B 1 Appendix B Declaration of conformity ...
Страница 190: ...Notices ...
Страница 191: ...Notices ...